- March 5, 2025
- Posted by: feinuojixie
- Category: Injection Molding News
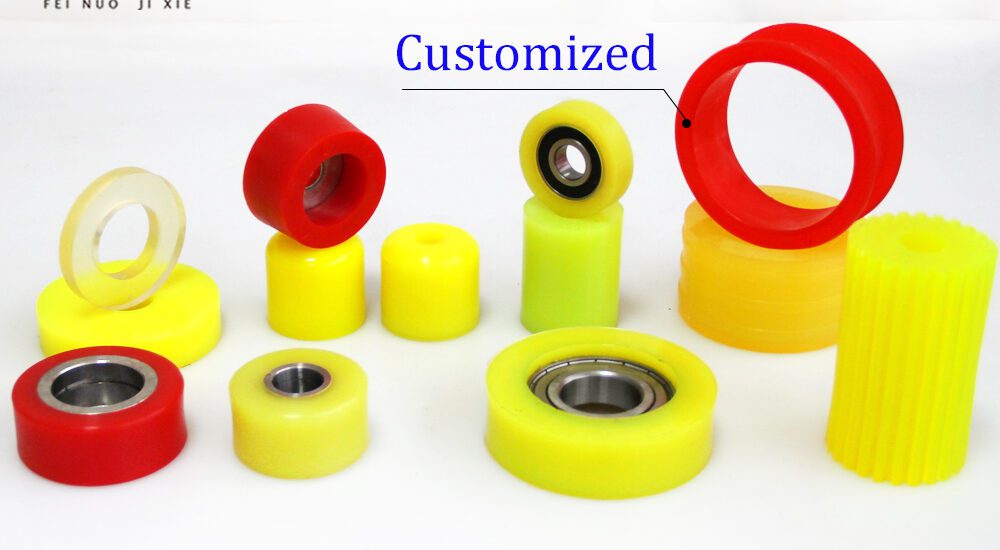
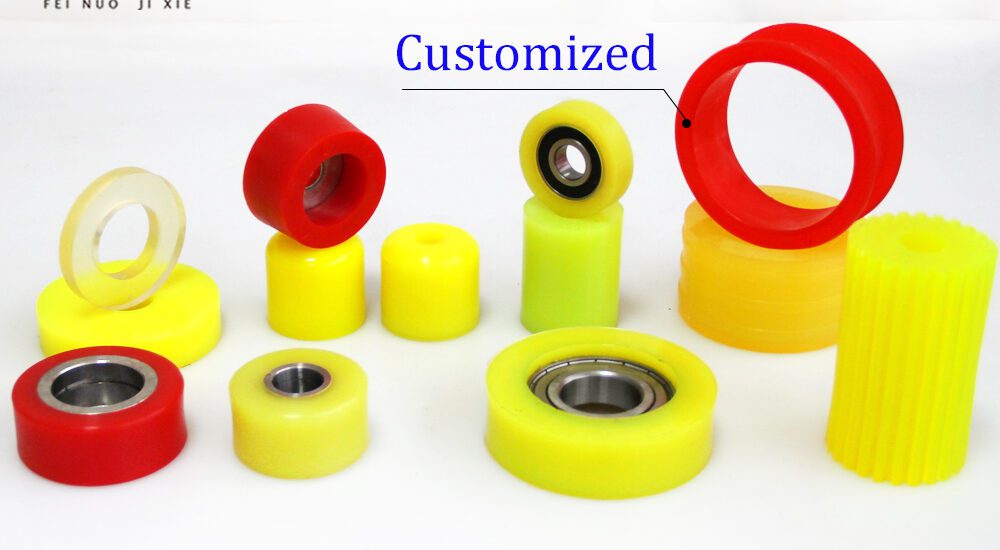
In the fast-paced world of manufacturing, the demand for high-quality, durable, and cost-effective plastic parts has never been higher. Injection moulding has emerged as a game-changer, enabling companies to produce complex plastic parts with unmatched precision. Whether you’re in the automotive, medical, or consumer electronics industry, injection moulding plastic parts has become an indispensable part of the production process. This article explores how injection moulding works, the materials involved, the design considerations, and how it’s reshaping industries across the globe.
Understanding Injection Moulding: The Process Behind Plastic Parts Creation
Injection moulding is a highly efficient manufacturing process used to create plastic parts. The process begins with the heating of plastic material, typically in pellet form, until it reaches a molten state. The molten plastic is then injected into a mold cavity under high pressure, where it fills the mold and takes its final shape. Once the plastic cools and solidifies, the part is ejected from the mold. This method is highly precise, enabling the creation of intricate, detailed plastic parts that are durable and consistent. The speed of the process and the ability to produce large volumes of parts make injection moulding an ideal choice for industries looking to streamline production.
The Role of Materials in Injection Moulding Plastic Parts
The materials used in injection moulding play a pivotal role in determining the performance and quality of the final plastic part. Common materials include thermoplastics such as ABS, polyethylene, and polypropylene, which are versatile, durable, and easily molded. Elastomers are used for parts that require flexibility, such as seals or rubber-like components. Composites, which combine plastic with fibers like glass or carbon, are used for parts that require added strength and durability. The choice of material depends on the specific requirements of the part, including its strength, flexibility, temperature resistance, and appearance. By selecting the appropriate material, manufacturers can ensure the production of plastic parts that meet the desired specifications.
