- February 21, 2025
- Posted by: feinuojixie
- Category: Injection Molding News
No Comments
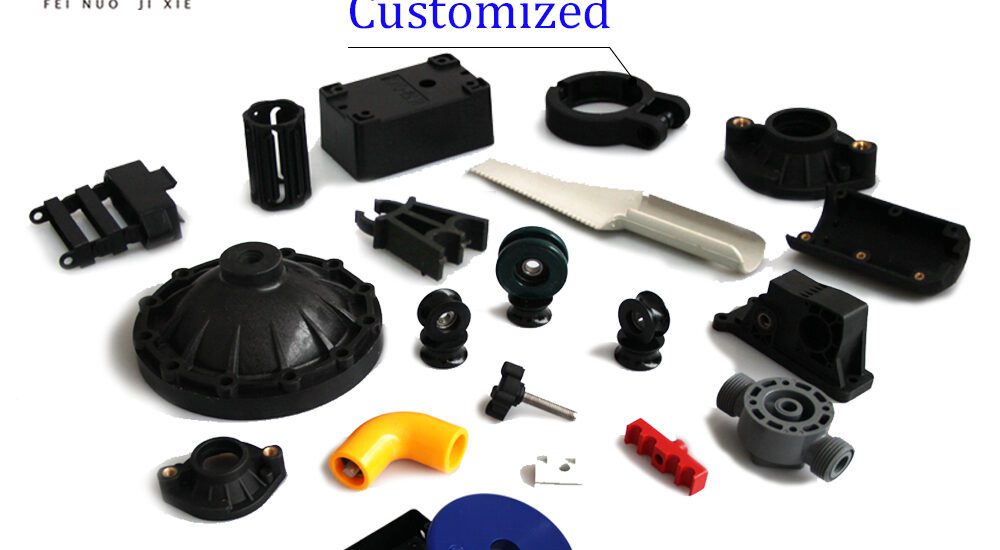
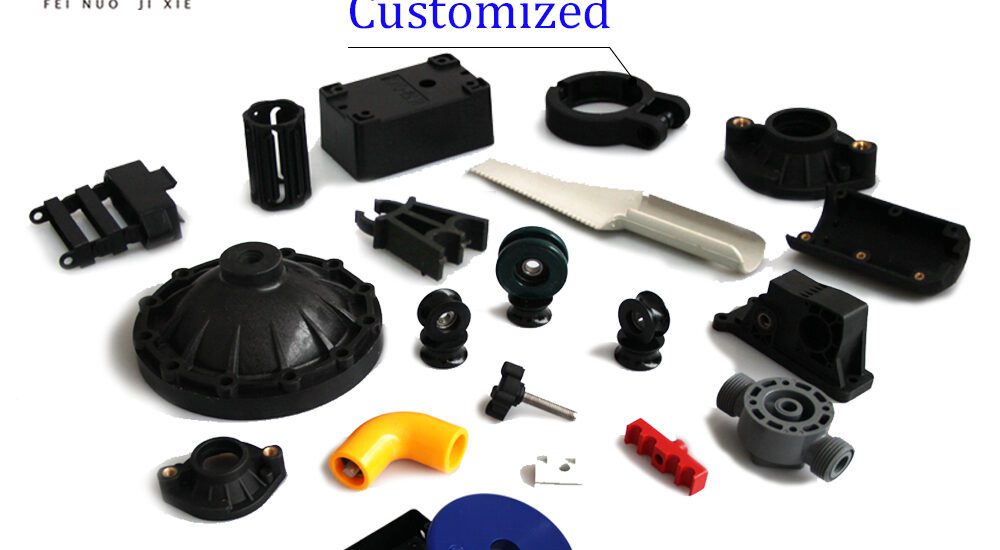
In the world of modern manufacturing, precision is no longer a luxury but a necessity. Whether it’s creating a tiny component for a smartphone or a large part for an automobile, the demand for accurate and high – quality parts is ever – increasing. This is where high – quality injection molded parts come into play, acting as the cornerstone of precision manufacturing.
