- March 17, 2025
- Posted by: feinuojixie
- Category: Injection Molding News
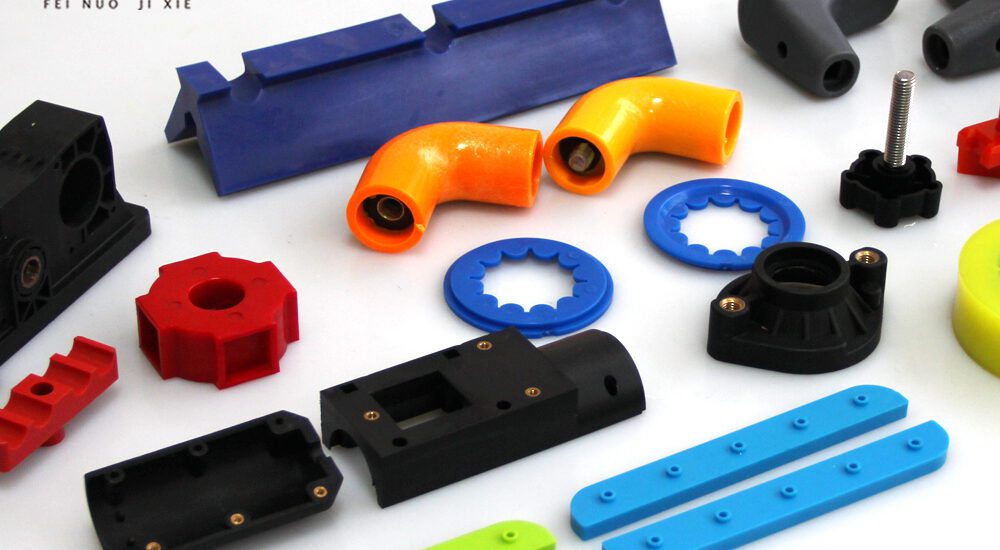
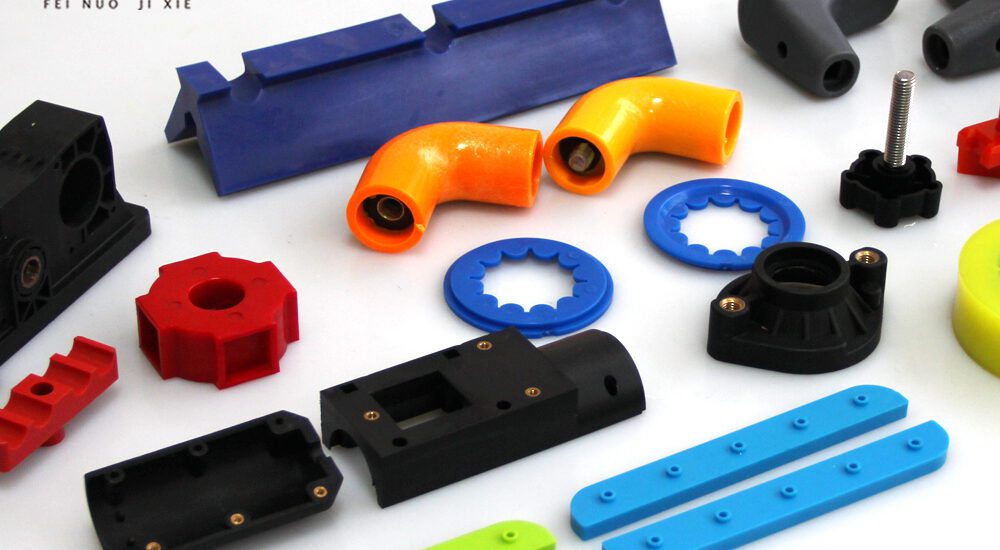
In the world of plastic manufacturing, ABS injection moulding is one of the most versatile and widely used methods for producing high-quality plastic parts. ABS (Acrylonitrile Butadiene Styrene) is a material prized for its strength, durability, and ease of moulding. This article will guide you through the secrets of achieving perfect results when using ABS plastic for injection moulding. Whether you’re in the automotive, electronics, or consumer goods industry, understanding the ins and outs of ABS injection moulding will ensure your plastic parts meet the highest standards of quality.
