- May 4, 2025
- Posted by: feinuojixie
- Category: Injection Molding News
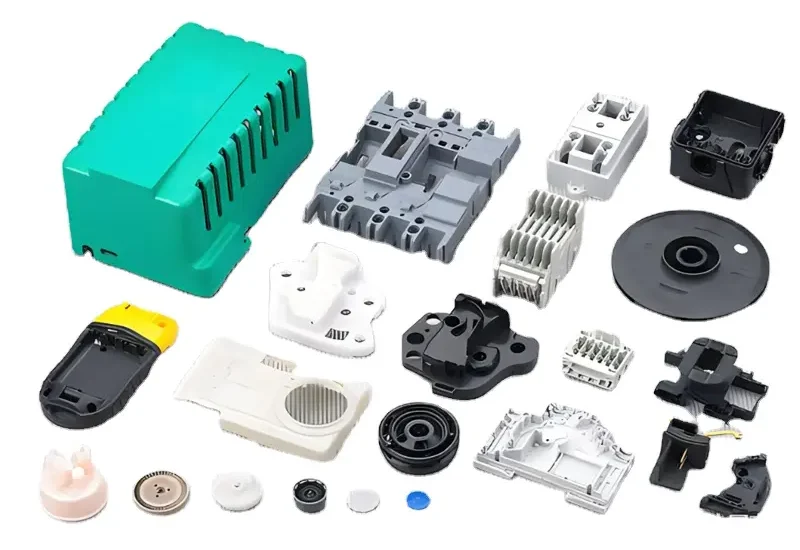
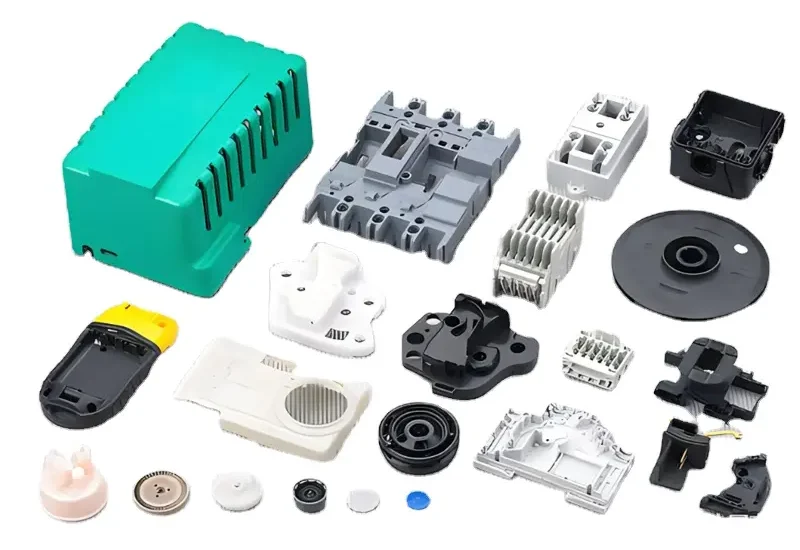
Large part injection molding plays a pivotal role in the manufacturing of complex, high-quality components that are used across various industries, including automotive, aerospace, and consumer goods. This advanced form of injection molding enables the production of parts that are not only large but also require high precision and performance. From the automotive bumpers to the body panels of aircraft, the process ensures that these parts meet the stringent requirements of strength, durability, and cost-effectiveness.
The process involves injecting molten material into a mold cavity under high pressure, where it cools and solidifies to form the desired shape. However, large part injection molding presents unique challenges compared to standard injection molding. The scale of the parts, along with the need for specialized molds and equipment, adds layers of complexity to the process. Mastering these intricacies is crucial for manufacturers who aim to meet the ever-increasing demands for large, high-performance parts.
In this guide, we will explore the core principles of large part injection molding, delve into the challenges and opportunities it presents, and provide insights into how manufacturers can optimize their processes for improved efficiency and product quality. By understanding these key aspects, manufacturers will be better equipped to navigate the world of large part injection molding and unlock its full potential.
Understanding the Fundamentals of Injection Molding
Injection molding is one of the most versatile manufacturing processes used to create parts with complex geometries and precise dimensions. In the traditional process, material in the form of pellets or granules is melted and injected into a mold cavity under high pressure, where it cools and solidifies. For large part injection molding, the same fundamental principles apply, but the scale and requirements of the mold, material, and machinery differ significantly.
The basic components of injection molding include the injection unit, the mold, and the clamping unit. The injection unit is responsible for melting and injecting the material, while the mold is the cavity that determines the shape of the part. The clamping unit holds the two halves of the mold together under pressure during injection.
In the case of large parts, the scale of these components increases. For example, the clamping force must be much higher to ensure that the large mold halves remain closed under the pressure of the injected material. Similarly, the injection unit needs to be capable of injecting large volumes of material at the correct pressure and speed to ensure that the part is molded consistently and with the desired properties.
Compared to small part injection molding, large part injection molding requires more advanced machinery and a better understanding of how material flows, cools, and solidifies in large molds. This knowledge is essential for minimizing defects like warping, sink marks, or air traps, which are more likely to occur in larger parts due to the greater volume of material involved.
