- May 7, 2025
- Posted by: feinuojixie
- Category: Injection Molding News
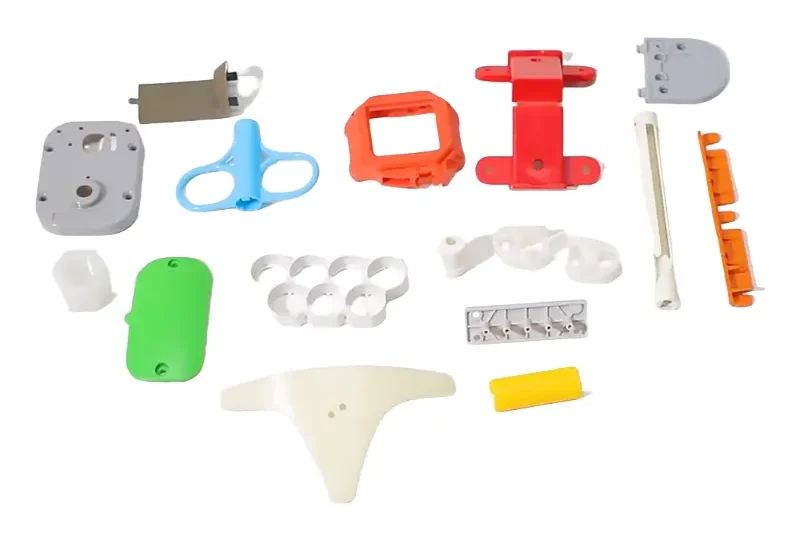
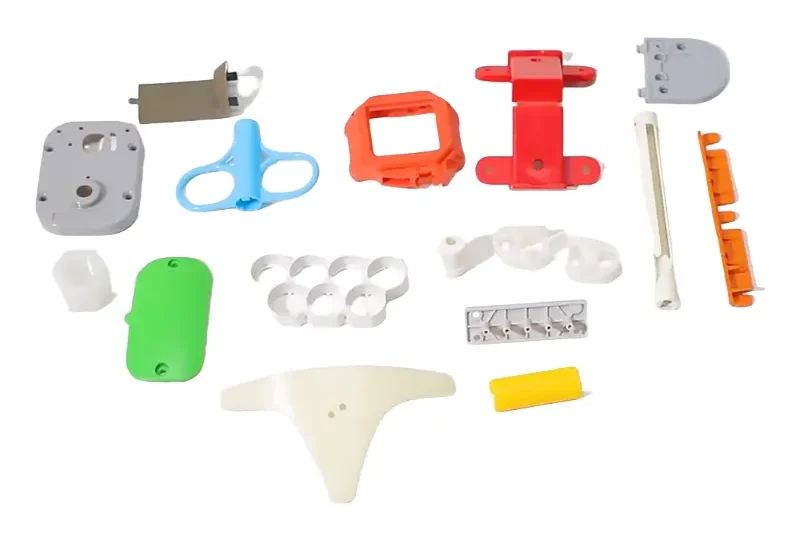
In today’s highly competitive market, the quality of every component within a product can directly influence its success or failure. Among these components, plastic injection parts often play a silent but crucial role. Whether they serve a structural, functional, or cosmetic purpose, their precision and durability directly affect product performance, longevity, and user experience. A seemingly minor flaw in a single part can cascade into product malfunctions, warranty claims, or even recalls. This is why high-quality plastic injection parts are not just a manufacturing detail—they are a strategic asset that can make or break your product. As we explore further, you’ll see how their impact extends from design tables to end-user hands, shaping everything from functionality to brand reputation.
Understanding the Function of Plastic Injection Parts in Modern Manufacturing
Plastic injection parts are used in nearly every industry—from consumer electronics and automotive to medical devices and household appliances. Their versatility stems from the ability to produce complex geometries, reduce weight, and streamline assembly processes. These parts often serve as housings, fasteners, supports, or connectors that are integral to a product’s function and integrity. Their presence may go unnoticed by the user, but their role in holding systems together or enabling interaction is undeniable. When properly engineered and manufactured, they contribute significantly to both product innovation and cost-efficiency.