Understanding ABS Injection Moulding
ABS injection moulding is a process where molten ABS plastic is injected into a custom-designed mould under high pressure to form a solid part. The moulding process involves several stages: material preparation, injection, cooling, and ejection. By using precise control over temperature, pressure, and timing, manufacturers can produce consistent, durable parts in large volumes. ABS is favored for injection moulding because it offers a balanced combination of toughness, chemical resistance, and ease of processing.
Choosing ABS Plastic for Injection Moulding
ABS is the material of choice for many injection moulding applications due to its excellent balance of properties. It’s tough yet lightweight, resistant to impact, and offers a high degree of dimensional stability. These characteristics make ABS plastic a preferred choice for a wide range of industries, including automotive, electronics, and toys. Choosing ABS for injection moulding ensures that plastic parts are durable, resistant to wear and tear, and have the capacity to withstand harsh conditions.
The Injection Moulding Process for ABS Plastic Parts
The injection moulding process for ABS plastic parts involves several key steps. First, ABS plastic pellets are heated until they melt into a liquid. The molten plastic is then injected into a mould cavity under high pressure. Once the plastic fills the mould, it cools and solidifies, taking on the shape of the mould. The part is then ejected, and the cycle begins again. The key to perfect results is controlling factors such as temperature, injection speed, and pressure to ensure uniform filling and cooling, which ultimately results in high-quality plastic parts.
Design Considerations for ABS Injection Moulding
Designing for ABS injection moulding requires careful consideration to ensure the part is both functional and manufacturable. Factors such as wall thickness, gate placement, and part geometry all play a role in the final outcome. Thin walls may result in weak parts, while thick walls can lead to uneven cooling and warping. Designers must also consider the shrinkage rate of ABS during cooling and how the part will be ejected from the mould without causing damage. By optimizing these design aspects, manufacturers can achieve perfect results in ABS injection moulding.
Quality Control and Testing of ABS Plastic Parts
Maintaining high-quality standards throughout the ABS injection moulding process is crucial. Consistency in material properties, part dimensions, and surface finish are all essential for achieving the best results. Regular testing of ABS plastic parts ensures that they meet the desired specifications. Common testing methods include visual inspections, dimensional measurements, and mechanical testing to verify strength and durability. Implementing quality control procedures at each stage of the process helps prevent defects and ensures the final product meets industry standards.
Troubleshooting Common Issues in ABS Injection Moulding
While ABS injection moulding is a reliable process, common issues can arise that may affect the final product’s quality. Warping, sink marks, and air bubbles are some of the typical problems faced during production. These issues can be caused by improper cooling rates, incorrect mould design, or poor material handling. Understanding the root cause of these problems and adjusting process parameters such as temperature, injection pressure, and mould design can help mitigate these issues. By troubleshooting effectively, manufacturers can improve the quality and consistency of ABS plastic parts.
Advancements in ABS Injection Moulding Technology
As technology continues to evolve, so does the field of ABS injection moulding. New advancements in injection moulding machines, automation, and material formulations are improving the efficiency and precision of the process. Technologies such as 3D moulding, multi-material injection, and real-time process monitoring are pushing the boundaries of what’s possible in ABS plastic part production. These innovations not only enhance the quality of the final product but also reduce production costs and cycle times.
Conclusion
Mastering the art of ABS injection moulding is key to producing perfect, high-quality plastic parts. By understanding the intricacies of the process, optimizing designs, maintaining rigorous quality control, and embracing new technologies, manufacturers can unlock the full potential of ABS plastic. Whether you’re producing parts for critical industries or consumer products, achieving flawless results requires a deep understanding of the materials and processes involved. With the right knowledge and techniques, you can ensure that your ABS injection moulding projects are a success.