- April 29, 2025
- Posted by: feinuojixie
- Category: Injection Molding News
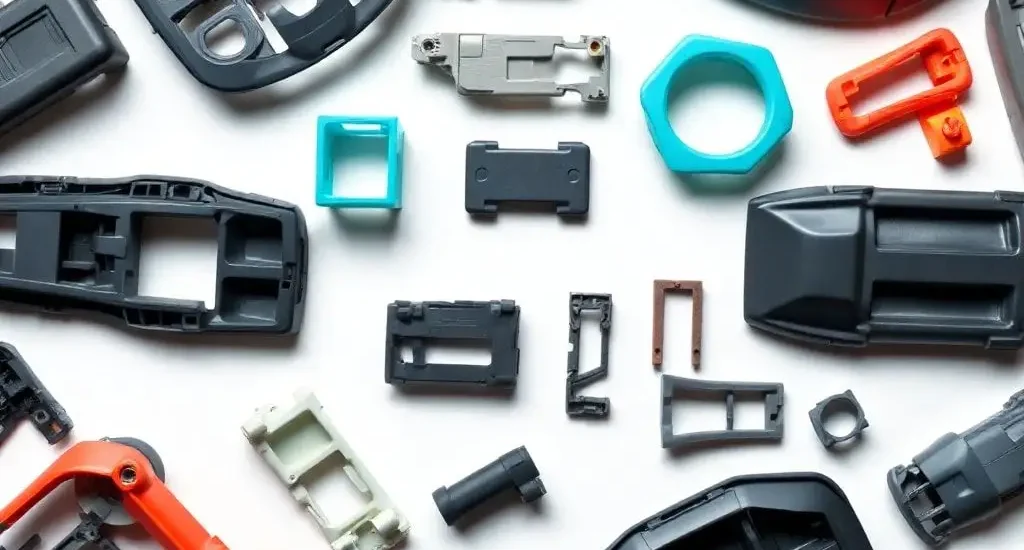
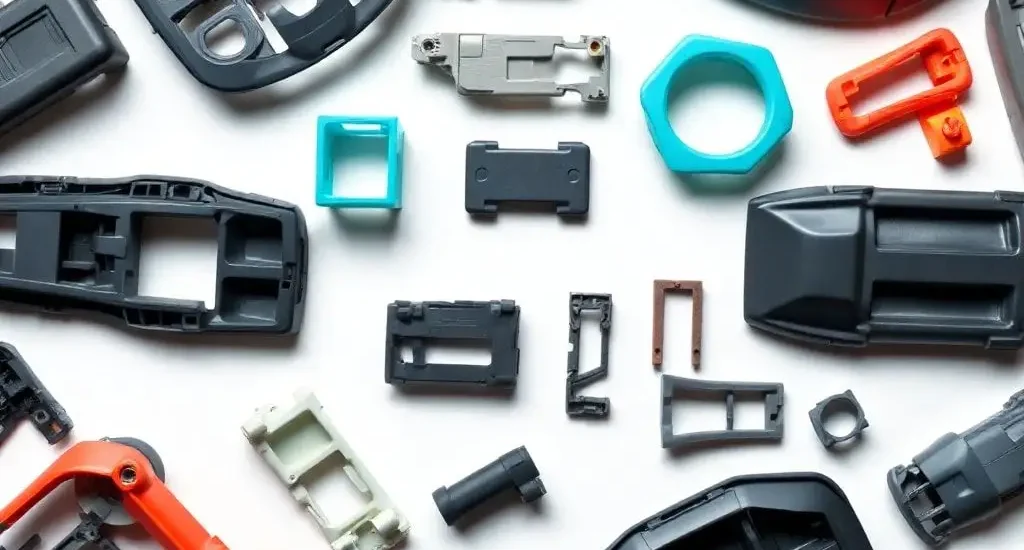
As the automotive industry accelerates toward lighter, more fuel-efficient, and sustainable vehicles, the demand for high-performance materials and advanced manufacturing techniques is higher than ever. Weight reduction has become a central strategy in achieving better fuel economy, improved handling, and lower emissions. However, reducing weight must not come at the expense of safety, durability, or cost efficiency. This is where injection molding automotive parts offers a powerful solution. By enabling the creation of strong yet lightweight components at scale, injection molding has revolutionized how vehicles are built and how they perform. This article explores the science and strategy behind this transformation, uncovering how injection molding contributes to the strength, efficiency, and innovation of modern automobiles.
Understanding Injection Molding in Automotive Manufacturing
Injection molding is a manufacturing process that involves injecting molten material into a precisely shaped mold cavity, where it cools and solidifies into the desired part. In the context of automotive manufacturing, this method is particularly valued for its ability to produce high-quality components with consistent dimensions and excellent surface finish. Unlike traditional metal fabrication or machining, injection molding minimizes material waste and allows for faster production cycles. The process is ideally suited for producing a wide range of automotive parts, from interior trims to structural components, offering manufacturers both design freedom and operational efficiency.
