- April 25, 2025
- Posted by: feinuojixie
- Category: Injection Molding News
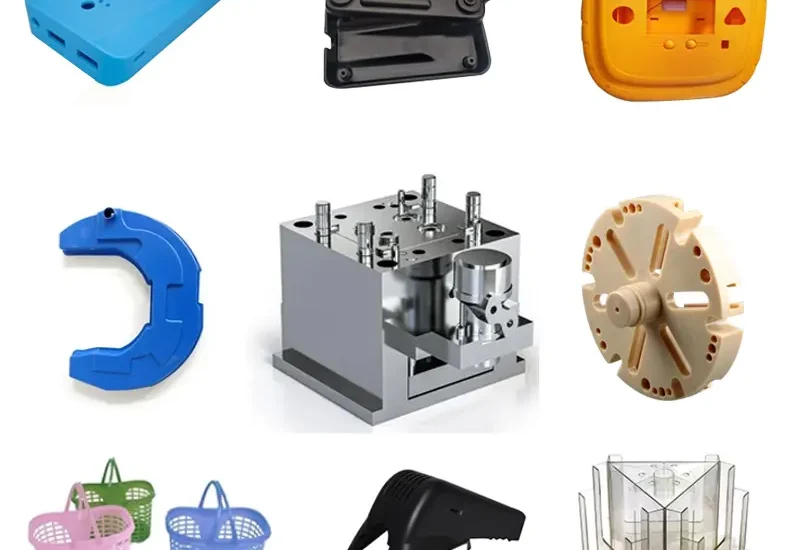
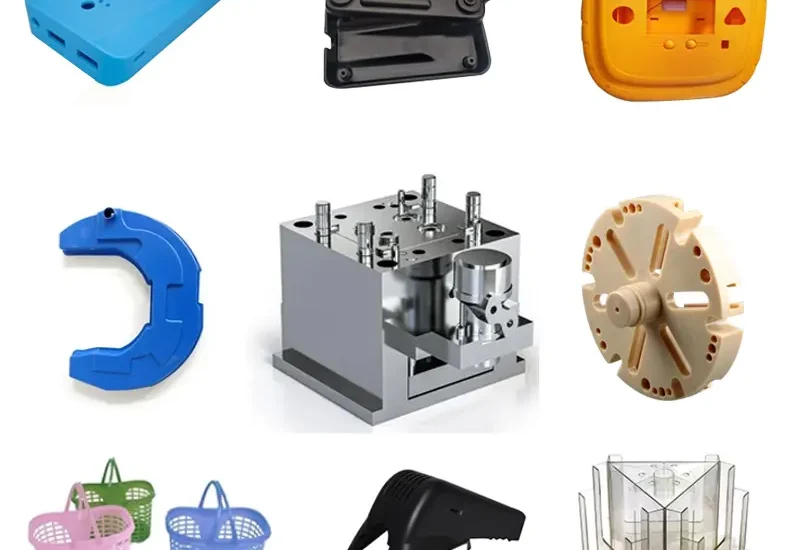
The manufacturing world is entering a transformative phase, and at the center of this evolution are injection parts. These components, once seen as simple outputs of a highly repetitive process, are now becoming smart, sustainable, and central to next-generation product design. As global industries—from automotive and aerospace to healthcare and electronics—continue to demand higher efficiency, quality, and customization, the injection part landscape is rapidly evolving to meet these expectations. Advancements in technology, materials, and design philosophy are driving the shift, unlocking new possibilities and redefining what injection part manufacturing can achieve.
Smart Materials Revolutionizing Injection Part Design
One of the most exciting shifts in the manufacturing of injection part lies in the development of smart and advanced materials. Traditional plastics are being replaced—or at least supplemented—by materials that offer superior performance and sustainability. Biodegradable polymers, for example, are now being used in applications where environmental responsibility is a priority. Carbon fiber-reinforced composites provide the strength of metal with a fraction of the weight, making them ideal for aerospace and automotive injection part. Meanwhile, thermally and electrically conductive plastics are opening new doors in electronics and energy sectors. These materials are not only enhancing product functionality but are also redefining design boundaries, offering greater freedom for innovation and application-specific tailoring.
Automation and AI in Injection Part Manufacturing
Automation is no longer a futuristic concept—it’s the backbone of modern injection part production. Robotics have become essential on the factory floor, executing complex molding and assembly tasks with speed and precision. Beyond the physical aspect, artificial intelligence is playing a growing role in data-driven decision-making. Machine learning algorithms are used to optimize cycle times, predict equipment maintenance needs, and reduce waste through advanced quality control systems. With AI, manufacturers can achieve greater consistency, minimize downtime, and scale production with unprecedented agility. This convergence of automation and intelligence is dramatically increasing the productivity and competitiveness of injection part operations.