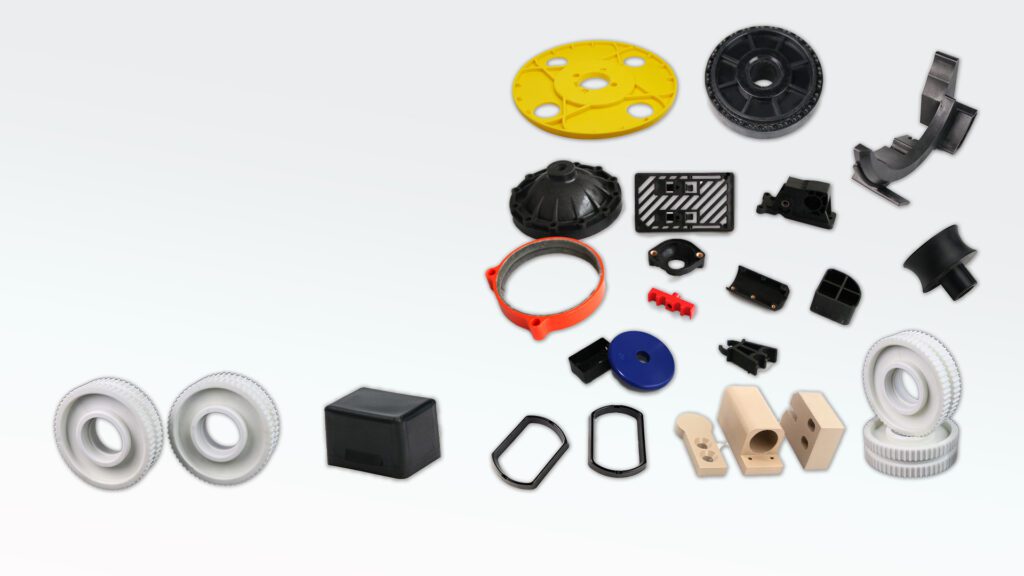
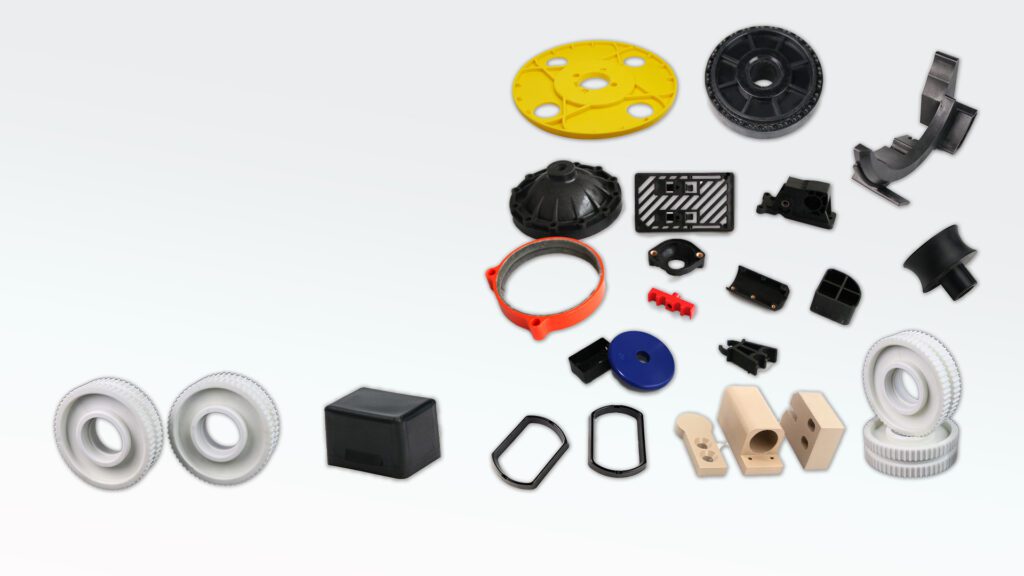
The Magic of Injection Molding Process
The injection molding process is a fascinating manufacturing technique. First, the raw material, usually in the form of plastic pellets, is melted in a heated barrel. Then, this molten material is injected at high pressure into a mold cavity. Once the material cools and solidifies inside the mold, the finished part is ejected. This process allows for the creation of parts with extremely tight tolerances. For example, parts with dimensional accuracies within ±0.001 inches can be produced, making it ideal for applications where precision is crucial.
