- March 17, 2025
- Posted by: feinuojixie
- Category: Injection Molding News
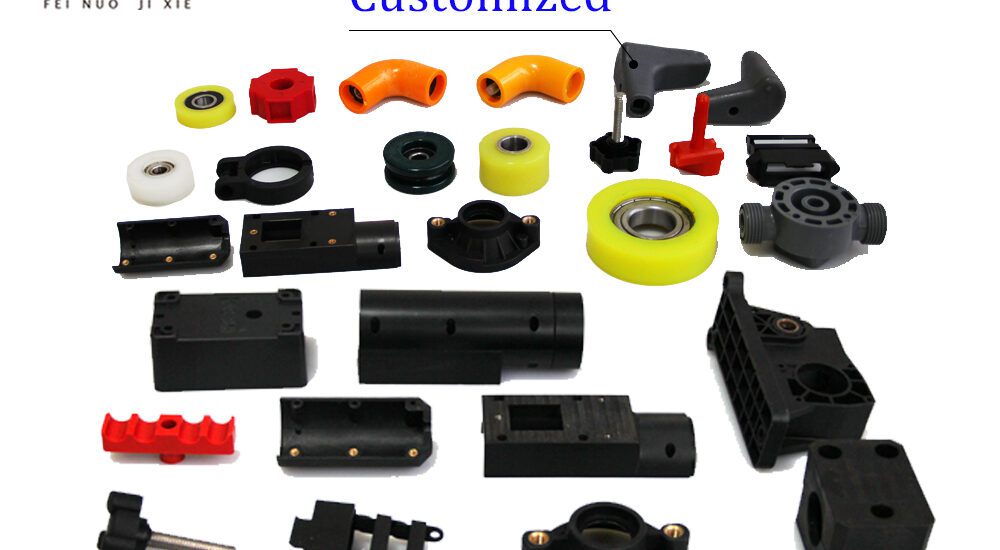
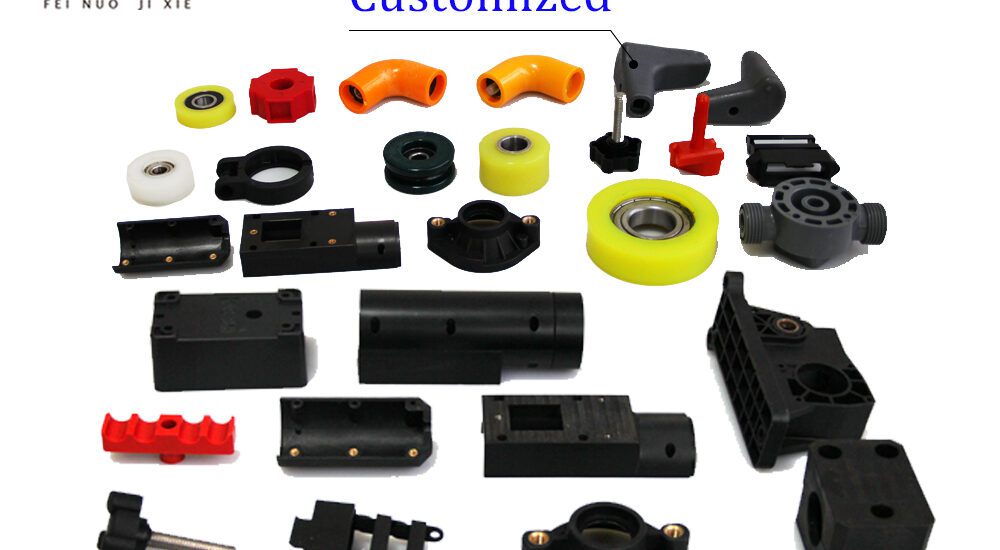
ABS injection moulding has revolutionized the way manufacturers produce durable, high-quality plastic parts. This process involves injecting molten ABS plastic into a mould cavity to form precise, complex shapes. It’s a highly efficient and scalable method that has gained significant traction in various industries due to its exceptional qualities.
One of the key benefits of ABS injection moulding is its versatility. ABS plastic itself is known for its robust properties—offering high strength, resistance to impact, and thermal stability. These features make it ideal for creating plastic parts that are not only functional but also have the ability to withstand rough conditions over extended periods.
