- April 9, 2025
- Posted by: feinuojixie
- Category: Injection Molding News
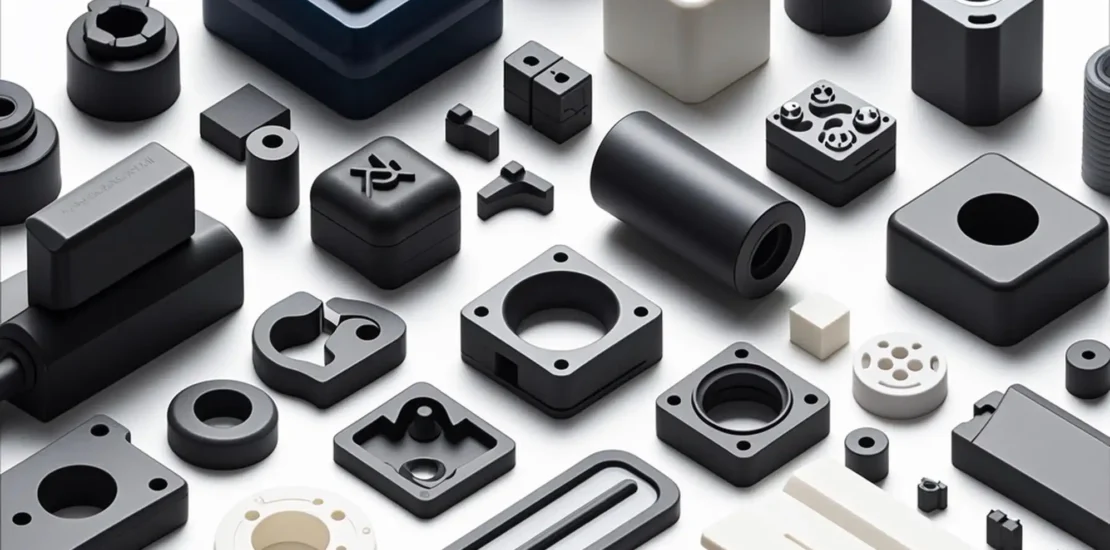
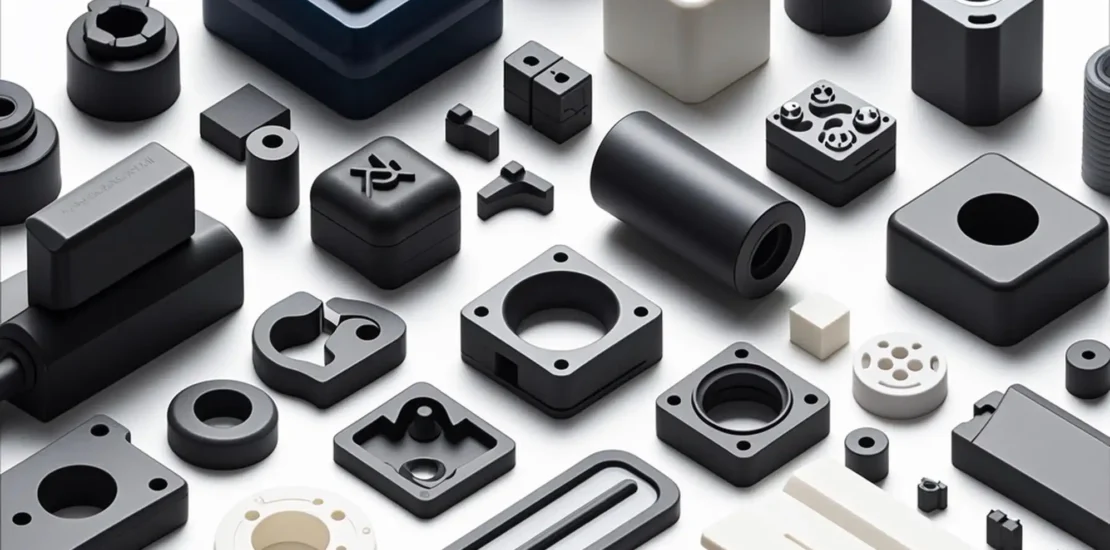
In today’s fast-paced automotive industry, the ability to design, test, and refine new concepts quickly is a competitive advantage. As vehicle technologies evolve—from electrification to autonomous driving—the pressure to innovate is higher than ever. Automotive prototyping has become the cornerstone of this innovation process, allowing designers and engineers to transform ideas into tangible models that can be tested and improved.
Among the various manufacturing techniques used in prototyping, injection molding automotive parts stands out as one of the most effective and reliable. This method allows manufacturers to create accurate, functional parts rapidly, using materials that closely mimic the properties of final production components. By incorporating injection molding into their prototyping strategy, automotive companies can significantly shorten development cycles, minimize costly design errors, and bring higher-quality products to market faster.
Whether it’s refining the aerodynamic contours of a bumper or testing the tactile feel of a dashboard panel, injection molding plays a pivotal role in making sure every detail is perfected before mass production begins. As we dive deeper into this article, we’ll explore how this process works, why it’s ideal for prototyping automotive parts, and what the future holds for this essential technology.
