- April 8, 2025
- Posted by: feinuojixie
- Category: Injection Molding News
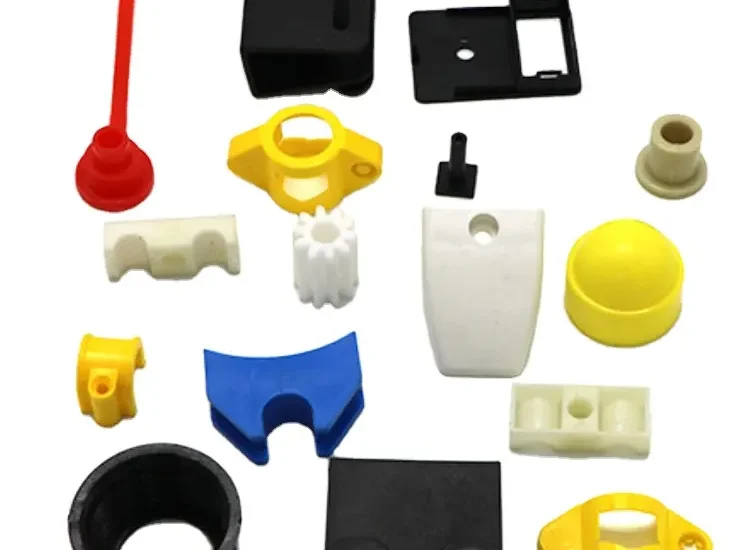
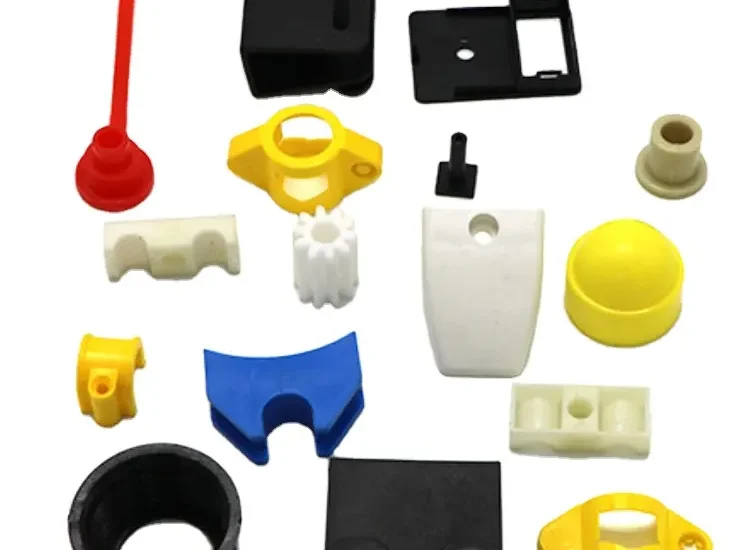
Injection molding part technology is the backbone of countless industries, from automotive to electronics to medical devices. As the demand for precision, speed, and affordability continues to grow, so does the need for innovation in how these parts are created. Modern manufacturing is in the midst of a quiet revolution, one driven by cutting-edge technologies that are transforming traditional methods into high-tech production lines. This evolution isn’t just about faster machines — it’s about smarter systems, sustainable materials, and processes that deliver consistent, high-quality parts with minimal waste. Understanding the technology behind injection molding part innovation is key to staying ahead in today’s competitive market.
The Basics of Injection Molding Part Production
At its core, injection molding is a manufacturing process used to produce parts by injecting molten material into a mold cavity. Once cooled and solidified, the part is ejected, and the process repeats. This technique is favored for its ability to create highly detailed, complex shapes with tight tolerances. Materials commonly used include thermoplastics like ABS, polypropylene, and polycarbonate. The injection molding part process relies heavily on precise temperature control, pressure regulation, and mold design. Choosing the right material and designing an efficient mold are crucial steps that influence product performance, production speed, and overall cost.
Advanced Materials Powering Better Injection Molding Part
Material science has played a transformative role in improving injection molding part quality. Traditional plastics are being replaced or enhanced with high-performance polymers that offer superior strength, heat resistance, and flexibility. Engineers are also exploring biodegradable materials like PLA and PHA, which support environmental goals without compromising functionality. Some modern resins include embedded additives such as glass fibers or UV stabilizers, which further extend the durability of molded parts. The development of customizable blends has also enabled more application-specific solutions, making injection molding part technology highly adaptable across industries.
