- April 7, 2025
- Posted by: feinuojixie
- Category: Injection Molding News
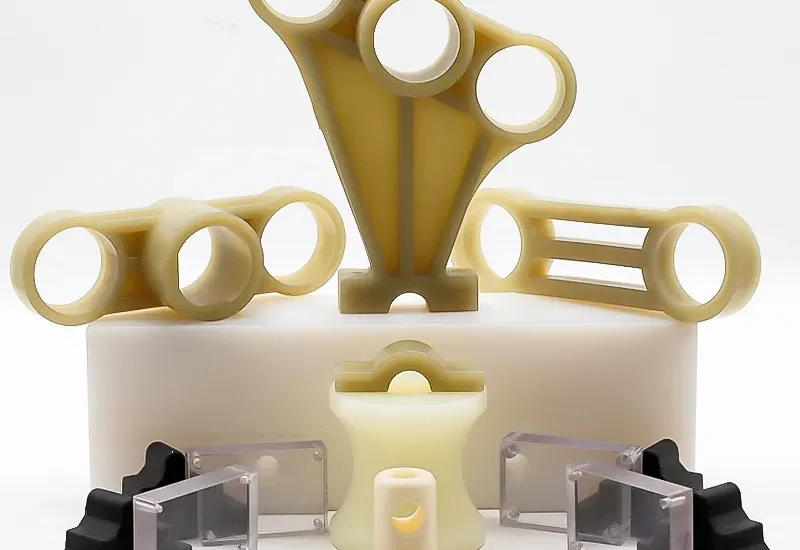
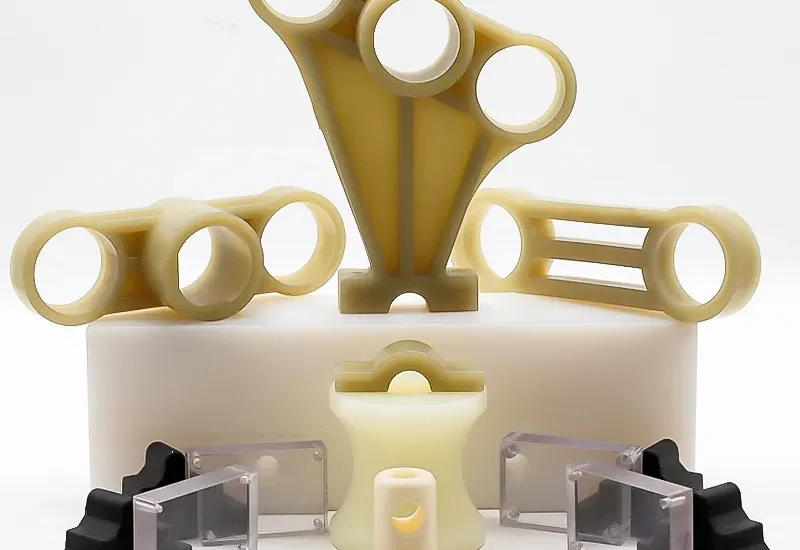
When it comes to product development, every detail matters—especially the components that bring your design to life. The plastic injection molding part is often one of the most vital elements in ensuring product performance, cost efficiency, and durability. Whether you’re designing a medical device, an automotive interior, or a consumer gadget, selecting the right molded component can mean the difference between long-term success and expensive setbacks.
A well-chosen plastic injection molding part not only meets functional and aesthetic requirements but also optimizes manufacturing efficiency. From reducing cycle times to preventing material waste, the right decision can significantly influence your bottom line. In this guide, we’ll walk you through the essential knowledge and considerations to help you choose the ideal part for your application—no matter the industry.
Key Factors to Consider When Selecting a Plastic Injection Molding Part
Choosing the right plastic injection molding part involves a careful balance between performance, cost, manufacturability, and application requirements. Start by identifying the function of the part—will it bear weight, interact with other components, or withstand harsh environments?
Other factors include required precision, mechanical strength, impact resistance, flexibility, and the desired appearance. Designers must also consider the estimated production volume, which can influence mold complexity and material selection. Taking a strategic approach ensures the plastic injection molding part is optimized for both design intent and production scale.
Material Matters: How to Choose the Right Resin for Your Plastic Injection Molding Part
Material selection is a crucial step that directly impacts the performance of a plastic injection molding part. Different thermoplastics offer unique advantages depending on their physical, chemical, and thermal properties.
For example, ABS is ideal for general-purpose parts due to its toughness and ease of molding. Polycarbonate is excellent for transparent parts that require high impact resistance. For more demanding environments, materials like PEEK or nylon offer superior heat and chemical resistance. Factors like UV stability, flame retardance, and food-grade compliance may also influence your choice. Consulting with a material expert or supplier can help ensure the resin selected aligns with the plastic injection molding part’s requirements.
