- March 25, 2025
- Posted by: feinuojixie
- Category: Injection Molding News
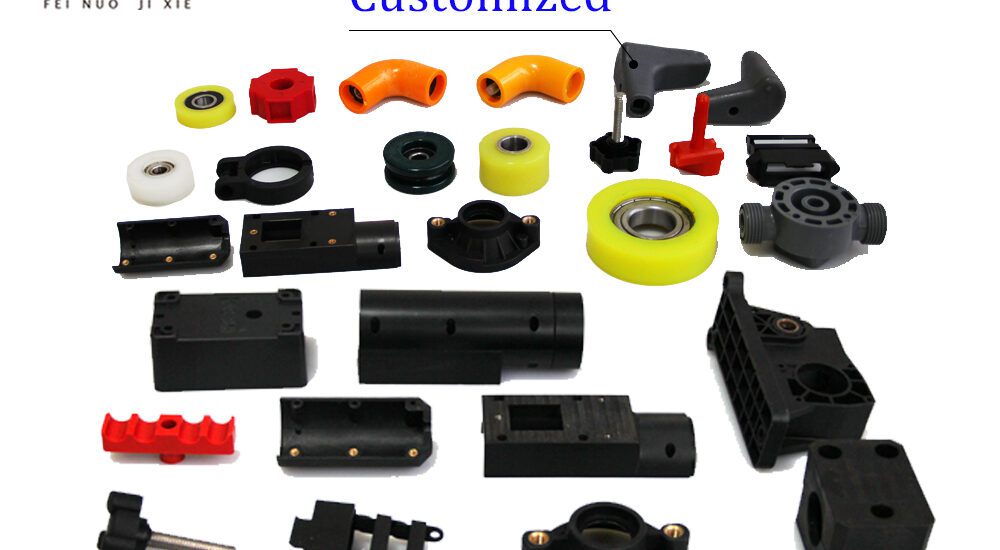
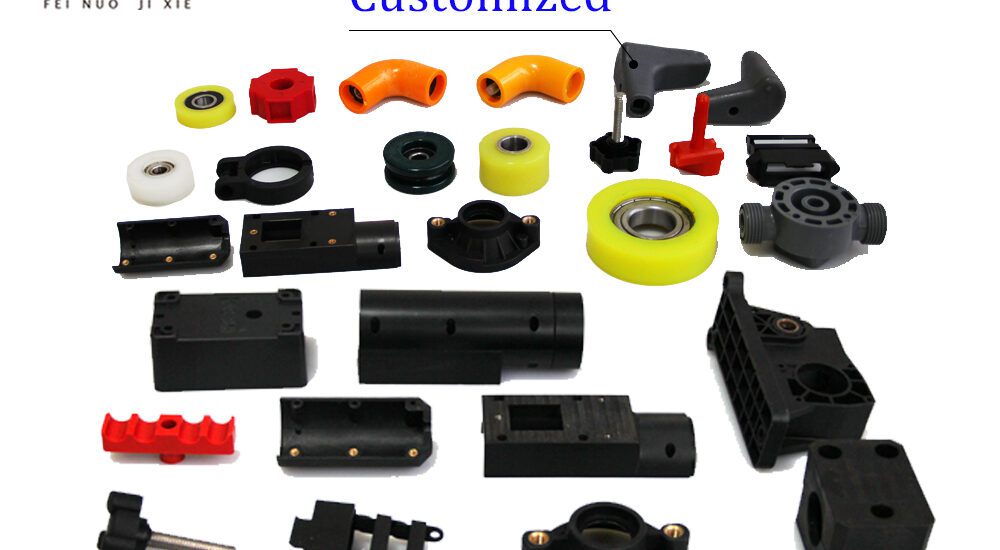
ABS injection moulding plays a crucial role in modern manufacturing, providing a reliable method for producing strong and versatile plastic parts. Acrylonitrile Butadiene Styrene (ABS) is a thermoplastic polymer known for its excellent mechanical properties, making it ideal for applications that require durability and impact resistance.
This moulding process involves injecting molten ABS material into a mould cavity, where it cools and solidifies into the desired shape. Industries such as automotive, consumer electronics, and construction heavily depend on ABS injection moulding for producing lightweight yet robust components.
In this article, we will explore the science behind ABS injection moulding, focusing on its strength, flexibility, and performance characteristics. We will also discuss its applications, challenges, and future trends, highlighting why it remains a key technology in modern manufacturing.
What Is ABS Injection Moulding?
ABS injection moulding is a manufacturing process that involves heating Acrylonitrile Butadiene Styrene (ABS) to a molten state and injecting it into a mould to create a specific shape. Once cooled, the material solidifies into a durable and precisely formed component. This method is widely used in various industries due to its efficiency, cost-effectiveness, and ability to produce complex shapes with high accuracy.
ABS is a unique thermoplastic polymer composed of three main monomers:
-
Acrylonitrile – Provides chemical resistance and heat stability.
-
Butadiene – Enhances toughness and impact resistance.
-
Styrene – Adds rigidity and glossy surface quality.