Why Injection Molding Is Ideal for Automotive Parts
One of the most significant advantages of injection molding automotive parts lies in its ability to balance strength and lightness. This balance is crucial for automotive engineers who must design vehicles that meet stringent safety regulations while keeping weight—and therefore fuel consumption—to a minimum. Injection molding allows the use of high-performance plastics that offer structural integrity comparable to metals but at a fraction of the weight. Moreover, the process enables rapid mass production of complex parts, reducing per-unit costs and speeding up time to market. It is a method well-suited for high-volume production without compromising on part quality or reliability.
Materials Used in Injection Molding for Automotive Parts
The effectiveness of injection molding in automotive applications is closely tied to the materials it employs. A wide range of thermoplastics and composites are used to meet the diverse requirements of different vehicle components. Polypropylene is popular for its low density and chemical resistance, making it ideal for interior panels and battery casings. Acrylonitrile butadiene styrene (ABS) is commonly used for its impact resistance and toughness. Nylon (polyamide) is favored for parts that need to withstand high mechanical stress and temperature, such as under-the-hood components. These materials can be further enhanced with additives like glass fibers to improve their mechanical properties, ensuring they meet the durability standards of modern vehicles.
Design Flexibility and Complexity with Injection Molding
Injection molding offers unmatched flexibility in part design. Engineers can create components with intricate geometries, undercuts, and integrated features like clips, ribs, and mounting points—all in a single molding cycle. This eliminates the need for secondary operations and fasteners, which not only reduces weight and cost but also enhances product reliability. Complex assemblies that once required multiple parts can now be manufactured as a single molded component. This design efficiency is particularly valuable in the automotive sector, where performance, aesthetics, and packaging constraints all demand innovative solutions.
The Role of Injection Molding in Reducing Vehicle Weight
Reducing the overall weight of a vehicle is one of the most effective ways to improve its fuel efficiency and lower emissions. Injection molding automotive parts contributes directly to this goal by replacing traditional metal components with lightweight plastic alternatives. For example, a molded intake manifold made from glass-reinforced nylon can weigh up to 60% less than its aluminum counterpart while maintaining comparable strength. These weight savings, when applied across multiple systems in the vehicle, result in significant performance gains without sacrificing durability or safety. Lighter vehicles also require less energy to accelerate and brake, which enhances driving dynamics and reduces wear on other vehicle systems.
Durability and Structural Integrity of Molded Automotive Parts
Despite being lightweight, molded automotive parts are built to withstand the rigorous conditions of daily driving. They must endure temperature fluctuations, mechanical stress, chemical exposure, and UV radiation—often simultaneously. Thanks to advancements in polymer science and engineering, modern plastics can be engineered to resist degradation and maintain their structural integrity over long lifespans. Components like engine covers, air ducts, and exterior trims are routinely subjected to harsh environments, yet they consistently perform thanks to the robustness of injection molded materials. Moreover, because the molding process creates parts with tight tolerances and minimal defects, it further enhances their reliability.
Applications of Injection Molding in Key Automotive Components
Injection molding is used in a wide array of automotive parts, both visible and hidden. In the vehicle interior, it is responsible for components such as dashboard panels, center consoles, door trims, and air vents. These parts benefit from the aesthetic versatility and tactile quality of molded plastics. Externally, bumpers, grille frames, and mirror housings are often molded for their lightweight strength and ability to absorb impacts. Under the hood, parts like engine covers, fluid reservoirs, fan shrouds, and air intake systems rely on injection molding for heat and chemical resistance. The process also supports the integration of electronic components, making it essential for modern infotainment systems and sensor housings.
Sustainability Benefits of Injection Molding in Automotive Parts
In an era where sustainability is a growing priority, injection molding offers clear environmental benefits. The process generates minimal waste, as excess material can often be recycled and reused. Many automotive suppliers are now using bio-based or recycled plastics in molded parts to reduce their carbon footprint. Additionally, the lightweight nature of molded parts contributes to more fuel-efficient vehicles, which in turn produce fewer emissions. By integrating sustainable practices into both materials and processes, injection molding helps automotive manufacturers align with global environmental targets while maintaining high performance standards.
Challenges and Innovations in Injection Molding for Automotive Parts
Despite its advantages, injection molding is not without challenges. High upfront tooling costs can be a barrier for low-volume production. Achieving uniform cooling and minimizing cycle times require precise mold design and process control. However, the industry is rapidly innovating to overcome these hurdles. Technologies such as microcellular injection molding are reducing material usage while maintaining part strength. Multi-material molding allows the combination of different polymers in a single part for enhanced functionality. Smart molding systems with real-time monitoring are also improving quality assurance and reducing downtime. These advancements are continuously expanding the capabilities of injection molding in automotive applications.
Injection Molding as the Backbone of Modern Automotive Engineering
Injection molding has become an indispensable tool in the creation of durable and lightweight automotive parts. By combining material science with advanced manufacturing techniques, it delivers solutions that meet the automotive industry’s toughest demands—strength, efficiency, design flexibility, and sustainability. From engine bays to passenger cabins, molded parts are transforming how vehicles are built and how they perform. As technology evolves, injection molding will continue to shape the future of automotive design, offering new possibilities for innovation and efficiency on the road ahead.