- April 2, 2025
- Posted by: feinuojixie
- Category: Injection Molding News
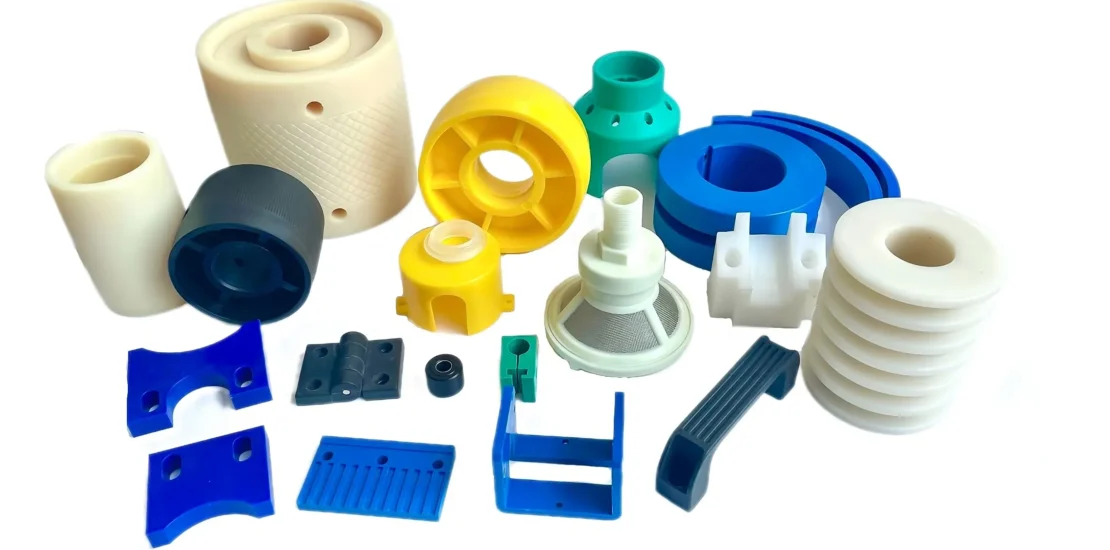
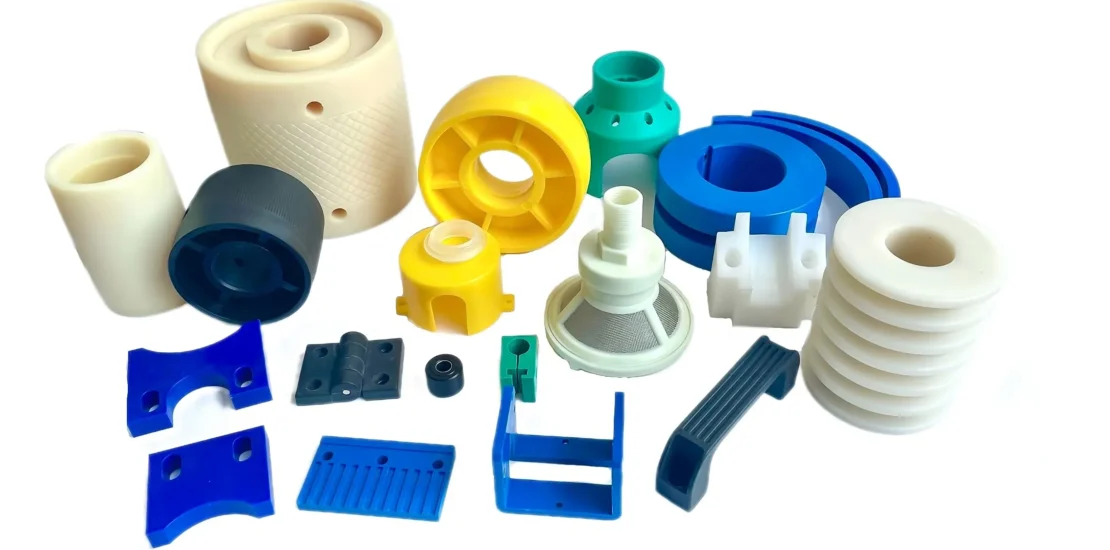
In the world of modern manufacturing, injection molding plays a crucial role in producing high-precision plastic components for various industries. Whether in automotive, medical, or consumer goods, manufacturers rely on injection molding machines to deliver consistent and high-quality products. However, the efficiency and longevity of these machines heavily depend on the quality of their parts.
Using top-quality injection machine part ensures smooth operation, minimizes downtime, and maintains production consistency. From the injection unit to the mold system, every component plays a significant role in determining the overall performance of the machine. This article explores the most essential injection machine part, how to choose the best components, and why investing in quality is a game-changer for your production line.
Understanding Injection Machine Part and Its Role in Production
An injection molding machine consists of multiple interconnected components, each playing a vital role in shaping the final product. Understanding how these parts function helps manufacturers optimize production and ensure high-quality output.