Challenges in Large Part Injection Molding
While large part injection molding offers great potential, it also comes with a unique set of challenges that require careful consideration and expertise. One of the main issues that manufacturers face is material flow. When molding large parts, ensuring that the molten material flows evenly and fills the entire mold cavity is crucial to avoid defects.
Another common challenge is the cooling process. Large parts require longer cooling times due to their size, and uneven cooling can lead to part deformation, such as warping. Effective cooling system designs are essential to ensuring that the material cools evenly, preventing shrinkage or dimensional changes that can compromise the quality of the final product.
Moreover, the durability of the mold itself is a concern. Larger molds are subject to higher stresses during the injection process, which can lead to premature wear or even mold failure if not properly designed and maintained. Managing these issues requires a combination of skilled engineering, robust material choices, and innovative techniques.
Designing for Large Part Injection Molding
Designing large parts for injection molding requires more than just scaling up a traditional design. A well-designed large part will not only meet functional and aesthetic requirements but will also ensure that the molding process runs efficiently and produces consistent, high-quality results.
The first consideration when designing large parts is material selection. The material used must not only meet the performance requirements for the end product but also be compatible with the injection molding process. Certain materials may require higher temperatures or different injection speeds, which must be taken into account when selecting the mold and machinery.
Next, designers need to account for factors such as wall thickness, gating, and cooling channels. In large part injection molding, it is crucial to ensure that the material flows uniformly into the mold cavity. This requires careful placement of gates and runners to direct the material flow. Additionally, optimizing the placement and design of cooling channels is key to minimizing cooling times and reducing the risk of part distortion.
Another critical aspect of design is the prevention of warping and shrinkage. Large parts tend to shrink unevenly as they cool, leading to distortions in shape. By using advanced molding techniques, such as controlled cooling and the addition of reinforcements, designers can reduce these issues and improve the overall quality of the final part.
Choosing the Right Equipment for Large Part Injection Molding
Selecting the proper equipment is crucial for successful large part injection molding. The injection molding machine plays a central role in ensuring that the process runs smoothly and that large parts are molded accurately.
For large part injection molding, machines with a higher clamping force are required. The clamping force needed is directly proportional to the size and complexity of the mold, as well as the material being used. A machine with insufficient clamping force can lead to defects like flash (excess material around the part) or incomplete filling of the mold.
Additionally, the size of the injection unit is important. Larger parts require machines with higher injection capacities to handle the larger volume of material. The injection speed must also be optimized to ensure that the material is injected at the correct rate to avoid defects such as air pockets or incomplete molding.
Automation plays a key role in large part injection molding, particularly when it comes to post-production handling and assembly. Robotic arms and automated systems can help with part removal, trimming, and assembly, reducing labor costs and improving overall efficiency.
Techniques for Preventing Common Issues in Large Part Injection Molding
Preventing defects in large part injection molding requires a proactive approach. Some of the most common issues in large part injection molding include sink marks, air traps, and warping.
Sink marks are depressions that occur on the surface of the part, usually due to uneven cooling or inconsistent material flow. To avoid sink marks, it’s important to carefully manage the cooling process and ensure that the material is distributed evenly throughout the mold.
Air traps occur when air becomes trapped in the mold cavity, leading to voids or bubbles in the part. These can be minimized by optimizing the placement of vents and ensuring that the material flows smoothly into the mold.
Warping is another common issue that results from uneven cooling or material shrinkage. Using a well-designed cooling system and controlling the cooling rate can significantly reduce the risk of warping. Reinforcements and thicker sections can also help maintain the shape of the part during cooling.
The Role of Materials in Large Part Injection Molding
The choice of material is crucial when it comes to large part injection molding. Different materials offer varying characteristics in terms of strength, flexibility, and durability, and selecting the right material is essential for ensuring the performance of the final product.
Common materials used in large part injection molding include thermoplastics like ABS, polycarbonate, and polyethylene, as well as thermosetting plastics such as epoxy. The material selection process depends on the intended use of the part, as well as the required properties like impact resistance, chemical resistance, and thermal stability.
Innovations in material science continue to impact the field of large part injection molding. New materials, such as high-performance polymers and composites, are being developed to provide superior strength, heat resistance, and weight reduction, making them ideal for industries like automotive and aerospace.
The Future of Large Part Injection Molding
As industries continue to demand larger and more complex parts, the future of large part injection molding looks promising. Emerging technologies, such as 3D printing and advanced robotics, are playing a significant role in improving the efficiency and accuracy of large part molding processes.
The use of simulation software is also on the rise, enabling manufacturers to predict and address potential issues in the molding process before production begins. This can lead to faster prototyping, reduced costs, and higher-quality parts.
Looking ahead, the development of new materials and the ongoing optimization of injection molding machines will continue to drive innovation in large part molding. As manufacturers seek to meet the ever-increasing demands for large, high-performance components, the future of large part injection molding will be defined by continued advancements in technology, design, and material science.
Conclusion
Large part injection molding is a complex but essential process that enables the production of high-quality, durable components for a wide range of industries. By understanding the fundamentals, addressing the challenges, and optimizing design and equipment choices, manufacturers can unlock the full potential of this powerful manufacturing method.
With continued advancements in technology and materials, the future of large part injection molding promises even greater opportunities for innovation and efficiency. Manufacturers who embrace these changes and continuously refine their processes will be well-positioned to succeed in the competitive world of large part production.