Design Considerations for Injection Moulding Plastic Parts
When designing plastic parts for injection moulding, several factors must be considered to ensure successful production. One of the most important considerations is wall thickness. Consistent wall thickness is essential to prevent warping and ensure even cooling. Uneven wall thickness can result in defects such as shrinkage or poor part quality. Another key factor is part geometry. While simple shapes are easier to mould, complex geometries may require specialized molds and careful attention to material flow. Designers must also consider features like gates, runners, and vents in the mold, as these affect how the molten plastic flows into the cavity and solidifies. With careful design, manufacturers can optimize the injection moulding process to produce high-quality, functional plastic parts.
The Benefits of Injection Moulding for Plastic Parts Production
Injection moulding offers several advantages that make it the go-to solution for producing plastic parts at scale. One of the biggest benefits is cost-effectiveness. Once a mold is created, producing additional plastic parts is relatively inexpensive, making it ideal for high-volume production runs. The precision of injection moulding also ensures that parts meet tight tolerances, reducing the need for rework and improving the overall quality of the product. Additionally, the speed of the process means that parts can be produced quickly, enabling companies to meet tight production deadlines. Injection moulding’s versatility also allows manufacturers to produce parts of varying sizes and complexities, making it a valuable tool across a wide range of industries.
Challenges in Injection Moulding Plastic Parts Production
While injection moulding offers numerous benefits, it is not without its challenges. One common issue is warping, which occurs when parts cool unevenly, causing them to bend or distort. This can be mitigated through careful mold design and temperature control. Shrinkage is another challenge, as plastic parts may shrink slightly as they cool. This can be accounted for during the design phase to ensure that the final part meets the required specifications. Cycle time optimization is also a consideration, as manufacturers aim to reduce the time it takes to produce each part without compromising quality. With the right techniques and process controls, these challenges can be effectively managed, leading to successful production runs.
Applications of Injection Moulding Plastic Parts in Various Industries
Injection moulding plastic parts are used in a wide range of industries, each with its own unique requirements. In the automotive industry, injection moulding is used to create lightweight, durable parts such as dashboard components, exterior trim, and interior fittings. In consumer electronics, it is used for creating casings, connectors, and other components that require precision and durability. The medical industry also relies on injection moulding to produce high-quality, sterile components such as syringes, medical devices, and surgical tools. In packaging, injection moulding is used to produce custom, eco-friendly packaging solutions. As industries continue to evolve, injection moulding plastic parts remain a critical technology in meeting the demands of modern manufacturing.
Advanced Injection Moulding Techniques for High-Quality Plastic Parts
The injection moulding industry has seen significant advancements in recent years, with new techniques and technologies emerging to improve production efficiency and part quality. One such advancement is multi-material moulding, which allows different types of plastic to be injected into a single mold to create parts with varying properties. This technique is particularly useful for parts that require a combination of flexibility and rigidity. Another exciting development is the integration of additive manufacturing, which enables rapid prototyping and the creation of complex, customized parts that would be difficult to produce with traditional moulding methods. Smart moulding technologies are also enhancing the precision and efficiency of the injection moulding process, incorporating sensors and automation to optimize production and reduce waste.
Sustainability in Injection Moulding Plastic Parts Production
As sustainability becomes an increasing focus for manufacturers, injection moulding is leading the way in reducing waste and improving energy efficiency. One major benefit of injection moulding is the ability to recycle scrap material, reducing the amount of plastic waste generated during production. Additionally, modern injection moulding machines are designed to be more energy-efficient, using less power to heat and cool the molds. Manufacturers are also turning to eco-friendly materials, such as biodegradable plastics and recycled plastics, to create injection moulded parts that have a lower environmental impact. By incorporating sustainable practices, injection moulding is helping to make plastic parts production more environmentally friendly.
The Future of Injection Moulding Plastic Parts: Trends and Innovations
The future of injection moulding is bright, with several trends and innovations on the horizon. Automation is expected to play a significant role in improving production efficiency, reducing costs, and increasing consistency. The integration of artificial intelligence and machine learning will allow manufacturers to optimize the injection moulding process in real-time, leading to higher-quality parts and faster production times. 3D printing is also likely to continue to evolve, allowing for more complex and customized parts to be created alongside traditional injection moulding. These advancements will further revolutionize plastic parts manufacturing, making it more efficient, cost-effective, and sustainable.
Conclusion: Embracing the Potential of Injection Moulding Plastic Parts
Injection moulding has revolutionized the way plastic parts are produced, offering unparalleled precision, cost-efficiency, and versatility. From automotive to medical to consumer electronics, the applications of injection moulding are vast and diverse. As technology continues to evolve, the future of plastic parts manufacturing is set to become even more efficient and sustainable. By embracing these advancements, manufacturers can stay competitive and continue to innovate in an ever-changing marketplace.