- April 14, 2025
- Posted by: feinuojixie
- Category: Injection Molding News
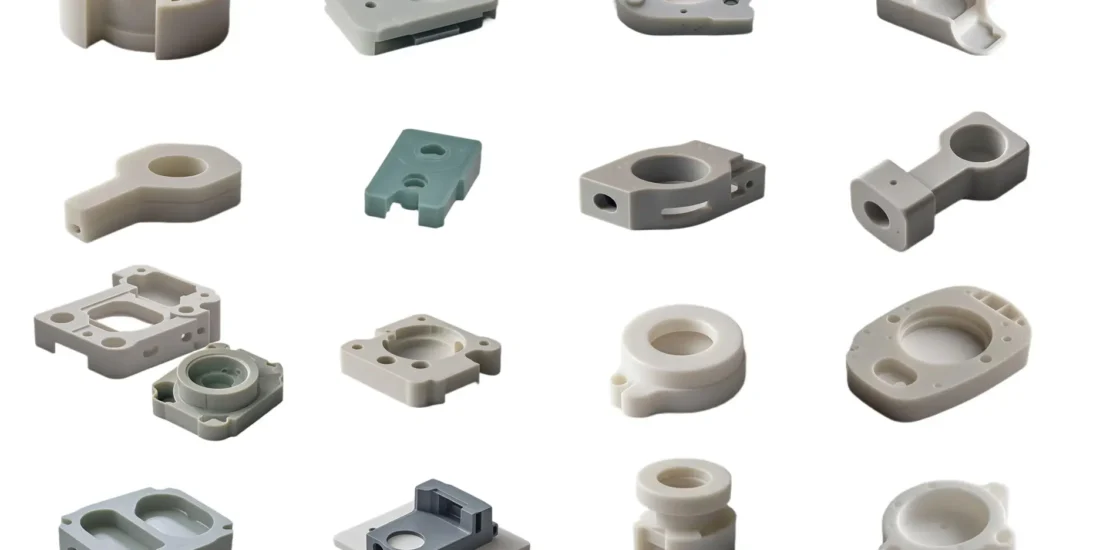
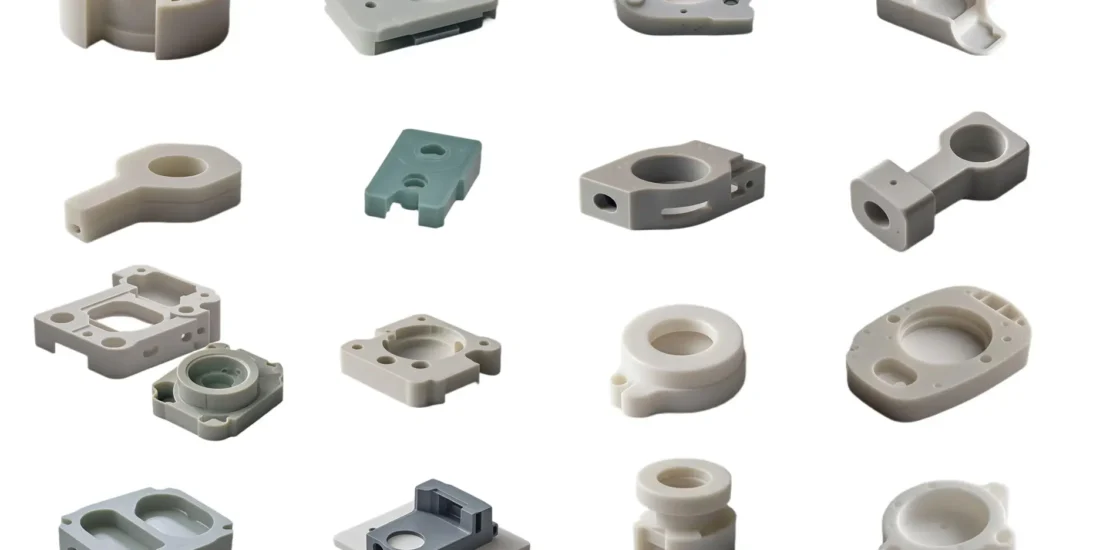
In the rapidly evolving world of automotive design and manufacturing, innovation is more than just a buzzword—it’s a necessity. As the demand for lighter, stronger, and more efficient vehicles increases, manufacturers are turning to smarter solutions to meet these expectations. Among these, plastic injection molding parts have emerged as silent game-changers, reshaping how cars are built and what they can do.
These components are found in nearly every corner of a modern vehicle, from intricate dashboard assemblies to structural support elements. Their rise in popularity is no coincidence. Plastic injection molding parts offer a unique blend of strength, flexibility, and cost-efficiency that traditional materials simply cannot match. More importantly, they empower designers to push boundaries, engineers to simplify production, and manufacturers to scale effectively.
In this blog, we’ll dive deep into the untold power of plastic injection molding parts in the automotive industry. We’ll explore the technology behind them, the strategic reasons for their widespread adoption, and the future trends poised to further revolutionize vehicle manufacturing. Buckle up—the road ahead is molded with innovation.
Why the Automotive Industry Depends on Plastic Injection Molding Parts
The automotive industry is under constant pressure to produce safer, more efficient, and aesthetically pleasing vehicles. To meet these demands, manufacturers rely heavily on plastic injection molding parts. These parts offer an ideal combination of properties—lightweight yet durable, cost-effective yet high-performing.
