- March 21, 2025
- Posted by: feinuojixie
- Category: Injection Molding News
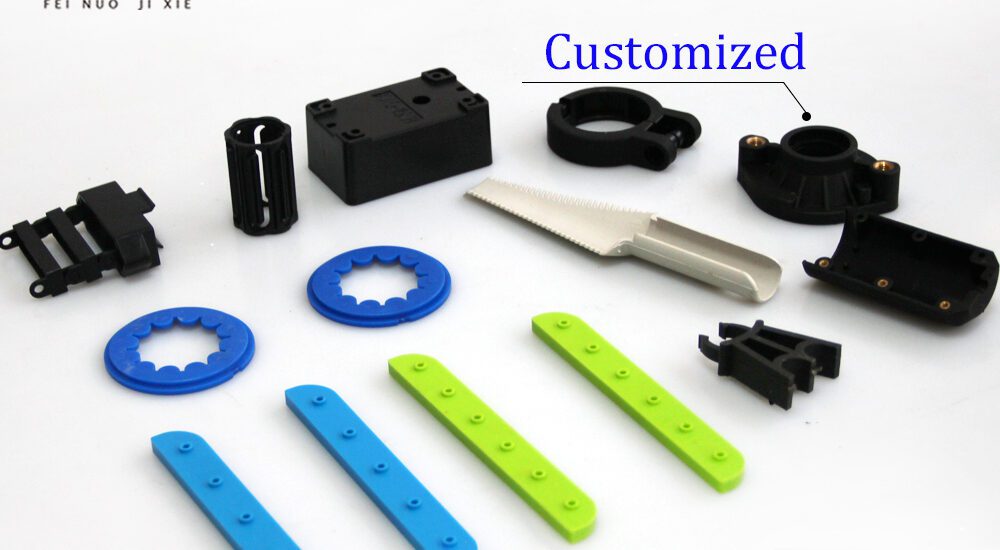
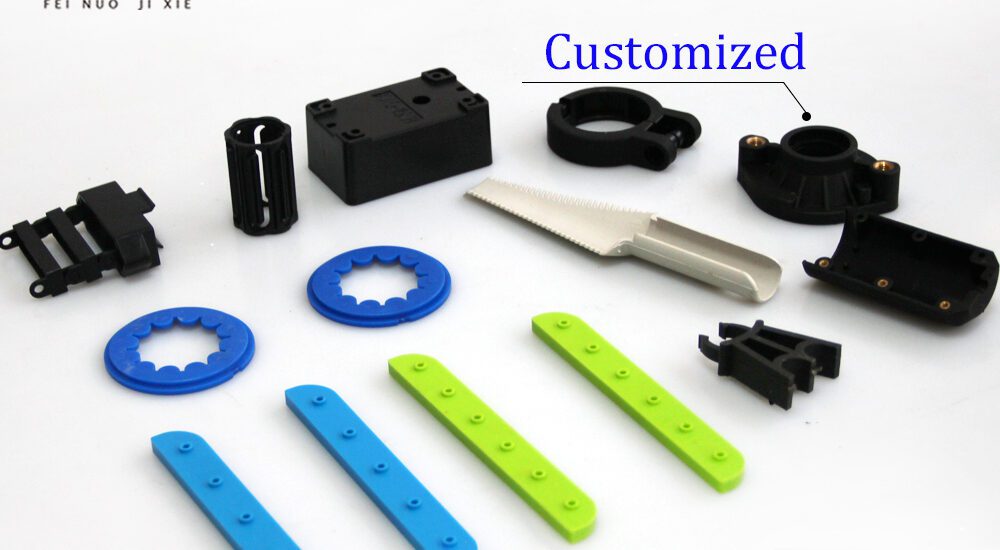
ABS injection moulding has become a cornerstone of modern plastic manufacturing, offering unparalleled strength, durability, and versatility. Whether for automotive components, consumer electronics, or household appliances, ABS (Acrylonitrile Butadiene Styrene) stands out as a go-to material for high-quality, long-lasting plastic products.
This advanced moulding technique ensures precision, efficiency, and cost-effectiveness, making it a preferred choice for manufacturers worldwide. As industries seek reliable and robust materials, ABS injection moulding continues to lead the way, providing the perfect balance of strength, aesthetics, and affordability.
What Is ABS Injection Moulding?
ABS injection moulding is a manufacturing process that involves injecting molten ABS (Acrylonitrile Butadiene Styrene) into a mould to create durable plastic products. ABS is a thermoplastic polymer known for its excellent strength, impact resistance, and smooth surface finish.
The injection moulding process begins with heating ABS resin until it melts. The molten material is then injected into a mould cavity under high pressure. Once cooled and solidified, the mould opens, and the final product is ejected. This method allows manufacturers to produce precise and complex plastic components efficiently and at scale.