Understanding Automotive Prototyping and Its Challenges
Automotive prototyping is the process of developing and testing parts or systems before committing to full-scale production. It serves as a crucial phase where ideas are transformed into physical components for evaluation. However, this process is not without challenges. One of the biggest hurdles is time—automotive designs evolve rapidly, and any delays in testing can derail production timelines.
Additionally, ensuring material performance, design accuracy, and functional integrity during prototyping can be complex. Traditional fabrication methods may not always offer the precision or repeatability needed for modern vehicle designs. That’s where injection molding offers a powerful advantage.
What Is Injection Molding and Why It Matters in Automotive Prototyping
Injection molding is a manufacturing technique that involves injecting molten material—typically plastic—into a mold cavity, where it cools and solidifies into the desired shape. This process is particularly valuable for prototyping because it produces detailed, high-fidelity components that closely represent the final production part.
For the automotive sector, this means that engineers can test injection molding automotive parts under real-world conditions. Whether it’s stress testing under heat, checking tolerances for moving components, or evaluating how a part fits within a larger system, injection molding enables precise validation at an early stage.
Key Benefits of Using Injection Molding for Automotive Parts
There are several compelling reasons why injection molding is widely adopted for automotive prototyping. First, it provides unmatched dimensional accuracy, which is critical when parts need to integrate with complex assemblies. Second, the repeatability of the process ensures that each prototype is consistent, which is essential for testing performance over multiple iterations.
Another major advantage is speed. Once a mold is created, parts can be produced rapidly, enabling faster prototyping cycles. This allows automotive teams to iterate on designs quickly, identifying and correcting issues before they escalate into costly production problems. Moreover, the ability to choose from a wide range of materials gives designers flexibility to test various physical and aesthetic characteristics.
Types of Automotive Parts Commonly Created Through Injection Molding
Many components in the prototyping stage benefit from injection molding. Common examples include dashboard elements, center console components, door handles, and air vents. Functional parts such as brackets, clips, and connectors are also frequently produced using this method.
Lighting housings and instrument panels, which require precise alignment and clarity, are often molded to evaluate both fit and optical performance. These injection molding automotive parts help simulate the final product more realistically, improving both design accuracy and confidence before moving into production tooling.
Material Selection in Injection Molding for Automotive Prototyping
Choosing the right material is essential for successful prototyping. Engineers must consider factors such as heat resistance, strength, flexibility, and surface finish. Materials like ABS, polycarbonate, and polypropylene are commonly used for their durability and ease of molding.
For more demanding applications, high-performance polymers such as nylon or PEEK may be used to replicate the behavior of metal components. These material options allow for comprehensive testing, ensuring that injection molding automotive parts perform reliably under the same conditions they will face in real-world environments.
How Injection Molding Enhances Design Validation and Testing
A key advantage of injection molding in automotive prototyping is its ability to support thorough design validation. When prototypes accurately reflect the shape, strength, and finish of final components, they can be subjected to rigorous testing.
This includes mechanical testing for stress and fatigue, environmental testing for heat and humidity resistance, and ergonomic testing for user interaction. The ability to validate these elements early helps reduce the risk of failure during production and enhances product reliability.
The Role of Injection Molding in Iterative Prototyping
Automotive development is inherently iterative. Initial concepts often go through multiple refinements before reaching a final design. Injection molding supports this process by enabling rapid retooling and reproduction of parts.
When a prototype reveals issues—whether in fit, aesthetics, or functionality—adjustments can be made to the mold design and new parts can be quickly produced. This cycle of feedback and refinement ensures that the final product meets all requirements for performance, safety, and user satisfaction.
Cost Efficiency of Injection Molding in Automotive Prototyping
While the upfront cost of creating molds may seem high, the long-term savings of using injection molding for prototyping are substantial. Once a mold is developed, the per-unit cost of each prototype becomes very low, especially when multiple versions are needed for testing.
Additionally, injection molding reduces material waste, offers low defect rates, and shortens the time needed to evaluate each design iteration. These efficiencies contribute to lower overall development costs and faster time-to-market—two major advantages in a competitive automotive landscape.
Future Trends: Advancements in Injection Molding Automotive Technology
The future of injection molding automotive parts is being shaped by new technologies. For example, the integration of 3D printing for mold fabrication has drastically reduced lead times and tooling costs. Engineers can now create complex mold geometries faster and more affordably than ever before.
Additionally, micro-injection molding is enabling the production of extremely small, intricate parts used in sensors and electronic systems. The use of bio-based and recyclable polymers is also gaining traction, supporting the industry’s sustainability goals. As digital tools and smart manufacturing techniques continue to evolve, the role of injection molding in prototyping will only grow more vital.
Why Injection Molding Is Indispensable in Automotive Prototyping
Injection molding automotive parts is more than just a manufacturing method—it’s a strategic tool that enables innovation, speed, and precision in the prototyping process. Its ability to produce realistic, functional prototypes helps engineers identify issues early, test performance under realistic conditions, and iterate quickly and cost-effectively.
As automotive technologies continue to advance, from electric drivetrains to smart interiors, the demand for rapid and reliable prototyping will only increase. With its unique blend of flexibility, material versatility, and scalability, injection molding remains at the heart of bringing automotive concepts to life.