- March 12, 2025
- Posted by: feinuojixie
- Category: Injection Molding News
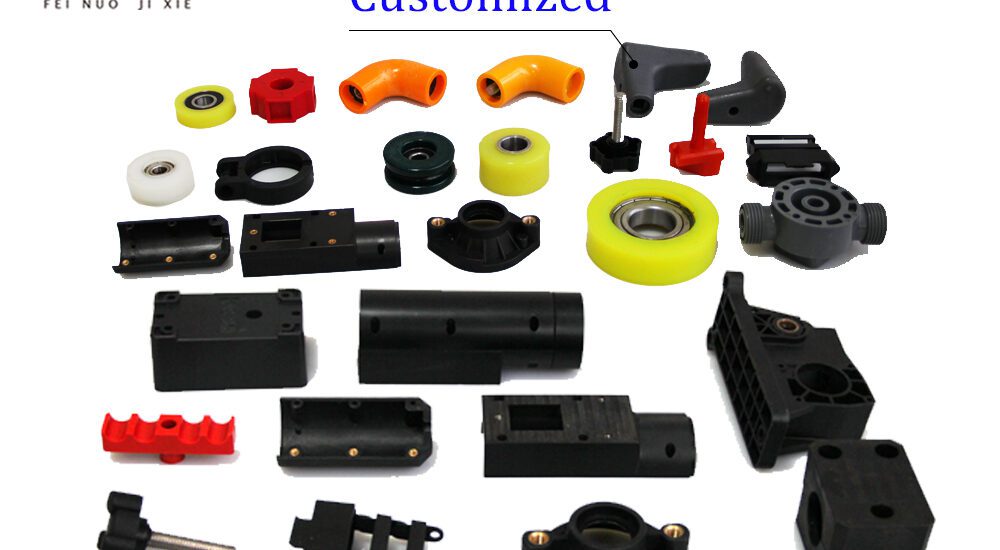
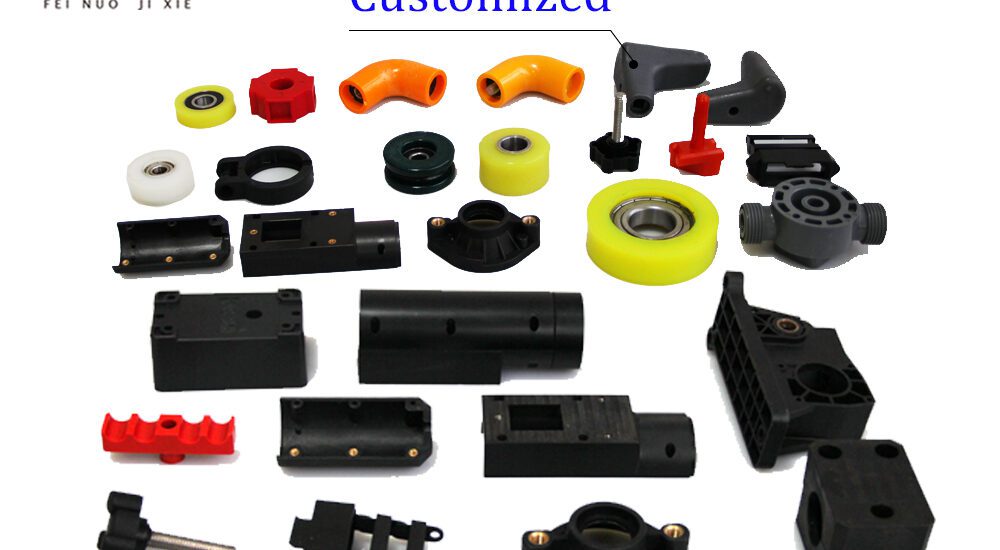
In modern manufacturing, ABS injection moulding has become an essential process due to its versatility, cost-effectiveness, and ability to produce high-quality components. ABS (Acrylonitrile Butadiene Styrene) is a widely used thermoplastic known for its durability, strength, and adaptability, making it a preferred material for various industries.
