- May 8, 2025
- Posted by: feinuojixie
- Category: Injection Molding News
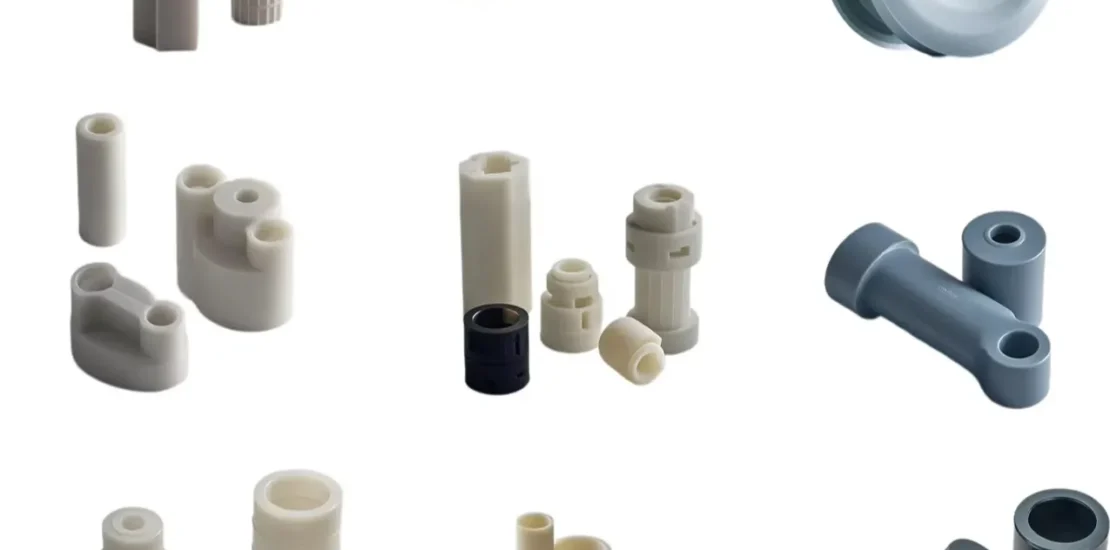
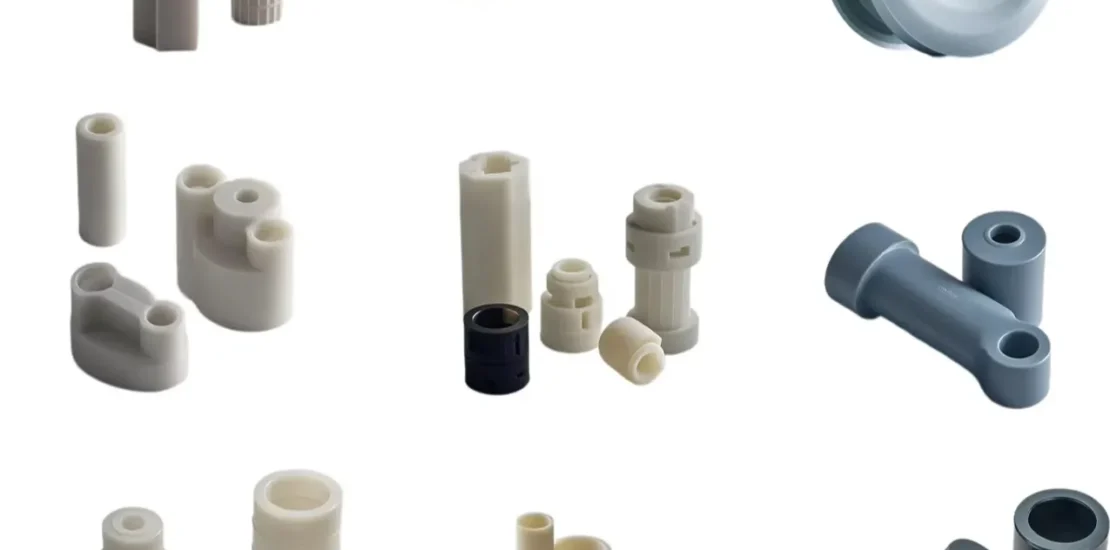
Plastic injection parts have quietly shaped the backbone of modern industry. From consumer electronics to automotive interiors and medical devices, they are the unsung heroes that keep the world running smoothly. Developed in the early 20th century as a cost-effective manufacturing technique, injection molding quickly rose to prominence for its ability to produce high volumes of parts with exceptional precision. Over time, the process evolved with the introduction of new materials, better mold designs, and more efficient machines.
Today, the world of plastic injection parts is undergoing a profound transformation. Fueled by demands for sustainability, customization, and high performance, manufacturers are adopting groundbreaking innovations that redefine what these parts can do. Whether it’s integrating smart features, achieving microscopic precision, or reducing environmental impact, the future is truly being molded—one part at a time.
