- April 3, 2025
- Posted by: feinuojixie
- Category: Injection Molding News
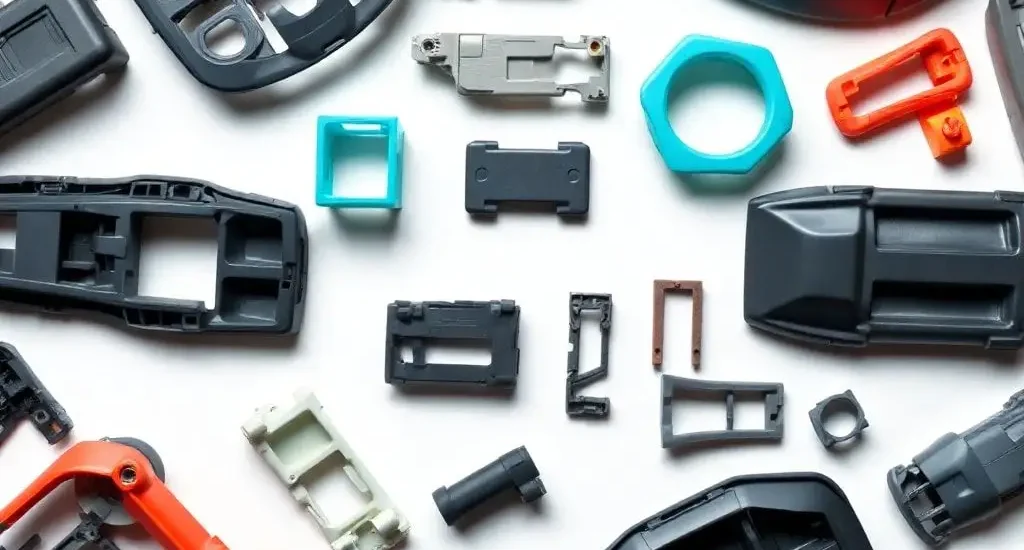
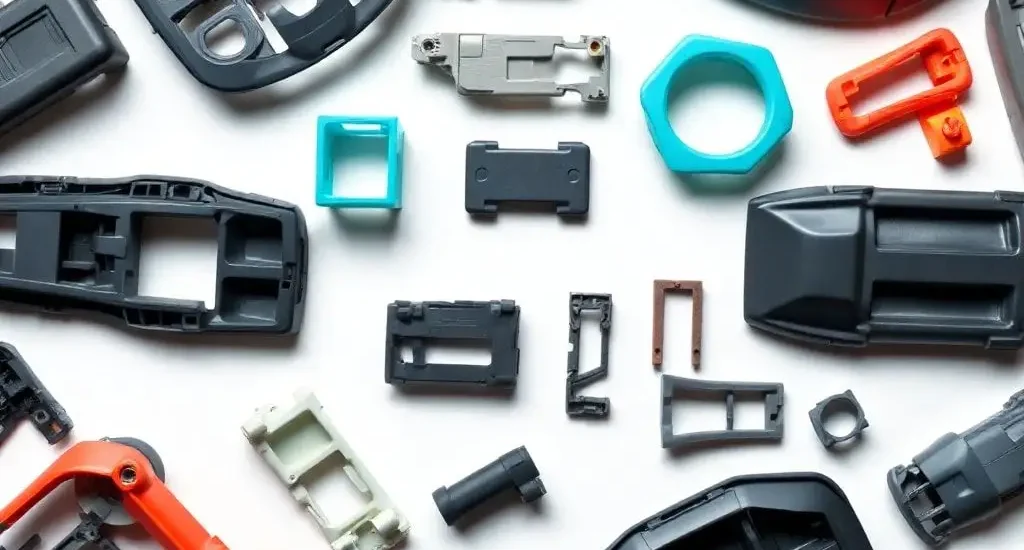
Injection molding is a widely used manufacturing process that plays a crucial role in producing plastic components for various industries, including automotive, medical, and consumer goods. The performance of an injection molding machine depends heavily on the quality of its components. Selecting the right injection machine part is essential for ensuring smooth operation, reducing production errors, and minimizing downtime.
Whether you are upgrading your machine, replacing worn-out components, or setting up a new injection molding system, understanding the key factors in choosing the right injection machine part can save you time and money. This guide will walk you through everything you need to know about different parts, their functions, and how to select the best ones for your specific needs.
Understanding Injection Machine Part and Its Importance
An injection machine part is any component that contributes to the operation of an injection molding machine. These machines are designed to melt plastic and inject it into a mold to create finished products. Each part plays a critical role in maintaining the machine’s efficiency and ensuring high-quality output.
What is an Injection Machine Part?
Injection molding machines consist of multiple components, including nozzles, barrels, screws, heating elements, and clamping units. Each part works together to facilitate smooth material flow, precise molding, and consistent production. A single faulty component can lead to defects in molded products, increased material waste, and costly downtime.