Manufacturers rely on ABS injection moulding to create durable and precise products that meet stringent quality standards. Whether used in automotive, electronics, or consumer goods, this process ensures efficiency and consistency. Below, we explore the top five benefits of using ABS injection moulding in modern manufacturing and why it continues to shape the industry.
Superior Durability and Strength
One of the primary advantages of ABS injection moulding is the outstanding durability of the final products. ABS is a thermoplastic with high impact resistance, making it ideal for applications that require long-lasting performance. The combination of acrylonitrile, butadiene, and styrene gives ABS its unique properties—acrylonitrile enhances chemical resistance, butadiene provides toughness, and styrene contributes to a smooth finish.
Manufacturers in industries such as automotive and electronics rely on ABS injection moulding to produce components that can withstand mechanical stress, temperature variations, and exposure to harsh environments. For example, automotive parts like dashboards, interior trims, and protective casings benefit from ABS’s resilience, ensuring longevity and safety in everyday use.
High Precision and Complex Design Capability
Another significant benefit of ABS injection moulding is its ability to create intricate shapes and complex geometries with high precision. This process allows for tight tolerances, ensuring that components fit perfectly and function as intended. Modern manufacturing often demands parts with detailed designs, and ABS injection moulding excels in meeting these requirements.
Industries such as medical devices, consumer electronics, and home appliances leverage this advantage to produce components with detailed patterns, thin walls, and intricate internal structures. For instance, laptop casings and smartphone covers require precise moulding to accommodate delicate internal components while maintaining a sleek design. With ABS injection moulding, manufacturers achieve the necessary accuracy while maintaining production efficiency.
Cost-Effective and Efficient Production
Manufacturing cost efficiency is a critical factor in choosing ABS injection moulding. This process significantly reduces material waste, optimizes production speed, and minimizes labor costs. Compared to traditional machining or other moulding techniques, injection moulding allows manufacturers to produce large quantities of ABS parts at a lower cost per unit.
The fast cooling and solidification properties of ABS further enhance production speed, allowing manufacturers to meet high-volume demands efficiently. Additionally, the automation of injection moulding reduces human error and ensures consistent product quality. For industries requiring mass production, such as the toy and packaging sectors, ABS injection moulding provides an ideal balance between affordability and performance.
Excellent Surface Finish and Customization Options
ABS is known for its excellent surface quality, making it a preferred choice for products that require a polished or textured finish. ABS injection moulding produces parts with a smooth surface that can be easily painted, coated, or plated, allowing for a wide range of customization options.
Manufacturers in the consumer electronics and automotive industries take advantage of these customization possibilities to enhance product aesthetics and branding. For example, gaming console housings and home appliance panels benefit from ABS’s ability to achieve glossy, matte, or textured finishes. Additionally, the material’s natural compatibility with adhesives and coatings allows for further design flexibility, ensuring that products not only perform well but also look visually appealing.
Environmental Benefits and Recyclability
Sustainability is becoming increasingly important in modern manufacturing, and ABS injection moulding supports eco-friendly production practices. ABS is a recyclable material, which means that waste from the injection moulding process can be reprocessed and reused, reducing overall material consumption.
Many industries are adopting ABS injection moulding as part of their sustainability efforts, ensuring minimal environmental impact while maintaining product quality. Recycling ABS reduces landfill waste and promotes a circular economy in manufacturing. Furthermore, the energy efficiency of the injection moulding process itself helps lower carbon emissions, making it a responsible choice for companies aiming to meet environmental standards.
Conclusion
ABS injection moulding has transformed modern manufacturing by offering a combination of durability, precision, cost-effectiveness, aesthetic appeal, and environmental benefits. From automotive components to consumer electronics, this process ensures high-quality production while optimizing efficiency and sustainability.
As technology continues to advance, innovations in ABS injection moulding will further enhance its capabilities, making it an indispensable tool for manufacturers worldwide. Whether for large-scale production or custom-designed products, ABS remains a reliable and versatile material that meets the demands of modern industries.