- May 2, 2025
- Posted by: feinuojixie
- Category: Injection Molding News
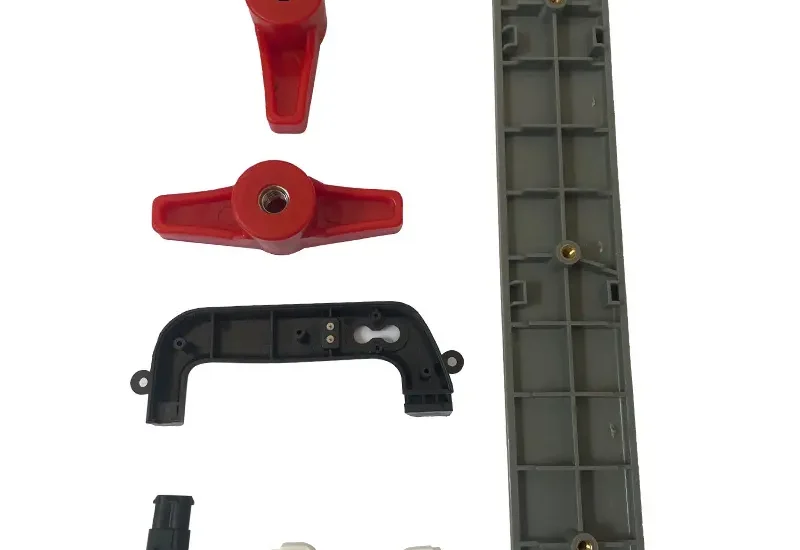
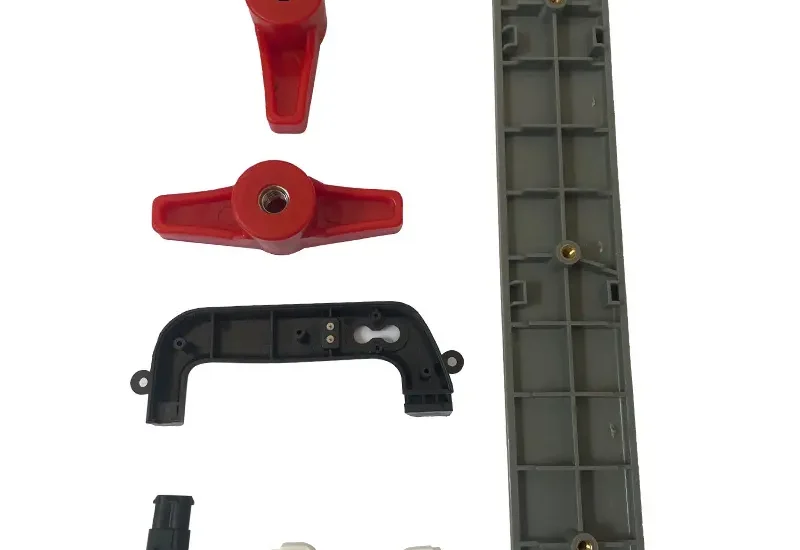
Plastic injection molding is one of the most widely used manufacturing processes for producing high-quality plastic parts. This versatile process allows for the creation of parts in a variety of shapes and sizes, catering to industries ranging from automotive to consumer electronics. Achieving high-quality results in plastic injection molding is essential for ensuring the functionality, durability, and cost-effectiveness of the end product.
In this guide, we will dive into the essential aspects of plastic injection molded part production. From understanding the molding process itself to troubleshooting common issues, this guide will cover everything you need to know about producing top-tier molded parts. Whether you’re new to the process or looking to refine your existing practices, you’ll find valuable insights to improve your operations and results.
What is Plastic Injection Molding?
Plastic injection molding is a manufacturing process that involves injecting molten plastic material into a mold cavity to form a specific part or product. The process begins with the selection of the material, which is then heated to a molten state. The molten plastic is injected under high pressure into a mold, where it cools and solidifies into the desired shape. The mold itself is made from high-strength materials, ensuring that it can withstand the pressure of repeated cycles without deformation.
The key components in the plastic injection molding process include the machine, mold, and material. The machine is responsible for heating and injecting the plastic, the mold defines the shape of the part, and the material dictates the properties of the final product. This process is widely used because it is highly efficient, precise, and capable of producing complex geometries at a low cost per part when scaled for mass production.
Factors That Affect the Quality of Plastic Injection Molded Part
Several factors can influence the final quality of a plastic injection molded part. These factors range from the materials used to the mold design and machine settings.
-
Material Selection: The choice of material plays a crucial role in determining the strength, flexibility, and durability of the part. Different plastics have different properties, and selecting the right one is essential for ensuring the final part meets the desired specifications. Factors such as temperature resistance, chemical resistance, and impact strength should be considered.
-
Mold Design: A well-designed mold is critical for achieving precision in plastic injection molding. Poor mold design can lead to defects such as sink marks, warping, or uneven surface finish. A well-crafted mold ensures uniform filling, accurate dimensions, and smooth surfaces.
-
Machine Settings: The machine settings, such as injection speed, temperature, and pressure, must be carefully controlled to achieve high-quality parts. If the settings are incorrect, it can lead to problems such as short shots (incomplete filling), flash (excess material), or even mold damage.