Design Considerations for High-Performance Plastic Injection Molding Part
An effective plastic injection molding part begins with good design. Key features such as consistent wall thickness prevent sink marks and warping. Adding draft angles facilitates easy part ejection from the mold, reducing wear and tear.
Structural features like ribs, bosses, and gussets enhance strength without adding unnecessary weight or material cost. Designers should also avoid sharp corners and undercuts unless absolutely necessary, as these can complicate mold construction and increase tooling cost. By following design for manufacturability (DFM) guidelines, you can improve the reliability and cost-efficiency of your plastic injection molding part.
Tolerance and Precision: Meeting the Exact Specifications for Your Plastic Injection Molding Part
Precision is critical, especially in assemblies where a plastic injection molding part must align or connect with other components. Tolerance refers to the acceptable range of dimensional variation, and it is influenced by material shrinkage, mold design, and process control.
In high-performance or regulated industries like aerospace or medical devices, tight tolerances are a must. Engineers must work closely with mold makers to define achievable tolerances that won’t compromise part function or inflate costs. Proper measurement techniques and in-process inspections also ensure that each plastic injection molding part meets specification throughout production.
The Role of Tooling in Plastic Injection Molding Part Quality
Tooling is the foundation of every plastic injection molding part. A high-quality mold determines not only the shape of the final product but also its surface finish, dimensional accuracy, and cycle time.
Key tooling elements such as gate type, runner system, and cooling layout affect how the molten plastic flows and cools within the mold. Improper tool design can lead to defects like short shots, warping, or sink marks. Investing in precision tooling, even if costly upfront, results in a more consistent and high-performing plastic injection molding part over the long run.
Surface Finish and Aesthetic Requirements for Your Plastic Injection Molding Part
Aesthetic appeal is just as important as functionality, particularly for consumer-facing products. The surface finish of a plastic injection molding part can influence not only how it looks but also how it feels to the touch and performs in use.
Finishes range from high-gloss to matte to textured, and each option affects mold design and cost. Functional finishes, like anti-slip textures or EMI shielding coatings, can also be applied post-molding. Understanding the relationship between mold texture, part geometry, and material flow is vital to achieving the desired result.
Choosing the Right Supplier for Your Plastic Injection Molding Part
A skilled and reliable supplier can make all the difference when it comes to the success of your project. When evaluating manufacturers, look for expertise in your industry, robust quality control processes, and a track record of delivering complex plastic injection molding part on time.
Certifications such as ISO 9001 or IATF 16949 indicate a strong quality management system. Also consider whether the supplier offers in-house tooling, design support, or secondary services like assembly or packaging. The right partner will collaborate with you from concept to completion, ensuring your plastic injection molding part meets both technical and commercial expectations.
Cost Optimization Without Compromising Quality
Cost is always a factor, but cutting corners can be costly in the long run. To reduce expenses while maintaining quality, consider simplifying part geometry, using family molds, or switching to a more cost-effective resin that still meets the application needs.
Cycle time optimization, material utilization, and predictive maintenance on molds can also reduce long-term costs. Remember that a well-optimized plastic injection molding part doesn’t just save money—it improves reliability and enhances user satisfaction.
Common Mistakes to Avoid When Choosing a Plastic Injection Molding Part
Many design and sourcing errors can lead to expensive delays and product failures. Common mistakes include choosing a material without considering long-term durability, designing parts with inconsistent wall thickness, or failing to perform mold flow analysis.
Overcomplicating the part or underestimating the mold cost are also frequent missteps. Avoid these pitfalls by working with experienced engineers, leveraging simulation tools, and testing prototypes early. Being proactive helps you create a plastic injection molding part that performs as intended without surprises during production.
Future Trends in Plastic Injection Molding Part Design and Production
The world of plastic injection molding is evolving rapidly. Sustainable materials are becoming more common as companies look to reduce environmental impact. Bio-based resins and recyclable thermoplastics offer new options for eco-conscious production.
Technologies like micro-molding are enabling the creation of ultra-small components for electronics and medical devices. Smart mold monitoring systems are improving process control and reducing downtime. By staying ahead of these trends, manufacturers can create innovative and efficient plastic injection molding part that meet the demands of tomorrow’s market.
Getting the Perfect Plastic Injection Molding Part for Your Application
Selecting the right plastic injection molding part is not just about picking a shape—it’s about understanding materials, design principles, manufacturing constraints, and supplier capabilities. Every decision, from resin choice to surface finish, plays a role in the final outcome.
By applying the insights from this guide, you’ll be better equipped to make informed choices that enhance performance, reduce costs, and accelerate time to market. Whether you’re developing a prototype or scaling up for mass production, the perfect plastic injection molding part starts with smart planning and expert execution.