- February 28, 2025
- Posted by: feinuojixie
- Category: Injection Molding News
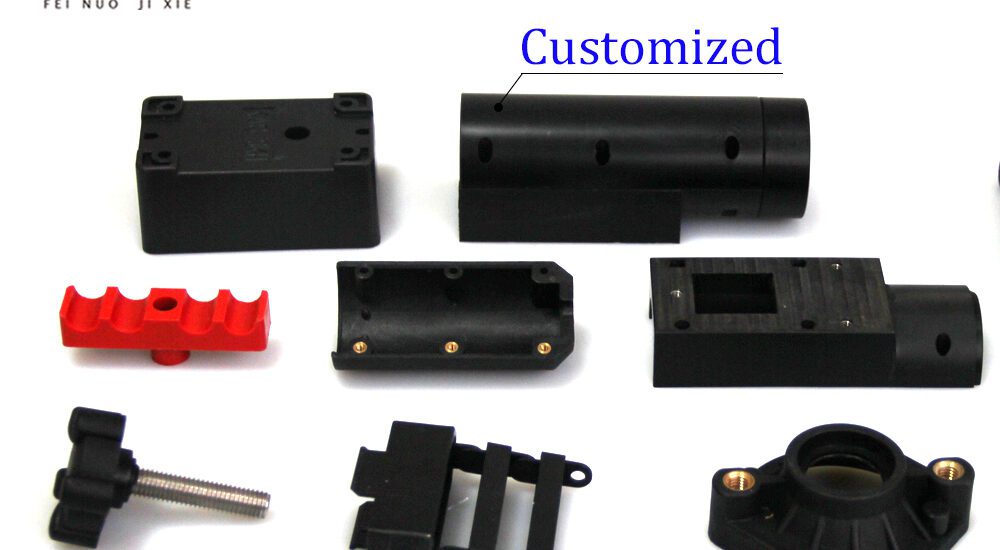
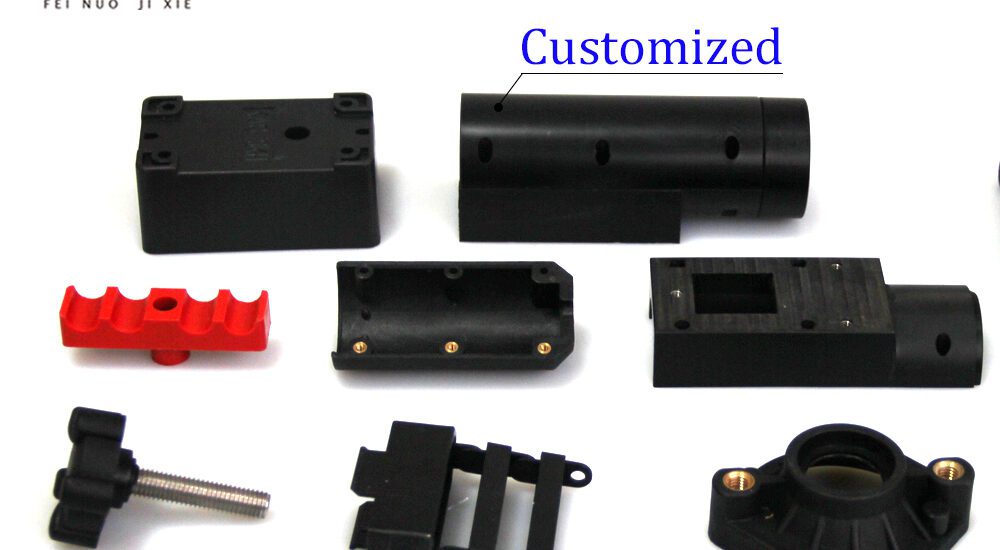
In recent years, injection molding has become a cornerstone of manufacturing across various industries. As the demand for high-quality, cost-effective products increases, manufacturers are turning to injection molding for its ability to produce complex parts with unparalleled precision. Injection molded parts have already transformed industries such as automotive, electronics, and medical devices, and the technology’s future looks promising. This blog post delves into why injection molded parts are revolutionizing manufacturing and how they will continue to shape the future of production.