The combination of these elements results in a plastic that offers an excellent balance of strength, flexibility, and performance, making it one of the most popular materials for injection moulding.
The Strength of ABS Injection Moulding
One of the primary reasons ABS is widely used in injection moulding is its exceptional strength. The butadiene content within ABS enhances its toughness, allowing it to withstand significant impact without cracking or breaking. This makes it ideal for applications where durability is a key requirement.
Key Strength Benefits of ABS Injection Moulding:
-
Impact resistance – ABS can absorb shocks and resist sudden forces, making it perfect for automotive parts, helmets, and protective casings.
-
Dimensional stability – Once moulded, ABS maintains its shape under mechanical stress, ensuring long-term performance.
-
Wear resistance – Components made from ABS withstand regular use without excessive wear and tear.
Because of these properties, ABS injection moulding is widely used in industries that demand structural integrity and high-performance plastic components.
The Flexibility of ABS Injection Moulding
ABS injection moulding offers a unique balance between rigidity and flexibility. This adaptability makes ABS suitable for applications that require both strength and slight elasticity.
Factors That Influence the Flexibility of ABS Injection Moulding:
-
Material composition – Adjusting the ratio of acrylonitrile, butadiene, and styrene can modify the flexibility of the final product.
-
Moulding conditions – Temperature, pressure, and cooling time can impact the flexibility and overall properties of the moulded part.
-
Wall thickness – Thinner sections tend to be more flexible, while thicker parts retain greater rigidity.
This flexibility is particularly useful in applications like snap-fit connectors, consumer electronics, and automotive interior components, where parts need to be strong yet slightly pliable.
Performance Benefits of ABS Injection Moulding
ABS injection moulding provides numerous performance advantages that make it a preferred choice for manufacturers.
Key Performance Features:
-
Heat resistance – ABS maintains its structure even at moderately high temperatures, making it suitable for components exposed to heat.
-
Chemical resistance – ABS can withstand exposure to oils, acids, and other chemicals, enhancing its durability.
-
Precision and consistency – The injection moulding process ensures that every part produced has consistent dimensions, reducing defects and improving product quality.
-
Cost-effectiveness – ABS is relatively affordable compared to other engineering plastics, making it an economical choice for large-scale production.
Because of these properties, ABS injection moulding is used in sectors requiring reliable and long-lasting plastic components.
The Science Behind the Injection Moulding Process
The ABS injection moulding process involves multiple precise steps to ensure high-quality results.
Step-by-Step Breakdown:
-
Material Preparation – ABS pellets are loaded into the injection moulding machine.
-
Melting and Injection – The material is heated to a molten state and injected into the mould under high pressure.
-
Cooling and Solidification – The molten ABS cools and takes the shape of the mould.
-
Ejection – The solidified part is ejected from the mould.
-
Post-Processing – Finishing touches like trimming, polishing, or coating may be applied.
Temperature, pressure, and cooling rate all play critical roles in determining the final properties of the moulded ABS product.
Applications of ABS Injection Moulding
Thanks to its strength, flexibility, and performance, ABS injection moulding is used across numerous industries.
Common Applications:
-
Automotive Industry – Used for dashboards, bumpers, and protective covers.
-
Consumer Electronics – Found in laptop casings, remote controls, and mobile phone housings.
-
Medical Devices – Utilized for durable, sterilizable equipment.
-
Construction Materials – Used in pipe fittings, panels, and protective components.
Its widespread application highlights the versatility and reliability of ABS injection moulding.
Challenges and Limitations of ABS Injection Moulding
Despite its many advantages, ABS injection moulding has some limitations.
Key Challenges:
-
UV Sensitivity – ABS can degrade under prolonged exposure to sunlight unless treated with UV stabilizers.
-
Environmental Impact – ABS is not biodegradable, raising concerns about sustainability.
-
Limited High-Temperature Resistance – Although ABS can handle moderate heat, extreme temperatures can cause deformation.
Manufacturers are continually working on solutions, such as UV-resistant coatings and recycling initiatives, to improve ABS’s environmental footprint.
Future Trends in ABS Injection Moulding
The field of ABS injection moulding is evolving with technological advancements.
Emerging Trends:
-
Eco-Friendly ABS Alternatives – Researchers are developing biodegradable and recycled ABS materials.
-
Smart Moulding Technologies – AI-driven moulding processes optimize efficiency and reduce waste.
-
Hybrid Manufacturing – Combining ABS injection moulding with 3D printing expands design possibilities.
These innovations will continue to enhance the performance and sustainability of ABS injection moulding.
Conclusion: Why ABS Injection Moulding Remains Essential
ABS injection moulding remains one of the most reliable and versatile manufacturing processes in the plastic industry. Its exceptional combination of strength, flexibility, and performance makes it a preferred choice for applications ranging from automotive components to consumer electronics.
As technology advances, improvements in material formulation and processing techniques will further enhance the efficiency and sustainability of ABS injection moulding. Whether for high-performance industrial applications or everyday consumer products, ABS injection moulding continues to shape the future of modern manufacturing.