Additionally, ABS injection moulding allows for the creation of highly intricate designs with incredible accuracy. The process ensures that even the most detailed features of a product can be replicated consistently, making it an excellent choice for high-precision components.
In comparison to other injection moulding materials like polycarbonate or polyethylene, ABS stands out due to its ability to be processed at relatively lower temperatures, reducing energy consumption during production. This energy efficiency, combined with the material’s recyclability, makes ABS injection moulding a highly cost-effective option for manufacturers looking to reduce production costs without compromising on quality.
As industries push for more advanced product designs, ABS injection moulding continues to be at the forefront, offering a wide range of benefits that support modern manufacturing goals. From consumer goods to automotive applications, ABS plastic parts created through injection moulding are shaping the future of product design.
The Role of Injection Moulding in Modern Product Design
Injection moulding is a key player in modern product design, offering manufacturers a level of precision, consistency, and efficiency that is hard to match. This process is essential for producing complex shapes and parts with minimal waste. It works by injecting molten ABS plastic into a precisely crafted mould under high pressure, where it cools and solidifies into the desired shape.
One of the biggest advantages of injection moulding in product design is its ability to produce high volumes of identical parts with exacting precision. The process allows for intricate, detailed designs that can be replicated consistently without deviations, ensuring that each product meets quality standards. This capability is especially crucial in industries where product reliability and durability are paramount, such as automotive and electronics.
Moreover, injection moulding plays a significant role in reducing the need for manual labor and minimizing production costs. As the process is automated, it accelerates production times, enabling companies to manufacture products at a much faster rate compared to traditional methods. This scalability allows businesses to meet growing demands, whether they are producing small batches of bespoke parts or large-scale production runs.
The versatility of injection moulding also opens up opportunities for designers to explore innovative shapes and functionalities that were once considered impractical. With the precision of the moulding process, ABS plastic parts can have varying thicknesses, integrated components, and even intricate textures that add to the aesthetic appeal and functionality of the final product. This enables manufacturers to experiment with new designs, pushing the boundaries of what’s possible in product development.
Why ABS Plastic Is the Preferred Material in Injection Moulding
ABS plastic has become the go-to material for injection moulding due to its unique combination of properties that make it ideal for a wide range of applications. Its key characteristics, such as durability, impact resistance, and lightweight nature, make it the perfect choice for manufacturing parts that require both strength and ease of handling.
Durability is one of the most attractive features of ABS. It is highly resistant to physical wear and tear, making it a popular material choice for products that undergo regular handling or are exposed to tough environments. In addition to its physical resilience, ABS is also known for its resistance to chemicals and high temperatures, ensuring that the final product remains functional and intact under demanding conditions.
The lightweight nature of ABS plastic allows for the creation of parts that are easier to handle and transport without compromising on their strength. This is particularly important in industries such as automotive, where reducing the overall weight of components can significantly improve fuel efficiency and performance.
In addition to these material benefits, ABS is a cost-effective option for mass production. The material is readily available and easy to process, which helps to reduce production costs. Furthermore, ABS is highly recyclable, offering a more sustainable option for manufacturers looking to reduce their environmental footprint. As a result, ABS plastic provides an excellent balance of affordability, performance, and sustainability in injection moulding.
Innovation and Sustainability: ABS Injection Moulding’s Future Potential
ABS injection moulding is not only at the forefront of manufacturing innovation, but it also plays a crucial role in driving sustainability within the industry. As manufacturers are under increasing pressure to adopt greener practices, ABS stands out as a material that supports both innovation and environmental responsibility.
One of the major innovations in ABS injection moulding is the development of bio-based ABS plastic. These newer versions of ABS use renewable resources in their production, reducing reliance on fossil fuels and making the material more eco-friendly. This shift toward bio-based ABS helps manufacturers to meet sustainability goals while maintaining the high-quality standards expected of their products.
Technological advancements in injection moulding itself are also contributing to the sustainability of ABS plastic. For example, newer moulding techniques reduce waste by allowing more precise control over the amount of material used during the injection process. This results in fewer off-cuts and more efficient production, lowering the overall environmental impact.