Additive Manufacturing and Its Impact on Injection Part Prototyping
3D printing, or additive manufacturing, is reshaping how injection part are prototyped and tested. While it doesn’t replace traditional injection molding for mass production, it plays a critical role in accelerating product development cycles. Engineers can now quickly create functional prototypes, validate design concepts, and make rapid adjustments before investing in costly tooling. This not only speeds up innovation but also reduces overall development costs. In hybrid approaches, 3D printing can even complement injection molding by producing custom inserts or low-volume parts that are tailored to niche applications. The synergy between additive and traditional methods is becoming a hallmark of forward-thinking injection part strategies.
Sustainable Manufacturing Practices for Injection Part Production
Environmental concerns are reshaping the way injection part are made. Sustainability is no longer a marketing trend—it’s a manufacturing imperative. Innovations in energy-efficient molding machines, waste-reduction techniques, and recyclable materials are transforming production lines. Many manufacturers are now adopting closed-loop systems that recycle scrap directly back into the process, drastically reducing material waste. Moreover, sustainable resin alternatives, such as bio-based plastics, are becoming more widely adopted in both consumer and industrial applications. As governments impose stricter environmental regulations and consumers demand greener products, sustainable manufacturing is becoming a competitive advantage in the injection part sector.
Digital Twin Technology Enhancing Injection Part Precision
Digital twin technology is giving manufacturers a powerful new tool to optimize injection part design and performance. By creating a virtual replica of a physical object or process, engineers can simulate every aspect of production and product behavior under real-world conditions. This enables better testing, faster design iterations, and higher precision without the costs of physical trial and error. For injection part, this means identifying defects before they happen, optimizing mold geometry, and ensuring consistency across production runs. As digital twins become more integrated into manufacturing ecosystems, they will play a crucial role in pushing the boundaries of injection part innovation.
Global Supply Chain Innovation in Injection Part Delivery
Efficiency in the global supply chain is critical for injection part manufacturers. Modern innovations are transforming how materials and parts are sourced, tracked, and delivered. Just-in-time manufacturing models reduce storage needs and ensure timely delivery, while digital platforms allow for real-time inventory monitoring and forecasting. Some manufacturers are even adopting blockchain technology to enhance traceability and transparency across the supply chain. These innovations are not only reducing costs and lead times but are also improving risk management in an increasingly volatile global market. For injection part producers, a streamlined and responsive supply chain is essential to maintaining agility and customer satisfaction.
Industry 4.0 and the Smart Factory for Injection Parts
The smart factory is at the heart of Industry 4.0, and injection part manufacturers are among the early beneficiaries of this digital transformation. By integrating IoT devices, cloud computing, and big data analytics, factories are becoming highly connected and intelligent. Machines communicate in real time, operators receive instant feedback, and production lines adapt dynamically to changes in demand or operating conditions. These capabilities allow for greater customization, higher efficiency, and reduced downtime. For injection part production, the smart factory represents a leap forward in capability, enabling mass customization and predictive control with minimal manual intervention.
The Role of Customization in the Future of Injection Parts
Today’s consumers and industries alike are demanding more personalized solutions, and injection part manufacturing is evolving to meet this trend. Advanced molding techniques and digital tools are enabling highly customized parts at scale. Whether it’s tailoring components for medical devices, creating unique automotive interiors, or modifying electronics housings, customization is becoming a standard feature rather than a premium option. Design flexibility, rapid prototyping, and modular tooling are all contributing to this shift. As products become more individualized, injection part manufacturers who can adapt quickly will find themselves at the forefront of innovation.
Challenges and Opportunities in Future Injection Part Development
Despite all the progress, the journey toward the future of injection part is not without challenges. High initial investment in automation, the complexity of integrating AI, and the need for a highly skilled workforce can be significant hurdles. Furthermore, rapid technological evolution demands continual learning and adaptation. Yet, these challenges also open the door to tremendous opportunity. Companies that embrace change, invest in innovation, and develop resilient strategies will gain a competitive edge. With demand rising across sectors and technologies advancing at breakneck speed, the potential for growth in the injection part market is enormous.
The Road Ahead for Injection Parts Innovation
The future of injection part is dynamic, data-driven, and deeply intertwined with global shifts in technology and sustainability. From smart materials to AI-powered factories, the innovations shaping this industry are poised to redefine how we design, produce, and deliver essential components across every sector. While challenges remain, the direction is clear: manufacturers must innovate to stay relevant. Those who do will not only thrive in the modern era but will also lead the next wave of transformation in global manufacturing.