What Is an Injection Molded Part? Understanding the Basics
At its core, an injection molded part is a component created through the injection molding process, where material (often plastic) is melted and injected into a mold to form a specific shape. The process allows manufacturers to produce parts in large quantities with consistent precision and minimal waste. Injection molding is capable of producing parts with intricate designs, tight tolerances, and complex geometries, making it an invaluable tool for modern production lines.
The Advantages of Injection Molded Part in Manufacturing
One of the most significant advantages of using injection molded parts is efficiency. The injection molding process enables high-volume production, meaning manufacturers can produce thousands—or even millions—of parts in a relatively short period. This scalability makes injection molding an ideal solution for industries that require mass production, such as automotive or consumer electronics.
Another key benefit is the precision of the parts. Injection molding allows for the creation of parts with consistent dimensions, ensuring that each part meets exact specifications. The process also offers cost-effectiveness, especially when compared to traditional methods such as machining or casting. Though the initial investment in machinery can be high, the long-term savings in labor and material costs make injection molding a highly efficient manufacturing method.
Industries That Benefit from Injection Molded Part Technology
-
Automotive Industry: In the automotive world, injection molded parts are crucial for producing everything from dashboards to engine components. The ability to create lightweight, durable parts that can withstand high temperatures is essential in the production of modern vehicles. Injection molded parts also contribute to reducing the overall weight of a vehicle, improving fuel efficiency and performance.
-
Electronics Industry: Consumer electronics like smartphones, computers, and wearables rely heavily on injection molded parts for housing and internal components. The ability to create complex shapes and integrate multiple functions into a single molded part is transforming the design and functionality of electronics.
-
Medical Devices: Precision and reliability are critical in medical devices, and injection molded parts meet these requirements. From surgical tools to disposable components, injection molding allows manufacturers to create high-quality, sterile, and functional medical devices that adhere to strict regulatory standards.
How Injection Molded Part Drives Innovation in Design
Injection molding opens the door to endless design possibilities. The process allows for a wide range of material choices, from standard plastics to high-performance resins, offering designers the flexibility to choose materials that meet specific strength, flexibility, and temperature requirements.
The intricacy of the designs possible through injection molding is another reason for its widespread use. Manufacturers can create parts with complex features, such as undercuts, ribs, and threads, which would be difficult or impossible to achieve using other manufacturing methods.
Additionally, sustainability is becoming a driving factor in design. Many manufacturers are turning to recycled materials and biodegradable plastics for injection molded parts, aligning with growing consumer and regulatory demand for eco-friendly products.
Future Trends in Injection Molded Part Technology
The future of injection molding lies in automation and smart manufacturing. With the integration of robots and advanced machinery, the efficiency of the injection molding process is set to improve, reducing human error and increasing production rates. Moreover, 3D printing and additive manufacturing are beginning to work in tandem with traditional injection molding techniques, enabling the creation of highly customized, small-batch parts that would previously have been difficult to produce.
Sustainability is also a significant trend moving forward. Manufacturers are exploring ways to incorporate recycled materials into injection molding processes, reducing waste and promoting a circular economy. The ability to recycle parts after their lifecycle will be key in reducing the environmental impact of mass production.
Overcoming Challenges in the Injection Molding Process
Despite its many advantages, the injection molding process comes with challenges. One common issue is material selection. While a wide variety of materials are available, each comes with its own set of properties, requiring manufacturers to carefully choose the right one for each application. Additionally, injection molding machines require routine maintenance to ensure consistent performance, and quality control measures are critical to ensuring that each part meets stringent standards.
Other challenges include managing production costs, especially during the prototyping phase. Though injection molding offers long-term savings, the initial mold design and production can be costly, which can be a barrier for smaller businesses or startups.
Injection Molded Part as a Pillar for Future Manufacturing
As manufacturing continues to evolve, injection molded parts will remain a fundamental technology driving innovation and efficiency. With its unmatched ability to produce complex, high-volume parts at a low cost, injection molding is poised to shape the future of industries ranging from automotive to medical devices. As new trends such as automation, 3D printing, and sustainability take hold, the role of injection molded parts in manufacturing will only become more significant in the years to come.