Advantages of High – Quality Injection Molded Parts
One of the most significant advantages of high – quality injection molded parts is their dimensional accuracy. The molds used in the process are designed with great precision, ensuring that each part produced is an exact replica of the others. This consistency is vital in industries where parts need to fit together perfectly.
Material flexibility is another plus. Injection molding can work with a wide range of materials, from common plastics like polyethylene and polypropylene to high – performance engineering plastics. This allows manufacturers to choose the material that best suits the specific requirements of the part, such as strength, heat resistance, or chemical resistance.
In terms of cost – effectiveness, injection molding truly shines in mass production. Once the initial mold is created, the cost per part is relatively low, making it an economical choice for large – scale manufacturing.
Applications of Injection Molded Parts
In the automotive industry, injection molded parts are everywhere. They are used in interior components like dashboards, door panels, and seats, as well as exterior parts such as bumpers and body panels. These parts not only provide the necessary functionality but also contribute to the overall aesthetics of the vehicle.
In the electronics field, injection molded parts are crucial for housing electronic components. Their ability to be produced in complex shapes with high precision allows for the creation of sleek and compact device casings, like those for smartphones, tablets, and laptops.
In the consumer goods sector, injection molded parts are used in countless everyday products. From toys and kitchen utensils to furniture components, these parts are an integral part of our daily lives.
Ensuring Quality in Injection Molding
Advanced molds are the key to high – quality injection molded parts. These molds are made from high – grade materials and are designed using computer – aided design (CAD) and computer – aided manufacturing (CAM) technologies. This ensures that the mold has the correct dimensions and surface finish, which in turn affects the quality of the final part.
Quality control measures during production are also essential. This includes regular inspections of the parts during the molding process, using techniques such as optical inspection and dimensional measurement. Any defects, such as flash (excess material) or voids (holes in the part), can be detected and corrected immediately.
Material selection is another critical aspect. Using the right material for the job is crucial for ensuring the part’s performance and durability. For example, using a heat – resistant material for a part that will be exposed to high temperatures is essential.
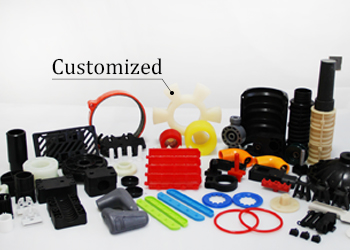
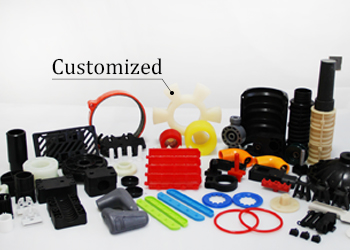
Challenges and Solutions in Injection Molding
Despite its many advantages, injection molding does face some challenges. Warping, where the part becomes distorted during cooling, and shrinkage, where the part reduces in size more than expected, are common issues.
To address warping, manufacturers can adjust the cooling rate, modify the part design to improve its structural integrity, or use mold inserts to control the cooling process. For shrinkage, accurate material selection, proper mold design, and controlling the injection pressure and temperature can help minimize the problem.
Future Trends in Injection Molding
The future of injection molding is full of exciting possibilities. One emerging trend is the use of 3D – printed molds. This technology allows for the rapid creation of molds with complex geometries, reducing the lead time for mold production. Another trend is the integration of sensors into the injection molding process. These sensors can monitor parameters such as temperature, pressure, and material flow, providing real – time data for better process control.
Conclusion
High – quality injection molded parts are undeniably the key to achieving precision in manufacturing. Their numerous advantages, wide range of applications, and the continuous improvement in the injection molding process make them an indispensable part of modern manufacturing. As manufacturers, embracing this technology and staying updated with the latest trends can give us a competitive edge in the global market. Let’s unlock the full potential of precision manufacturing with high – quality injection molded parts.