- March 31, 2025
- Posted by: feinuojixie
- Category: Injection Molding News
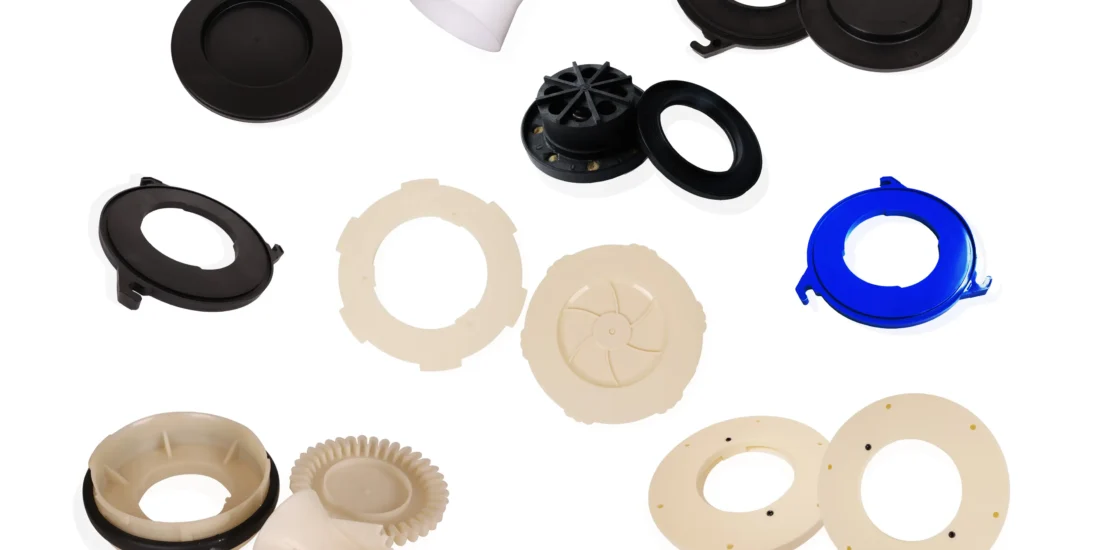
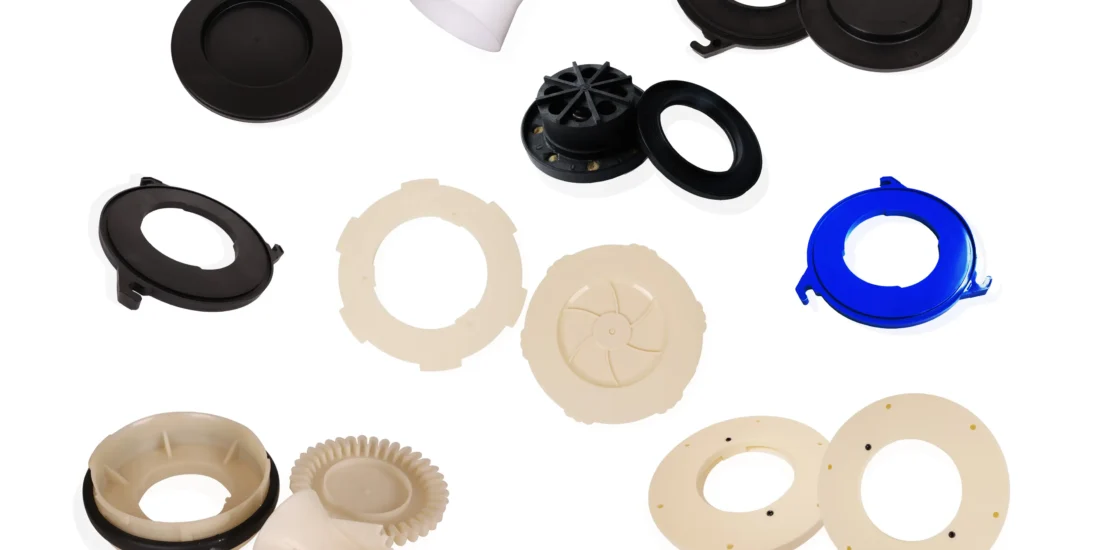
In the world of modern manufacturing, PC ABS injection moulding has become a cornerstone of innovative product design. This technique combines the strengths of polycarbonate (PC) and acrylonitrile butadiene styrene (ABS) to create high-performance plastic components. With its excellent mechanical properties, superior heat resistance, and impressive aesthetic finish, PC ABS injection moulding is widely used in industries such as automotive, electronics, and healthcare.
This article explores the power of PC ABS injection moulding in product design, highlighting its advantages, applications, and future trends. Whether you are an engineer, designer, or manufacturer, understanding the potential of PC ABS injection moulding can help you create durable and high-quality products that meet industry demands.
Understanding PC ABS Injection Moulding
PC ABS injection moulding is a manufacturing process that involves injecting a molten blend of polycarbonate (PC) and acrylonitrile butadiene styrene (ABS) into a mould to create complex and durable plastic parts. This hybrid material combines the high-impact resistance and heat stability of PC with the processability and toughness of ABS, making it a preferred choice for high-performance applications.
Unlike other plastic moulding methods, PC ABS injection moulding allows for greater design flexibility, precise detailing, and enhanced structural integrity. The process involves several stages, including material preparation, heating, injection, cooling, and ejection, ensuring that each part meets exact specifications. The ability to create intricate designs with consistent quality makes PC ABS injection moulding a superior option for product designers and manufacturers.