Additionally, the use of 3D printing technology in conjunction with ABS injection moulding is helping to further revolutionize product design. 3D printing allows for rapid prototyping, which means that companies can test and iterate on new designs before committing to full-scale production. This reduces the need for large quantities of raw material and allows for more efficient testing of product ideas.
Industries Benefiting from ABS Injection Moulding
ABS injection moulding is transforming various industries by offering a versatile and cost-effective solution for creating durable, high-quality plastic parts. One of the primary sectors benefiting from ABS moulding is the automotive industry, where lightweight, high-strength parts are crucial for improving fuel efficiency and vehicle performance. Components such as dashboards, interior panels, and bumpers are often made from ABS, owing to its ability to withstand impacts while maintaining a low weight.
The electronics industry also relies heavily on ABS plastic parts, especially for devices that require intricate, compact designs. ABS is commonly used in the manufacturing of casings for smartphones, televisions, computers, and other electronic devices. Its ability to be moulded into complex shapes while remaining lightweight and durable makes it ideal for these applications.
In the consumer goods sector, ABS injection moulding is widely used to create everyday products such as kitchen appliances, toys, and personal care items. The material’s strength, combined with its aesthetic flexibility, allows manufacturers to design products that are both functional and appealing to consumers. ABS plastic parts can be easily coloured, textured, and finished to match product branding, further enhancing their appeal.
The Impact of ABS Injection Moulding on Product Design Flexibility
ABS injection moulding offers designers unprecedented flexibility in product development. One of the key advantages is the ability to create highly customized plastic parts that meet specific design requirements. ABS plastic can be moulded into intricate shapes, enabling designers to explore more complex and innovative concepts without worrying about limitations in material properties.
The integration of advanced technologies such as 3D printing with ABS injection moulding further expands design possibilities. Designers can create rapid prototypes and adjust their designs on the fly, making the product development process more efficient and dynamic. This flexibility is crucial in today’s fast-paced market, where speed to market is often a key competitive advantage.
Moreover, ABS injection moulding allows for faster iterations in design, enabling companies to test multiple versions of a product and refine it based on real-world feedback. This flexibility accelerates innovation and helps manufacturers bring better products to market more quickly.
The Cost-Efficiency of ABS Injection Moulding in Manufacturing
One of the most significant advantages of ABS injection moulding is its cost-effectiveness, particularly in large-scale manufacturing. While the initial investment in moulds and machinery can be substantial, the long-term benefits far outweigh the costs, especially when producing high volumes of plastic parts.
ABS plastic itself is relatively inexpensive, and because it can be processed quickly and efficiently, the overall production costs remain low. This makes it an ideal material for manufacturers who need to produce large quantities of parts without significantly increasing their budget. The high throughput of injection moulding allows manufacturers to meet demand at a competitive price point, all while maintaining high product quality.
Additionally, the reduced need for post-production work, such as sanding or finishing, further reduces costs. ABS plastic parts typically require little additional processing, which speeds up production timelines and reduces the overall labor required.
Looking Ahead: The Future of ABS Injection Moulding in Product Design
As technology continues to advance, the future of ABS injection moulding looks promising. The development of smarter, more efficient injection moulding machines and the continued evolution of ABS material science will open up even more possibilities for product design. In the coming years, we may see more industries embracing ABS injection moulding for creating complex, lightweight, and durable parts that meet growing consumer demands.
The integration of ABS with emerging technologies, such as artificial intelligence and machine learning, could further optimize the manufacturing process. These technologies can help to monitor production in real-time, ensuring that the highest standards of quality are maintained throughout the process.
As consumer expectations continue to evolve, ABS injection moulding will remain a key driver of innovation in product design. Whether it’s in creating new product categories, improving existing designs, or adopting more sustainable practices, ABS moulding will play a critical role in shaping the future of manufacturing.
Conclusion
In conclusion, ABS injection moulding is revolutionizing product design, offering manufacturers a versatile, cost-effective, and sustainable method of creating high-quality plastic parts. Its ability to combine strength, durability, and lightweight properties makes it ideal for a wide range of industries, from automotive to electronics. With continued advancements in technology and a growing emphasis on sustainability, ABS injection moulding will undoubtedly remain at the forefront of innovation, shaping the future of product design for years to come. By adopting this cutting-edge manufacturing technique, companies can stay competitive and meet the ever-growing demands of the global marketplace.