Common Types of Plastic Used for Injection Molding
Plastic injection molding uses a variety of materials, each with unique properties that make them suitable for specific applications. Some common materials include:
-
ABS (Acrylonitrile Butadiene Styrene): Known for its toughness, impact resistance, and ability to be easily processed. ABS is commonly used in consumer electronics, automotive parts, and appliances.
-
Polyethylene (PE): A lightweight and flexible material, polyethylene is often used for packaging, containers, and products requiring chemical resistance.
-
Polypropylene (PP): This material is known for its resistance to fatigue and chemical degradation. It’s commonly used for parts that must withstand repeated stress, such as automotive and medical components.
The right material selection depends on the intended use of the part and the environmental conditions it will face. Each material has specific strengths and weaknesses, so understanding these properties is key to selecting the right one for your application.
The Importance of Mold Design for High-Quality Injection Molding
Mold design is one of the most critical factors in achieving high-quality plastic injection molded parts. A mold that is poorly designed can lead to defects, such as uneven filling, excessive wear, and poor dimensional accuracy. The design should consider factors such as the flow of the material, cooling rates, and venting to avoid defects and ensure a smooth production process.
Advanced mold design technologies, such as computer-aided design (CAD) and simulation software, allow manufacturers to model and test molds before they are made, identifying potential issues early. This preemptive approach helps in producing more accurate molds, reducing lead time, and minimizing costly errors during production.
Key considerations when designing a mold include:
-
Material flow and pressure: Ensuring that the molten plastic flows evenly throughout the cavity.
-
Cooling channels: Proper cooling is essential to minimize cycle times and prevent defects.
-
Ejection mechanisms: Designing ejection systems that allow for smooth removal of the part without causing damage.
Troubleshooting Common Defects in Plastic Injection Molded Parts
Even with careful planning, defects can still occur in plastic injection molded parts. Some of the most common defects include:
-
Warping: This occurs when parts distort due to uneven cooling. Proper mold design and material choice can help reduce warping.
-
Flash: Flash is excess material that forms around the edges of a molded part. This usually happens when there is too much pressure in the mold or when the mold has small gaps. Proper mold maintenance and calibration can prevent flash.
-
Sink Marks: These depressions appear on the surface of parts when there is insufficient material in the mold or uneven cooling. This can be minimized by optimizing mold design and material flow.
-
Short Shots: This happens when the mold is not completely filled, often due to low pressure or improper machine settings. Ensuring proper injection speed and pressure can prevent this issue.
By understanding these defects and their causes, manufacturers can implement corrective actions such as adjusting machine settings, improving mold design, or selecting better materials.
Best Practices for Achieving High-Quality Plastic Injection Molded Parts
To consistently achieve high-quality plastic injection molded parts, manufacturers should follow best practices:
-
Proper Material Handling and Storage: Materials should be stored in controlled environments to avoid contamination and moisture absorption. Some materials, like nylon, are particularly sensitive to moisture, which can affect the final part’s properties.
-
Optimal Machine Maintenance: Regular maintenance of injection molding machines is crucial for ensuring they operate efficiently and without issues. Machine parts, including screws, barrels, and nozzles, should be cleaned and replaced as needed to avoid malfunction.
-
Quality Control and Testing: Continuous quality control is essential in ensuring that parts meet required specifications. Using techniques like automated inspection and testing for factors like dimensional accuracy, surface finish, and mechanical properties ensures that only high-quality parts leave the production line.
Applications of High-Quality Plastic Injection Molded Parts
Plastic injection molding is used in a variety of industries, producing parts that are integral to the functionality and success of products in these sectors:
-
Automotive Industry: High-quality plastic parts are essential for vehicle performance, from interior components to under-the-hood parts that require durability and heat resistance.
-
Electronics: Plastic injection molded parts in consumer electronics, such as casings and connectors, must meet high standards for precision, strength, and aesthetic quality.
-
Medical Devices: The medical industry demands injection molded parts that meet stringent regulatory standards for safety, reliability, and biocompatibility.
By ensuring high-quality standards, manufacturers can produce parts that perform well and contribute to the longevity of products in these critical industries.
Advancements in Plastic Injection Molding Technology
The field of plastic injection molding continues to evolve with technological advancements that enhance the accuracy, efficiency, and flexibility of the process. Some of the notable innovations include:
-
3D Printing for Rapid Prototyping: 3D printing is increasingly being used to create prototypes of molds, which can be tested and adjusted before full-scale production begins, saving time and costs.
-
Improved Materials: New composite materials and blends offer enhanced strength, flexibility, and resistance, opening up new possibilities for product applications.
-
Automation and Robotics: The integration of robotics into the injection molding process allows for faster cycle times, greater precision, and reduced labor costs.
Looking ahead, the future of plastic injection molding is poised to embrace more sustainable practices, including the use of recycled materials and energy-efficient processes.
Conclusion
Achieving high-quality plastic injection molded parts requires careful attention to detail throughout the entire production process. From selecting the right material and designing an effective mold to troubleshooting common defects and adhering to best practices, manufacturers must be diligent in their approach to ensure the final product meets the desired standards. As technology advances, the potential for further improvements in quality, efficiency, and sustainability in plastic injection molding continues to grow.