Advantages of PC ABS Injection Moulding in Product Design
One of the key reasons PC ABS injection moulding is widely used in product design is its exceptional benefits. These advantages make it an ideal material for creating products that require strength, durability, and aesthetic appeal.
-
High Impact Resistance and Durability
PC ABS is known for its toughness, making it suitable for applications that demand high impact resistance. This property ensures that products can withstand physical stress without cracking or breaking. -
Excellent Heat Resistance and Stability
Unlike standard ABS, PC ABS offers improved heat resistance, maintaining its structural integrity even in high-temperature environments. This is particularly useful for applications in electronics and automotive industries. -
Superior Surface Quality and Aesthetic Appeal
PC ABS injection moulding produces smooth, high-quality finishes that enhance the visual appeal of products. The material can be easily painted, plated, or textured to achieve a premium look. -
Enhanced Processability for Complex Designs
The flexibility of PC ABS allows for the creation of intricate designs with fine details. It supports thin walls and sharp edges without compromising strength, making it perfect for innovative product designs.
Applications of PC ABS Injection Moulding in Various Industries
PC ABS injection moulding is utilized across multiple industries due to its outstanding properties. Some of the most common applications include:
-
Automotive Industry
Many car components, such as dashboard panels, interior trims, and structural reinforcements, are made using PC ABS injection moulding. The material’s high impact resistance and heat tolerance make it ideal for vehicle interiors and exteriors. -
Consumer Electronics
PC ABS is widely used in the production of laptop casings, smartphone enclosures, and gaming accessories. Its durability ensures that electronic devices remain protected from drops and everyday wear and tear. -
Medical Devices
The medical industry benefits from PC ABS injection moulding for creating sterilizable and impact-resistant equipment. Components like diagnostic devices, housings for medical instruments, and protective enclosures are often made using PC ABS. -
Household Appliances
Kitchen appliances, vacuum cleaners, and other home gadgets frequently feature PC ABS parts due to the material’s lightweight nature, strength, and aesthetic appeal.
How PC ABS Injection Moulding Enhances Product Performance
PC ABS injection moulding plays a crucial role in improving product performance by ensuring durability, reliability, and resistance to environmental factors.
-
Improved Mechanical Properties for Long-Lasting Products
The combination of PC and ABS enhances mechanical strength, making products less prone to wear and tear. -
Resistance to Harsh Environmental Conditions
PC ABS can withstand UV exposure, humidity, and temperature fluctuations, making it suitable for outdoor and industrial applications. -
Better Adhesion for Secondary Operations
The surface properties of PC ABS allow for easy painting, plating, and adhesion to other materials, increasing the versatility of design options.
Design Considerations for PC ABS Injection Moulding
To maximize the benefits of PC ABS injection moulding, product designers must consider several key factors:
-
Choosing the Right PC ABS Formulation
Different grades of PC ABS offer varying levels of strength, flexibility, and heat resistance. Selecting the right formulation ensures optimal performance for specific applications. -
Optimizing Mould Design
Proper mould design reduces production defects such as warping, sink marks, and uneven cooling. Advanced moulding techniques can further improve efficiency and product consistency. -
Addressing Shrinkage and Warpage Issues
Since PC ABS has different shrinkage rates depending on its composition, designers must account for this in the moulding process to maintain dimensional accuracy.
Sustainability and Cost-Effectiveness of PC ABS Injection Moulding
With growing environmental concerns, manufacturers are increasingly turning to sustainable materials and processes. PC ABS injection moulding supports sustainability in several ways:
-
Recyclability
PC ABS can be recycled and reused, reducing plastic waste and promoting eco-friendly production practices. -
Cost Benefits for Mass Production
Injection moulding allows for the efficient production of high volumes of parts at a lower cost per unit, making it an economical choice for manufacturers. -
Reducing Material Waste
Advanced moulding techniques minimize excess material usage, ensuring a more resource-efficient production process.
Future Trends in PC ABS Injection Moulding
As technology advances, PC ABS injection moulding continues to evolve, offering even more possibilities for product design. Some emerging trends include:
-
Innovations in PC ABS Material Formulations
Researchers are developing new blends of PC ABS with enhanced properties such as increased flexibility, improved flame resistance, and greater environmental sustainability. -
Advanced Moulding Techniques
The integration of smart manufacturing and AI-driven moulding processes is leading to higher precision, faster production cycles, and reduced defects. -
Role in Next-Generation Products
From electric vehicle components to smart home devices, PC ABS injection moulding is playing a crucial role in shaping the future of consumer and industrial products.
Conclusion
PC ABS injection moulding is a powerful technique that enhances product design by offering superior strength, durability, and aesthetic appeal. Its widespread use in automotive, electronics, medical, and consumer industries highlights its versatility and reliability. By understanding the advantages and design considerations of PC ABS injection moulding, manufacturers can create high-quality, cost-effective, and sustainable products.
As innovation continues to push the boundaries of material science and manufacturing, PC ABS injection moulding will remain a key player in the evolution of modern product design. Whether you are designing everyday gadgets or advanced industrial components, PC ABS injection moulding provides the perfect balance of performance, efficiency, and aesthetics.