What Defines High-Quality Plastic Injection Parts?
Not all plastic injection parts are created equal. High-quality parts share a set of essential attributes that ensure reliable performance. First, material selection is critical; the resin must match the environmental, mechanical, and aesthetic demands of the application. Second, dimensional accuracy ensures that the part fits and functions as intended, especially when tolerance is tight. Surface finish must also be considered—it affects not only appearance but also the part’s interaction with other components. Lastly, consistency across production runs is vital; each part should perform identically to maintain product reliability.
Common Problems Caused by Poor-Quality Plastic Injection Parts
When plastic injection parts fall short of quality standards, the consequences can be severe. Common issues include warping, shrinkage, weak joints, and premature wear—all of which can lead to product failure. For example, a weak snap-fit component might break during customer use, or an out-of-spec connector could interfere with assembly. These problems not only cause frustration for the end user but also increase warranty costs, trigger recalls, and damage brand reputation. In the worst cases, they can lead to complete product redesigns or lost contracts.
How Plastic Injection Parts Affect Your Brand and Customer Experience
Customers may never see the individual plastic injection parts within a product, but they feel their impact. A door that doesn’t close smoothly, a button that sticks, or a case that creaks—all can be traced back to poor-quality components. Over time, these small failures erode customer trust. On the other hand, when plastic injection parts are robust and well-made, they enhance the tactile and functional quality of a product, reinforcing a sense of reliability and value. This often translates into positive reviews, repeat purchases, and long-term brand loyalty.
Cost Efficiency vs. Quality: The Hidden Risks of Cutting Corners
It’s tempting to reduce costs by sourcing cheaper plastic injection parts, but this strategy often backfires. Short-term savings may result in higher long-term expenses due to increased defect rates, returns, and rework. Furthermore, poor quality can disrupt production timelines, damage relationships with distributors, and lead to lost market opportunities. Investing in quality upfront not only protects your product but also supports leaner operations and lower total cost of ownership. In manufacturing, cheap can be expensive—especially when it comes to core components like plastic injection parts.
The Role of Design and Engineering in Ensuring Quality
Quality begins at the design stage. Engineers must understand how plastic behaves under stress, temperature, and environmental exposure to create parts that meet performance requirements. This involves selecting the right resin, optimizing wall thickness, incorporating draft angles, and simulating mold flow during development. Poor design can doom a part before it ever reaches the mold. Close collaboration between design and manufacturing teams is essential to balance functionality, manufacturability, and aesthetics. By engineering quality into the part from the start, you reduce risks and enhance end-product performance.
Choosing the Right Manufacturing Partner for Plastic Injection Parts
The quality of plastic injection parts also depends heavily on the capabilities of your manufacturing partner. A reliable supplier should have modern equipment, skilled technicians, and strict quality control processes. Look for ISO certifications, robust inspection systems, and a track record of producing for similar industries. In addition, transparency, responsiveness, and a willingness to collaborate are signs of a trustworthy partner. Choosing the right manufacturer is not just a procurement decision—it’s a strategic choice that influences your product’s success and your brand’s reputation.
Case Studies: Products That Succeeded or Failed Due to Plastic Injection Parts
Consider a handheld medical device that consistently earned top ratings thanks to its ergonomic, precisely molded casing—it used high-quality plastic injection parts that held up under daily sterilization. On the flip side, a consumer electronics startup launched with fanfare but quickly ran into trouble due to parts that cracked under minimal pressure. The returns piled up, and the brand never recovered. These real-world examples show that investing in quality parts isn’t optional—it’s foundational to product success.
Invest in Quality, Reap Long-Term Benefits
In the end, plastic injection parts may be small, but their impact is massive. From performance and safety to user satisfaction and brand equity, the quality of these components resonates across every stage of your product’s lifecycle. Cutting corners might offer short-term savings, but the long-term risks far outweigh them. By investing in high-quality plastic injection parts, you set your product—and your business—on a path toward success, sustainability, and customer trust.