The key injection machine part includes the injection unit, responsible for melting and injecting plastic into the mold; the clamping system, which holds the mold in place during the process; the mold system, which defines the shape of the final product; the ejection system, which ensures smooth product removal; and hydraulic and electrical components, which provide the necessary power and control for seamless operation.
Choosing high-performance components for each system is crucial for achieving precision, reducing waste, and increasing production efficiency.
Essential Injection Machine Part for High-Performance Manufacturing
Injection Unit: The Heart of the Process
The injection unit consists of key components such as the barrel, screw, and nozzle. The screw and barrel work together to melt and mix plastic materials, ensuring a uniform and consistent flow. A high-quality nozzle ensures precise injection into the mold, preventing material leakage and inconsistencies. Upgrading these components improves melting efficiency, reduces cycle time, and enhances overall product quality.
Clamping System: Stability and Strength
The clamping system is responsible for holding the mold in place during injection and cooling. A reliable toggle clamp or hydraulic clamp ensures even pressure distribution, preventing mold misalignment or flashing defects. Investing in a strong clamping system enhances mold protection and extends the lifespan of both the mold and machine.
Mold System: The Core of Precision Molding
The mold system determines the shape and surface finish of the final product. Mold bases, inserts, and cavity plates must be crafted from durable, high-precision materials to ensure accuracy and repeatability. A well-maintained mold system reduces defects such as warping, sink marks, or incomplete fills.
Ejection System: Smooth and Efficient Product Removal
Once the molding process is complete, the product needs to be ejected efficiently. Ejector pins, plates, and sleeves facilitate smooth removal without damaging the molded part. High-quality ejection components reduce cycle time and prevent defects such as stress marks or deformation.
Hydraulic and Electrical Components: Powering the Machine
The hydraulic and electrical systems control the movement, pressure, and speed of the injection molding machine. Hydraulic pumps, valves, controllers, and sensors ensure smooth operation and precision control. Investing in advanced electrical components improves energy efficiency and automation capabilities, allowing for more consistent production results.
How to Choose the Best Injection Machine Part for Your Needs
Selecting the right injection machine part is crucial for maintaining performance and efficiency. Consider the following factors:
-
Material Quality: Opt for components made from high-grade steel, alloy, or wear-resistant materials.
-
Compatibility: Ensure the parts fit your specific injection molding machine model.
-
Durability: Look for components with a proven track record of longevity and resistance to wear.
-
Manufacturer Reputation: Work with trusted suppliers who provide certified, precision-engineered parts.
Upgrading to high-quality components reduces long-term costs by minimizing breakdowns and maintenance requirements.
Benefits of Using High-Quality Injection Machine Part
Investing in superior injection machine part brings numerous benefits to manufacturers:
-
Enhanced Efficiency: Improved component performance leads to faster cycle times and increased production output.
-
Consistent Product Quality: Precision-engineered parts ensure accurate molding, reducing defects and material waste.
-
Lower Maintenance Costs: Durable components require less frequent replacements, minimizing downtime and repair expenses.
-
Better Energy Efficiency: Advanced hydraulic and electrical components reduce power consumption, leading to cost savings.
By choosing high-quality parts, manufacturers can optimize production processes and improve overall profitability.
Common Issues with Low-Quality Injection Machine Part
Using substandard injection machine part can negatively impact production in several ways:
-
Poor Precision: Low-quality screws, barrels, or molds can cause uneven material flow and inconsistent product dimensions.
-
Frequent Breakdowns: Inferior hydraulic pumps, clamps, or electrical components may fail prematurely, leading to costly repairs.
-
Product Defects: Warping, flashing, short shots, and sink marks are common defects resulting from poor-quality parts.
-
Increased Operating Costs: Frequent part replacements and extended downtime increase production costs and reduce profitability.
Avoiding these issues starts with investing in reliable, high-performance machine components.
Where to Source Top-Quality Injection Machine Part
To ensure you get the best components for your injection molding machine, consider these sourcing tips:
-
Partner with Reputable Manufacturers: Look for suppliers with industry certifications and a history of delivering high-quality parts.
-
Verify Quality Standards: Choose components that meet international quality certifications such as ISO or CE.
-
Request Custom Solutions: Some manufacturers offer custom-designed parts tailored to your specific production needs.
-
Read Reviews and Testimonials: Customer feedback can provide insights into the reliability and performance of different suppliers.
Choosing the right supplier guarantees long-term performance and a better return on investment.
Conclusion
Manufacturers who invest in top-quality injection machine part benefit from improved product consistency, reduced downtime, and lower long-term costs. High-quality components not only extend the lifespan of the machine but also ensure smoother operation and fewer defects in the final products.
To maintain peak performance, always choose reliable suppliers, verify material quality, and prioritize parts that align with your machine’s specifications. Whether you are looking to upgrade your existing setup or replace worn-out components, investing in the best injection machine part is a crucial step toward optimizing your production process.
By making the right choices, you can ensure a more efficient, cost-effective, and high-quality manufacturing operation that meets industry demands and customer expectations. Now is the perfect time to upgrade your injection machine part and take your production to the next level.