Advantages of ABS Injection Moulding for Durable Plastic Products
High Impact Resistance
ABS injection moulding is widely used for products that require toughness and durability. The combination of acrylonitrile, butadiene, and styrene gives ABS high impact resistance, making it ideal for applications that must withstand physical stress without cracking or breaking.
Superior Strength and Toughness
ABS is known for its excellent mechanical properties. Unlike brittle plastics, ABS maintains its structural integrity even under extreme conditions. This makes it a preferred choice for applications where strength and long-term durability are essential.
Excellent Surface Finish
One of the standout benefits of ABS injection moulding is the high-quality finish it provides. ABS can be easily polished, textured, or coated, making it suitable for products that require an attractive and professional appearance. This is particularly valuable in consumer electronics, automotive interiors, and household appliances.
Precision and Complex Design Capabilities
The injection moulding process enables manufacturers to create highly detailed and complex designs with precision. ABS injection moulding ensures consistency across production runs, making it ideal for intricate components that require tight tolerances.
Cost-Effective and Efficient Production
ABS injection moulding is highly efficient, allowing mass production of high-quality plastic parts at a lower cost. The process minimizes material waste, reduces production time, and enhances overall cost-effectiveness, making it a popular choice for large-scale manufacturing.
Common Applications of ABS Injection Moulding
Automotive Components
ABS injection moulding plays a critical role in the automotive industry. From dashboards and interior trims to exterior parts, ABS provides the durability and aesthetic appeal required in modern vehicle design. Its impact resistance makes it an excellent material for safety-related components as well.
Consumer Electronics
Many electronic devices rely on ABS injection moulding for their casings and structural components. Laptops, remote controls, gaming consoles, and smartphones often feature ABS enclosures due to its strength, lightweight nature, and ability to support detailed designs.
Household Appliances
ABS is widely used in the production of household appliances such as vacuum cleaners, kitchen gadgets, and air conditioners. The material’s durability and smooth surface make it ideal for products that are frequently handled and exposed to varying temperatures.
Medical Devices
The medical industry benefits from ABS injection moulding due to its hygienic properties, ease of sterilization, and resistance to chemicals. From diagnostic equipment to protective housings for medical devices, ABS ensures reliability and long-lasting performance.
Environmental and Sustainability Aspects of ABS Injection Moulding
Recyclability of ABS
ABS is a recyclable material, which makes it an environmentally friendly choice in plastic manufacturing. Used ABS products can be melted and reprocessed into new components, reducing waste and promoting sustainable practices.
Energy Efficiency in Production
The ABS injection moulding process is designed to optimize material usage and minimize waste. Advanced moulding techniques reduce energy consumption, making it a more sustainable option compared to traditional plastic production methods.
Innovations in Sustainable ABS Materials
With growing environmental concerns, manufacturers are developing bio-based and recycled ABS materials to further enhance sustainability. These innovations ensure that ABS injection moulding remains a viable and eco-friendly solution for plastic production.
How to Choose the Right ABS Injection Moulding Manufacturer
Experience and Expertise
Selecting an experienced manufacturer ensures high-quality production and adherence to industry standards. A skilled team with knowledge of ABS properties and moulding techniques can significantly impact product performance and durability.
Quality Control and Certifications
A reliable manufacturer should have strict quality control measures in place. Certifications such as ISO 9001 indicate compliance with global quality standards, ensuring consistency and reliability in ABS injection moulding.
Customization and Design Support
Manufacturers that offer design assistance and customization options help businesses create unique and functional plastic components. Advanced moulding technology allows for tailored solutions that meet specific requirements.
Future Trends in ABS Injection Moulding
Advancements in Material Science
Researchers are continuously improving ABS formulations to enhance strength, heat resistance, and environmental sustainability. These innovations are expanding the potential applications of ABS injection moulding.
Automation and Smart Manufacturing
The integration of AI, robotics, and automation in ABS injection moulding is revolutionizing the industry. These technologies improve production efficiency, reduce defects, and enable more complex designs with higher precision.
Expanding Applications
As industries evolve, new applications for ABS injection moulding continue to emerge. From aerospace components to smart home devices, ABS remains a key material in the development of durable and high-performance plastic products.
Conclusion
ABS injection moulding is a leading manufacturing technique that offers strength, durability, and cost-effectiveness. Its wide-ranging applications in automotive, electronics, household appliances, and medical industries demonstrate its versatility and reliability.
With its high impact resistance, excellent surface finish, and ability to produce precise designs, ABS injection moulding remains the go-to choice for durable plastic products. As advancements in material science and sustainable manufacturing continue to develop, ABS will continue to shape the future of plastic production.