Smart Materials Changing the Game for Plastic Injection Parts
One of the most exciting shifts in the industry is the rise of smart materials. These are not just new kinds of plastics—they’re engineered substances with enhanced functionality. Biodegradable resins, for example, allow manufacturers to reduce waste and meet environmental goals. Self-healing polymers can repair micro-cracks, extending the lifespan of components in demanding applications like automotive systems.
Conductive polymers and shape-memory plastics are also being incorporated into plastic injection parts, opening doors to parts that respond to heat, light, or electrical stimuli. These materials enable new possibilities in wearable tech, sensors, and medical devices. With continued research, smart materials are set to transform what plastic injection parts can achieve—from passive components to active, intelligent systems.
Micro Molding: Big Potential in Tiny Plastic Injection Parts
Miniaturization has become a driving force across multiple industries, especially in electronics and healthcare. Micro molding technology enables the production of plastic injection parts measured in microns, with features that are often invisible to the naked eye. These ultra-small parts are used in hearing aids, surgical instruments, microfluidic devices, and compact sensors.
To achieve this, manufacturers use precision tooling, advanced robotics, and high-resolution quality control methods. Micro molding pushes the boundaries of what’s possible, demanding perfection at an incredibly small scale. As devices continue to shrink, the importance of these tiny but complex parts will only grow.
Sustainable Production: Green Innovations in Plastic Injection Parts
Sustainability is no longer optional—it’s a central pillar of modern manufacturing. The production of plastic injection parts is adapting by embracing greener practices. Many companies are investing in electric injection molding machines that consume less energy and emit fewer pollutants than traditional hydraulic models.
Recycled plastic resins are also gaining popularity, especially for non-structural components where high-performance polymers are not required. Some manufacturers are even creating closed-loop systems, where scrap materials are reprocessed and reintroduced into the production cycle. By rethinking the way plastic injection parts are made, the industry is helping reduce the global carbon footprint.
3D Printing Meets Injection Molding: Hybrid Approaches in Plastic Injection Parts
3D printing is no longer just for prototyping—it’s now complementing injection molding in powerful ways. Hybrid approaches allow for the rapid creation of mold inserts and customized components, speeding up development cycles and enabling low-volume production with precision.
For plastic injection parts, this means greater design flexibility and shorter lead times. Companies can test new geometries quickly, tweak molds on the fly, and create parts with internal features or undercuts that were previously too complex or expensive to mold. The combination of additive and traditional manufacturing is proving to be a game-changer for innovation and agility.
Real-Time Monitoring and AI Integration in Plastic Injection Parts Manufacturing
The factory floor is getting smarter, thanks to real-time monitoring systems and artificial intelligence. In plastic injection parts manufacturing, sensors now collect data on pressure, temperature, cycle time, and material flow—every second of every production run.
This data is processed by AI algorithms to detect anomalies, predict equipment failures, and optimize performance. The result is fewer defects, less downtime, and more consistent quality. Smart manufacturing is also enabling traceability, which is especially critical for parts used in regulated industries like medical and aerospace. AI is not just improving how plastic injection parts are made—it’s ensuring they meet the highest standards every time.
Advanced Mold Design for Next-Generation Plastic Injection Parts
Behind every great injection-molded part is a precisely engineered mold. Recent advances in mold design are making it possible to produce more complex plastic injection parts with faster cycle times. Conformal cooling, where cooling channels follow the shape of the part, reduces warping and shortens production times.
Modular mold systems are also becoming popular, allowing for easy adjustments and faster changeovers. Innovations in mold materials, such as ceramic or composite coatings, help extend mold life and improve performance with high-temperature or abrasive plastics. These developments are pushing the capabilities of plastic injection parts further than ever before.
Lightweighting and High-Strength Solutions in Plastic Injection Parts
In industries like aerospace and automotive, reducing weight without sacrificing strength is a top priority. Plastic injection parts are stepping up to this challenge with new structural designs and composite formulations. Ribbing, honeycomb structures, and fiber reinforcements allow parts to maintain durability while trimming excess material.
These lightweight solutions not only improve fuel efficiency and performance but also lower material costs and shipping expenses. As engineers continue to innovate, plastic injection parts will play a larger role in building high-performance, weight-conscious products.
Looking Ahead: What the Future Holds for Plastic Injection Parts
The pace of innovation in plastic injection parts shows no sign of slowing. Technologies like digital twins—virtual models of the manufacturing process—are helping predict outcomes before production even begins. Nanotechnology is being explored to enhance material properties at the molecular level, offering new levels of precision and strength.
Smart factory systems, powered by IoT and cloud connectivity, are creating fully automated, self-optimizing production lines. These trends point to a future where plastic injection parts are not only cheaper and faster to produce but smarter and more sustainable than ever before.