Precision Engineering Through Smart Mold Design
Designing the mold is one of the most important phases in injection molding part manufacturing. Modern design software allows engineers to create incredibly complex geometries and simulate flow patterns before production begins. CAD (Computer-Aided Design) and CAM (Computer-Aided Manufacturing) tools help optimize mold structures, ensuring even material distribution and reducing the risk of defects like warping or sink marks. Mold flow analysis, for example, enables teams to visualize how molten plastic moves through the cavity, revealing potential weak spots. By integrating design for manufacturability principles, manufacturers ensure that each mold delivers not just accuracy, but also repeatability in high-volume production.
Automation and Robotics in Injection Molding Part Manufacturing
Automation has revolutionized the way injection molding part factories operate. Robotic arms are now standard in many facilities, handling repetitive tasks such as part removal, trimming, and quality inspection. This not only boosts efficiency but also reduces the likelihood of human error. Material handling systems automatically feed resins into machines, while conveyors and packaging robots handle finished parts. Collaborative robots, or cobots, are also being used to work safely alongside human operators. The result is a streamlined, highly productive environment where uptime is maximized and production costs are significantly lowered.
How AI and Machine Learning Optimize Injection Molding Part Quality
Artificial intelligence is making it possible to predict and prevent problems in real time. Machine learning algorithms analyze vast amounts of production data, identifying patterns that may indicate issues like short shots, flash, or temperature inconsistencies. These systems learn from historical runs and adjust machine settings dynamically, ensuring consistent quality. Predictive maintenance, powered by AI, can also alert operators to potential equipment failures before they happen. This technology minimizes downtime and reduces scrap rates, making injection molding part production not just smarter, but also more reliable.
Real-Time Monitoring and IoT Integration
The Internet of Things (IoT) is enabling real-time monitoring of every stage in the injection molding part process. Smart sensors embedded in machines measure key parameters like pressure, temperature, and cycle time. These metrics are instantly transmitted to centralized dashboards where operators can make immediate adjustments. Some systems even offer remote access, allowing engineers to monitor production from anywhere in the world. IoT-enabled machines can automatically calibrate themselves, record performance logs, and send alerts if any variable goes outside the optimal range. This level of transparency leads to tighter quality control and better decision-making.
3D Printing for Rapid Tooling in Injection Molding Part
Additive manufacturing is not just for prototypes anymore — it’s becoming a vital part of the injection molding part workflow. Rapid tooling, the process of creating molds using 3D printing, dramatically reduces lead times and cost. Engineers can quickly produce functional prototypes, test them in real-world conditions, and iterate on the design before committing to expensive steel tooling. This flexibility allows for faster time to market and greater innovation. While 3D-printed molds may not yet match the durability of traditional molds, they are ideal for short-run production and proof-of-concept testing.
Sustainable Innovations in Injection Molding Part Manufacturing
Sustainability is no longer optional — it’s a requirement. Injection molding part manufacturers are embracing green initiatives through various means. Energy-efficient hydraulic and all-electric machines consume less power and generate fewer emissions. Closed-loop water systems recycle coolant, while advanced filtration captures airborne particles. Some factories use solar energy to power equipment or opt for low-emission materials. Recycling programs for runners, sprues, and defective parts reduce waste significantly. These practices not only help the environment but also appeal to eco-conscious customers and improve long-term profitability.
The Future of Injection Molding Part Technology
The road ahead for injection molding part production is full of exciting possibilities. Smart molds embedded with sensors will provide even more granular data, enabling micro-adjustments in real time. Digital twins — virtual replicas of production systems — will allow manufacturers to simulate and optimize processes without interrupting live operations. Hybrid manufacturing methods, combining molding with overmolding or insert molding, will expand design potential. Meanwhile, advancements in sustainable polymers and carbon-neutral facilities will push the industry closer to full environmental responsibility. As technology continues to evolve, one thing is clear: injection molding part production will remain at the heart of modern manufacturing, continually pushing the boundaries of what’s possible.
Conclusion
The technology behind injection molding part innovation is more advanced — and more important — than ever. From smart mold design and AI-driven quality control to eco-friendly materials and IoT-enabled machines, every step of the process is undergoing transformation. These advancements are not only increasing efficiency and reducing costs but also shaping a future where precision, speed, and sustainability go hand in hand. For businesses and engineers alike, staying updated on these trends is the key to success in a rapidly evolving industry.