Why Quality Matters
The quality of an injection machine part determines how well the machine operates. High-quality parts provide:
-
Better performance: Smooth injection and precise molding reduce errors.
-
Longer lifespan: Durable materials prevent wear and tear, reducing replacement frequency.
-
Energy efficiency: Modern components help optimize energy consumption.
-
Reduced maintenance costs: Fewer breakdowns mean less frequent repairs and lower operational expenses.
Investing in the right parts can significantly improve the overall productivity of your injection molding machine.
Key Types of Injection Machine Part and Their Functions
Understanding the different components of an injection molding machine will help you make informed decisions when selecting replacement parts.
Nozzles
Nozzles control the flow of melted plastic from the machine into the mold. Choosing the right nozzle type ensures efficient material transfer and prevents issues like leakage or clogging. Some advanced nozzles come with temperature control to maintain optimal viscosity.
Barrels and Screws
The barrel houses the screw, which rotates to melt, mix, and push the plastic toward the mold. The design of the screw affects the melting process, injection pressure, and overall quality of the molded product. Choosing the correct barrel and screw is essential for achieving precise injection and reducing material waste.
Heating Elements
These components regulate the temperature of the plastic inside the barrel. A stable and consistent temperature ensures proper material flow, preventing defects in the final product. High-quality heating elements improve energy efficiency and extend the machine’s lifespan.
Clamping Units
The clamping unit holds the mold in place and applies pressure to ensure proper shaping of the plastic part. A well-functioning clamping system prevents defects such as warping, incomplete filling, and surface imperfections.
Hydraulic and Electric Systems
Injection molding machines can use either hydraulic or electric drive systems. Hydraulic systems provide high pressure and are suitable for large-scale production, while electric systems offer precision and energy efficiency. Selecting the right drive system depends on your production needs and cost considerations.
Factors to Consider When Selecting an Injection Machine Part
When choosing an injection machine part, consider the following factors to ensure compatibility and optimal performance.
Material Compatibility
Different plastics have unique melting points and flow characteristics. Ensure that components such as barrels, screws, and nozzles are designed for the type of plastic you are using.
Durability and Lifespan
Injection molding machines operate under high temperatures and pressures. Choosing durable materials such as hardened steel or ceramic-coated parts can prevent wear and tear, reducing the need for frequent replacements.
Precision and Tolerance
Injection molding requires extreme precision to produce high-quality parts. Select components with tight tolerances to ensure accurate and consistent production.
Maintenance Requirements
Some parts require regular cleaning or lubrication to function correctly. Choosing parts that are easy to maintain can save time and prevent production delays.
Energy Efficiency
Modern injection molding machines prioritize energy efficiency. Selecting components that reduce heat loss and optimize power usage can lower operational costs while maintaining productivity.
How to Identify High-Quality Injection Machine Part
Not all parts are created equal. To ensure you get high-quality components, consider the following:
Manufacturer Reputation
Buying from a reputable manufacturer ensures better quality and reliability. Established brands often provide warranties and customer support to assist with installation and troubleshooting.
Certifications and Compliance
Check for industry certifications such as ISO and CE compliance. These standards indicate that the parts meet strict quality and safety regulations.
Testing and Quality Assurance
Reliable manufacturers conduct thorough testing on their components before releasing them to the market. Look for parts that have been tested for performance, durability, and precision.
Common Mistakes to Avoid When Choosing an Injection Machine Part
Even experienced professionals can make mistakes when selecting replacement parts. Here are some common pitfalls to avoid:
-
Ignoring material compatibility: Using the wrong materials can lead to faster wear and production defects.
-
Choosing cheap parts: Low-cost components may seem appealing but can compromise machine performance and longevity.
-
Overlooking maintenance requirements: Some parts require frequent upkeep, and ignoring this can lead to unexpected breakdowns.
-
Not considering energy efficiency: Older, inefficient parts can increase operational costs over time.
Where to Buy the Best Injection Machine Part
Purchasing high-quality injection machine part from trusted sources ensures durability and optimal performance.
Trusted Manufacturers and Suppliers
Look for well-known manufacturers that specialize in injection molding components. They often provide better warranties, customer support, and high-quality materials.
Online vs. Offline Purchases
-
Online suppliers: Offer convenience and a wide selection, but be sure to check reviews and certifications before buying.
-
Offline suppliers: Allow you to inspect parts in person, ensuring compatibility and quality.
Custom vs. Standard Parts
-
Standard parts: Readily available and cost-effective for general applications.
-
Custom parts: Designed for specific machines and production needs, offering better performance but at a higher price.
Conclusion
Selecting the best injection machine part is essential for maintaining the efficiency, reliability, and productivity of your injection molding machine. By considering factors such as material compatibility, durability, precision, and energy efficiency, you can make informed purchasing decisions that enhance your manufacturing process.
Investing in high-quality components not only reduces maintenance costs but also ensures consistent production quality. Whether buying standard or custom parts, always choose trusted manufacturers and suppliers to get the best performance from your injection molding machine.