- April 9, 2025
- Posted by: feinuojixie
- Category: Injection Molding News
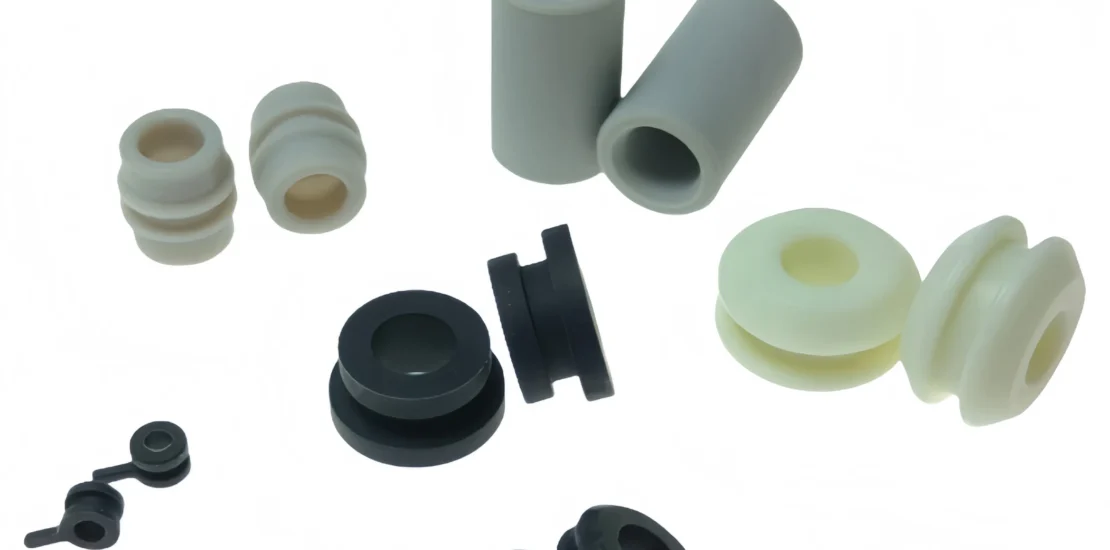
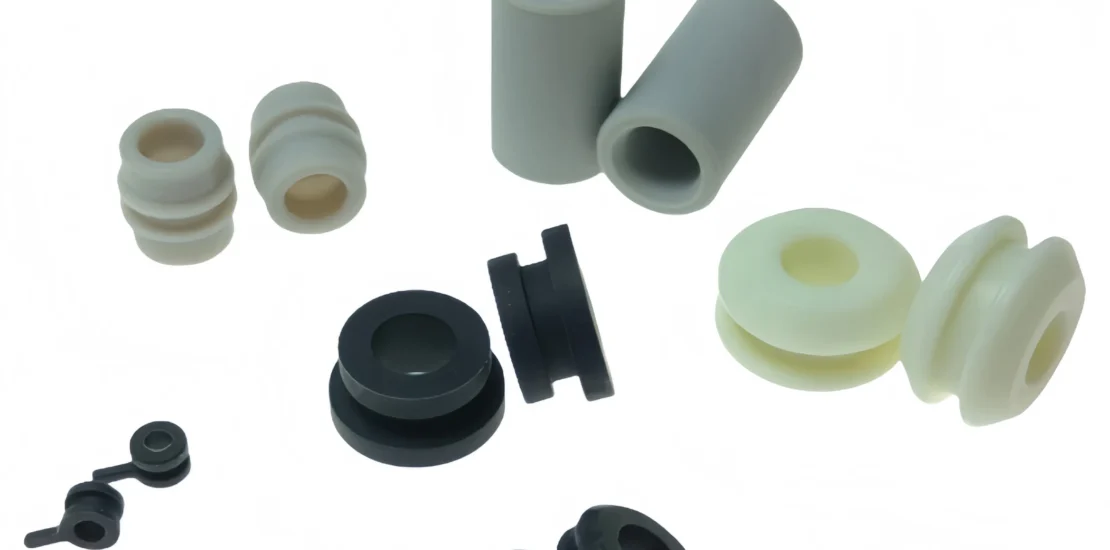
Plastic injection molding is one of the most versatile and efficient manufacturing techniques used across industries today. From creating lightweight components to shaping intricate designs with high repeatability, it plays a vital role in modern production. At the heart of many daily-use products—especially within the realm of injection molding automotive parts—this process combines speed, precision, and cost-efficiency like no other.
