- March 7, 2025
- Posted by: feinuojixie
- Category: Injection Molding News
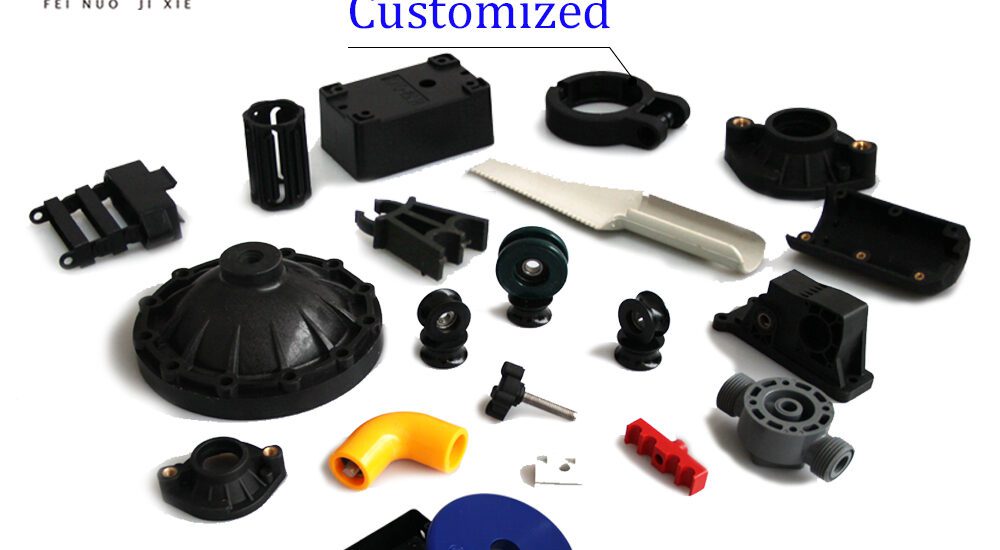
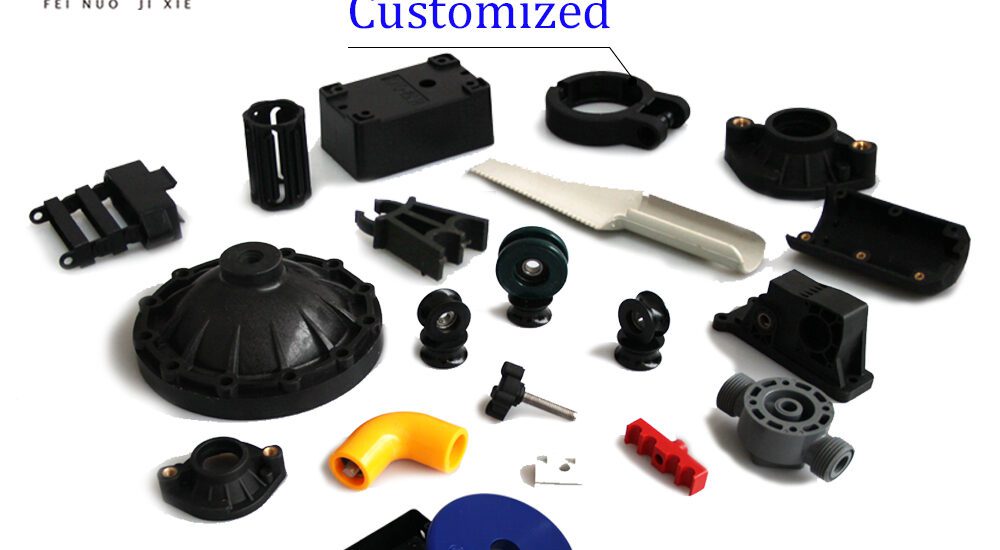
Injection moulding has long been a cornerstone of manufacturing high-quality plastic parts, and its importance continues to grow as industries demand more precision, efficiency, and sustainability. In 2025, injection moulding technology is expected to evolve significantly, driven by advancements in materials, automation, and smart manufacturing systems. As manufacturers face increasing pressure to deliver products faster and with greater reliability, these trends are expected to play a crucial role in meeting consumer and business expectations.
The injection moulding process has transformed over the years, with innovations allowing for more complex designs and enhanced part performance. This article explores the top trends that are poised to reshape injection moulding for plastic parts in 2025, offering insights into the future of the industry and how businesses can leverage these advancements to stay competitive.
Advanced Materials for Injection Moulding Plastic Parts
The use of advanced materials in injection moulding is one of the most significant trends for 2025. Traditionally, plastic parts were limited to a narrow range of materials. However, the development of high-performance resins, bio-based plastics, and composites has opened up new possibilities for stronger, more durable plastic parts. These materials offer a range of benefits, including enhanced strength, heat resistance, and lightweight properties, which are critical for industries such as automotive, aerospace, and medical devices.