Plastic materials significantly reduce the overall weight of a vehicle, improving fuel economy and reducing emissions. At the same time, their strength and resistance to wear ensure reliability under the toughest conditions. From structural reinforcements to trim pieces, plastic injection molding parts have become indispensable for both performance and design innovation.
Their consistency and scalability also play a crucial role. The injection molding process allows manufacturers to create high volumes of identical parts with exact specifications, ensuring that every component fits perfectly into the assembly line.
From Concept to Car: The Plastic Injection Molding Process Explained
The journey of a plastic injection molding part begins long before it appears in a vehicle. It starts with the design and development of a precision mold, tailored to the exact specifications of the desired component. Engineers use advanced CAD software to prototype and simulate the part’s performance.
Once the mold is ready, plastic pellets are melted and injected under high pressure into the cavity. After cooling and solidifying, the part is ejected and inspected for quality. This entire process is highly automated and repeatable, ensuring minimal error and consistent results.
What makes plastic injection molding parts particularly attractive for the automotive sector is the speed of production and the ability to quickly adapt designs for new models. This agility is essential in an industry where timelines are tight and innovation is constant.
Critical Applications of Plastic Injection Molding Parts in Modern Vehicles
Plastic injection molding parts can be found in almost every section of a vehicle. In the interior, they form components like dashboards, glove compartments, air vents, and center consoles. These parts are not only functional but also contribute to the vehicle’s aesthetic and ergonomic appeal.
Under the hood, plastic injection molding parts are used for fluid reservoirs, engine covers, and housing for electronic control units. These parts must withstand heat, vibration, and harsh chemicals—conditions that modern plastics are engineered to endure.
Even exterior elements like bumpers, grilles, and mirror housings are created using injection molding techniques. These components benefit from plastic’s impact resistance and design versatility, offering both safety and style.
How Plastic Injection Molding Parts Drive Sustainability in Automotive Manufacturing
Sustainability is no longer optional in automotive production—it’s a global priority. Plastic injection molding parts support sustainability by enabling more efficient use of materials. Unlike traditional manufacturing methods that result in substantial waste, injection molding minimizes excess through precision design and closed-loop systems.
Many plastic parts are now made using recyclable or biodegradable materials. Some manufacturers also incorporate post-consumer or post-industrial plastics into their production, contributing to circular economy practices.
Moreover, lighter vehicles consume less fuel, which directly reduces CO₂ emissions. The integration of plastic injection molding parts is a key strategy in making vehicles more eco-friendly from the factory to the road.
Customization and Complexity: The Design Advantages of Plastic Injection Molding Parts
One of the biggest advantages of plastic injection molding parts is their unparalleled design flexibility. Engineers are free to experiment with complex geometries, thin walls, and integrated fastening systems—elements that would be impossible or cost-prohibitive using metal or other materials.
This freedom fosters innovation in aesthetics and functionality. For instance, a single molded part can include integrated clips, seals, or textures, eliminating the need for secondary assembly or additional fasteners. This not only speeds up production but also enhances part performance and reduces the chance of failure.
Customization is also faster and easier. Changing mold designs allows manufacturers to tailor parts for different car models or brands without the need for entirely new manufacturing setups.
Cost-Efficiency Without Compromise: Economic Benefits of Plastic Injection Molding Parts
Automakers operate in a fiercely competitive market where every dollar counts. Plastic injection molding parts offer a clear financial advantage. The high repeatability and low cycle times of injection molding drastically reduce labor and production costs, especially at scale.
Tooling costs are higher upfront, but the return on investment is substantial for long-term or high-volume production. The reduced weight of plastic parts also translates into savings on fuel and transport during logistics.
Additionally, fewer secondary processes are required thanks to the ability to mold complex shapes with fine detail and surface finishes. This results in fewer parts, less assembly, and faster time to market—all essential for profitability and competitiveness.
Future Trends: What’s Next for Plastic Injection Molding Parts in Automotive Design?
The future of plastic injection molding parts in the automotive industry looks more dynamic than ever. One major trend is the integration of smart materials and sensors directly into plastic components. This could lead to more intelligent, responsive vehicle systems without increasing weight or complexity.
Electric vehicles (EVs) are also pushing innovation in injection molding. New materials are being developed to manage heat and electromagnetic interference, both of which are critical in EV design. Injection molding also supports the rapid prototyping and production flexibility needed for fast-paced EV development.
Automation and AI are making mold design and quality control more efficient, reducing errors and improving consistency. As Industry 4.0 continues to evolve, plastic injection molding parts will remain at the heart of the transformation in automotive manufacturing.
Reinventing the Road with Plastic Injection Molding Parts
Plastic injection molding parts are not just a supporting act—they are central to the innovation driving the automotive industry forward. From reducing weight and emissions to enabling bold designs and efficient production, their impact is undeniable.
As cars become smarter, lighter, and more sustainable, the demand for versatile, high-quality components will only grow. Plastic injection molding parts are already meeting this demand and are poised to play an even bigger role in shaping the future of mobility. For manufacturers and consumers alike, the road ahead is clear—and it’s paved with precision-molded plastic.