What makes injection molding stand out is its adaptability. Whether it’s a medical device, an automotive part, or a smartphone casing, this technique allows manufacturers to deliver high-performance components at scale. It’s a quiet force powering some of the most advanced industries in the world, often without users even realizing it. As we dive into the top sectors that rely on this technology daily, the critical role of injection molding in shaping our world becomes more evident than ever.
Automotive Industry: The Driving Force Behind Injection Molding Automotive Parts
The automotive sector is one of the most reliant industries when it comes to plastic injection molding. From the dashboard to the engine bay, countless vehicle components are created using this precise technique. Injection molding automotive parts include trim panels, air vents, cup holders, fenders, and even under-the-hood housings.
What makes this method so appealing to automakers is its ability to produce lightweight parts without sacrificing strength or durability. With global emphasis on fuel efficiency and electric mobility, reducing weight is more critical than ever. Injection molding also supports advanced design freedom, allowing engineers to create parts that are both functional and visually appealing. Furthermore, its scalability means millions of identical parts can be produced with minimal variation—critical in the high-volume world of vehicle manufacturing.
Medical Industry: Precision and Sterility at Scale
The medical field demands extreme precision, biocompatibility, and cleanliness—and plastic injection molding delivers on all fronts. From disposable syringes and IV components to surgical trays and housings for diagnostic devices, the process is essential in delivering sterile, high-quality products.
Injection molding excels in creating complex medical parts with tight tolerances. Since many of these components are single-use, the ability to manufacture them quickly and affordably is vital. Materials like medical-grade polypropylene and polyethylene can be molded into shapes that meet strict regulatory standards. Moreover, injection molding helps reduce contamination risks by allowing for automation and closed-system production environments.
For an industry where safety is paramount, this technology is a trusted solution that enables healthcare innovation at scale.
Consumer Electronics: Compact Design, Maximum Efficiency
Modern consumer electronics demand compact design, sleek aesthetics, and durable construction—and plastic injection molding makes all of that possible. From smartphone casings to laptop keyboards and internal components, this method is widely used to meet both performance and design expectations.
Injection molding allows engineers to develop thin-walled, high-strength parts that can withstand everyday wear and tear. The flexibility in design supports integration of clips, ribs, and complex geometries, reducing the number of separate parts needed. This not only simplifies assembly but also enhances product reliability.
In a world where electronic devices are getting smaller and smarter, the ability to manufacture compact and efficient parts through injection molding is more important than ever. It helps brands meet consumer demand for innovation, portability, and style.
Packaging Industry: Durable, Lightweight, and Eco-Friendly Solutions
In the packaging industry, where high volume and environmental considerations are key, injection molding has become a cornerstone manufacturing process. It’s used to create containers, bottle caps, lids, and closures that are not only durable but also reusable and recyclable.
Plastic packaging parts made with injection molding are typically lightweight, yet strong enough to withstand handling and transportation. This reduces shipping costs and lowers environmental impact. Brands are also leveraging biodegradable and recycled materials in molding to create more sustainable solutions.
Another key advantage is design customization. Companies can easily adjust shapes, textures, and branding elements to enhance shelf appeal and product identity. Whether it’s food packaging or cosmetic containers, injection molding supports fast production and consistent quality, making it indispensable to this industry.
Home Appliance Industry: Functionality Meets Form
From washing machines to blenders, plastic injection molding is heavily used in producing parts for home appliances. These include control knobs, outer casings, internal brackets, and even electrical insulators. The ability to combine function with design makes injection molding the go-to choice for appliance manufacturers.
With consumer expectations leaning toward energy-efficient, durable, and stylish appliances, the demand for high-quality molded parts has surged. The process allows for heat-resistant and impact-resistant materials that hold up under daily use. It also enables seamless integration of mechanical and electrical components, which is crucial for modern smart appliances.
Injection molding automotive parts may grab the spotlight, but in the home appliance industry, it’s the unsung hero ensuring performance, safety, and style go hand in hand.
Conclusion: The Ubiquity and Future of Injection Molding Automotive Parts
From the roads we travel to the devices in our hands, injection molding plays a vital role in shaping the products we rely on every day. While injection molding automotive parts represent a major sector, the technology’s influence extends far beyond the highway. In healthcare, electronics, packaging, and appliances, it delivers unmatched efficiency, accuracy, and adaptability.
As industries continue to evolve and innovate, the demand for precise, cost-effective manufacturing will only grow. Plastic injection molding stands ready to meet these needs—supporting a future where quality, speed, and creativity converge to deliver better products to the world.