The shift towards sustainable materials is also gaining traction. Bio-based plastics, made from renewable resources, are becoming more common as companies look to reduce their environmental impact. Composite materials, which combine different materials to create stronger plastic parts, are increasingly used in injection moulding processes to meet the demand for high-performance applications.
Automation and Robotics in Injection Moulding for Precision and Speed
Automation has been a game-changer in injection moulding, offering significant improvements in both speed and precision. The adoption of robotics and automated systems in injection moulding allows for the consistent production of high-quality plastic parts with minimal human intervention. Robots are able to perform tasks such as part removal, inspection, and assembly with unparalleled accuracy, reducing the risk of defects.
As production lines become more automated, the efficiency of injection moulding processes improves. Manufacturers can achieve faster turnaround times, which is crucial in meeting the demands of fast-paced markets. Automation also ensures consistency, ensuring that each part produced meets the same high-quality standards, which is essential in industries where precision is critical, such as medical or automotive sectors.
Additive Manufacturing and Injection Moulding Synergy
The integration of additive manufacturing (3D printing) and injection moulding is becoming increasingly popular, particularly in the prototyping and low-volume production stages. By combining these two technologies, manufacturers can take advantage of the flexibility offered by 3D printing while still maintaining the efficiency and scalability of injection moulding for mass production.
Additive manufacturing allows for rapid prototyping, enabling designers to quickly test and refine their ideas before committing to large-scale production. Once the design is finalized, injection moulding can be used to produce high volumes of parts with greater precision and faster cycle times. This synergy is revolutionizing the design process, offering manufacturers greater flexibility, faster time-to-market, and the ability to produce highly complex designs that were previously difficult or impossible to achieve.
Sustainable Practices in Injection Moulding Plastic Parts
Sustainability is becoming a key priority in manufacturing processes, and injection moulding is no exception. As environmental concerns continue to rise, manufacturers are looking for ways to reduce waste, lower energy consumption, and increase the use of recyclable materials. Sustainable injection moulding practices include using energy-efficient machinery, reducing scrap material, and incorporating recycled plastics into the production process.
Circular economy principles are also gaining momentum in the injection moulding industry. By designing plastic parts that are easier to recycle and reprocess, manufacturers can contribute to reducing the environmental impact of plastic products. In 2025, more companies are expected to adopt these sustainable practices, driven by both consumer demand and regulatory pressures to reduce plastic waste.
Smart Injection Moulding with IoT and Real-Time Monitoring
The integration of Internet of Things (IoT) technologies into injection moulding processes is enabling manufacturers to monitor and optimize production in real time. IoT devices can collect data from machines, sensors, and environmental conditions to provide valuable insights into the manufacturing process. This data allows for better quality control, predictive maintenance, and optimization of production schedules.
Real-time monitoring can also help reduce downtime by detecting issues before they become critical, allowing for quick interventions that prevent costly delays. By leveraging IoT and data analytics, manufacturers can improve overall efficiency and reduce the risk of defects in plastic parts.
Enhanced Surface Finishing Techniques for Superior Quality Plastic Parts
Surface finishing is a critical aspect of injection moulding, especially when it comes to the appearance and functionality of plastic parts. Advances in surface finishing technologies are allowing manufacturers to achieve superior aesthetics and performance. Techniques such as polishing, painting, and coating are being refined to create parts that are not only visually appealing but also more durable and resistant to wear and tear.
Surface quality is particularly important in industries such as automotive and consumer electronics, where the appearance of the plastic parts can significantly impact the product’s appeal. Enhanced surface finishes also improve the functionality of parts, making them more resistant to environmental factors such as heat, moisture, and UV radiation.
The Future of Injection Moulding: Trends to Watch Beyond 2025
As we look beyond 2025, the future of injection moulding for high-quality plastic parts is filled with exciting possibilities. Technologies such as artificial intelligence, machine learning, and advanced robotics are expected to further revolutionize the manufacturing process. These innovations will enable even greater precision, speed, and customization in the production of plastic parts.
Industry 4.0 principles, including automation, data analytics, and digital twins, will play an increasingly important role in injection moulding. As manufacturers continue to embrace these technologies, the injection moulding process will become even more efficient, cost-effective, and sustainable, meeting the demands of an ever-changing global market.
Conclusion: The Path Forward for Injection Moulding in 2025 and Beyond
The trends outlined in this article highlight the ongoing transformation of injection moulding for plastic parts. From advanced materials and automation to sustainability and smart manufacturing, the industry is poised for significant growth and innovation in 2025. By embracing these trends, manufacturers can not only improve the quality and efficiency of their production processes but also stay ahead in a competitive market. The future of injection moulding looks bright, and the possibilities for creating high-quality plastic parts are virtually limitless.