- April 11, 2025
- Posted by: feinuojixie
- Category: Injection Molding News
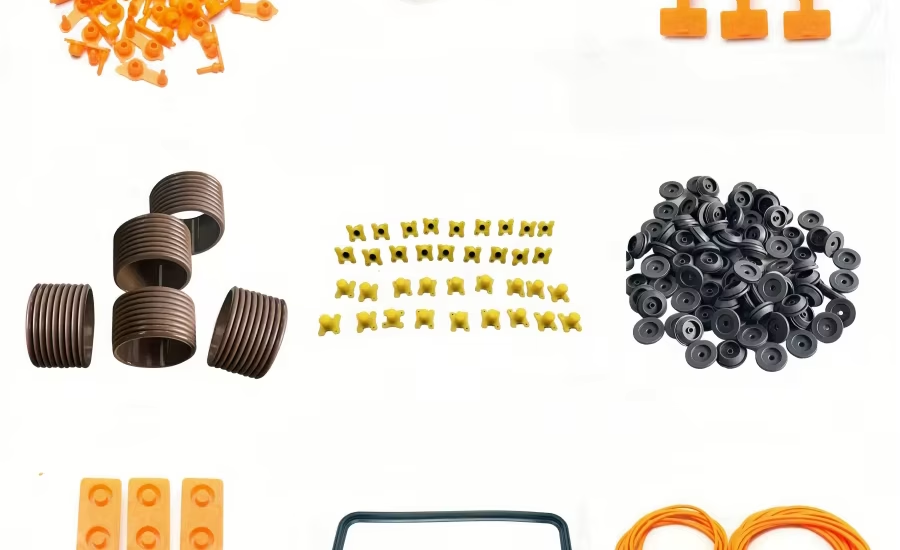
The automotive world is undergoing a transformation like never before. With rising demands for efficiency, customization, and sustainability, manufacturers are turning to smarter solutions for their vehicles. At the heart of this shift lies a powerful technology—plastic injection molding parts. Once limited to basic components, these parts have now taken center stage in everything from dashboards and bumpers to under-the-hood systems. Their growing dominance isn’t just about cost savings—it’s a result of their versatility, strength, and ability to meet modern automotive standards. As carmakers race to build lighter, safer, and more eco-friendly vehicles, plastic injection molding parts are proving to be a game-changing solution.
Precision Meets Performance: What Makes Plastic Injection Molding Parts Ideal for Cars
When it comes to automotive manufacturing, precision is non-negotiable. Every component must fit perfectly, function flawlessly, and withstand a variety of conditions. This is where plastic injection molding parts shine. The process allows manufacturers to create components with incredibly tight tolerances and consistent quality. Whether it’s a small clip or a dashboard panel, the precision of injection molding ensures that each part meets exact specifications. This level of detail is crucial for maintaining performance, safety, and reliability across all vehicle types.
Lightweight and Fuel Efficiency: The Environmental Edge
One of the most important benefits of using plastic injection molding parts is their contribution to reducing overall vehicle weight. Lightweight materials are essential in improving fuel efficiency and cutting emissions. Replacing traditional metal components with molded plastic alternatives can significantly lower a vehicle’s mass without sacrificing strength or durability. This not only enhances mileage but also helps manufacturers meet increasingly strict environmental regulations. As the push for greener transportation intensifies, lightweight plastic injection molding parts are becoming a cornerstone of sustainable automotive design.
Design Flexibility and Customization for Every Model
No two vehicle models are exactly the same—and thanks to plastic injection molding, they don’t have to be. This manufacturing method offers unmatched flexibility when it comes to part design and customization. Engineers can easily adapt or tweak molds to produce parts that are unique to a specific car model or brand aesthetic. From complex geometries to textured finishes, plastic injection molding parts can be tailored to deliver both function and visual appeal. This level of design freedom allows manufacturers to innovate continuously and meet diverse consumer preferences without compromising efficiency.
Cost-Effective Manufacturing at Scale
Producing millions of parts for global vehicle lines requires a manufacturing method that’s both fast and economical. Plastic injection molding parts fit this requirement perfectly. Once the initial mold is created, the production process is highly efficient, enabling large volumes of parts to be produced at low per-unit costs. The process also minimizes material waste, making it not only cost-effective but also environmentally friendly. For automakers looking to balance quality with profitability, injection molding offers an ideal solution that scales effortlessly with demand.
Durability and Strength: Beyond the Plastic Stereotype
There’s a common misconception that plastic equals flimsy—but modern engineering has shattered that stereotype. Today’s plastic injection molding parts are made from advanced polymers designed to endure high stress, heat, and chemical exposure. These parts are built to last, even in the most demanding automotive environments such as engine compartments or suspension systems. Some plastics can even outperform metal in terms of corrosion resistance and fatigue life. This makes them not only a viable replacement for metal components but often a superior one in terms of longevity and resilience.
Enhanced Safety and Structural Integrity
Safety is a top priority in automotive design, and plastic injection molding parts contribute more than many realize. Through smart design and material selection, these parts can absorb impact, resist deformation, and enhance overall vehicle integrity. Whether it’s interior components designed to reduce injury during a crash or structural elements that provide rigidity, molded plastic parts play a critical role in protecting occupants. In fact, many components are engineered to meet or exceed regulatory safety standards, proving that safety and plastic can go hand in hand.
Integration with Smart and Electric Vehicle Technologies
As the automotive world moves toward smarter, more connected vehicles, plastic injection molding parts are evolving to keep pace. These parts are now designed to integrate seamlessly with sensors, wiring harnesses, and electronic modules essential for modern vehicle systems. In electric cars, for example, molded plastic components help insulate electrical systems, house battery packs, and even support advanced driver-assistance technologies. Their non-conductive nature, combined with lightweight and customizable design, makes them ideal for the demands of next-generation vehicle platforms.
Sustainability and Recycling: A Cleaner Future
In addition to their performance benefits, plastic injection molding parts support sustainability in several ways. Many automotive plastics are recyclable, and advances in biodegradable and bio-based resins are opening new doors for eco-friendly production. The molding process itself is efficient, producing minimal waste and often using recycled material in the manufacturing cycle. This aligns with the industry’s push toward circular economies and carbon neutrality. As sustainability becomes a top priority, injection molding is positioned as a clean, responsible manufacturing solution for the future.
Future Trends: What’s Next for Plastic Injection Molding Parts in Automotive Design
The future of plastic injection molding parts in automotive design looks bright and bold. Innovations such as AI-assisted design, smart tooling, and hybrid material composites are redefining what’s possible. We can expect to see even lighter, stronger, and more multifunctional parts in upcoming vehicle models. Additionally, as autonomous and electric vehicles become more prevalent, the demand for precisely engineered plastic components will only grow. The industry is heading toward a new era—one where plastic injection molding doesn’t just support car design but drives it forward.
Driving Innovation with Plastic Injection Molding Parts
From boosting fuel efficiency and reducing emissions to enabling sleek designs and cutting-edge technologies, plastic injection molding parts are revolutionizing the way cars are built. Their versatility, strength, and cost-effectiveness make them an indispensable part of the modern automotive world. As the industry continues to evolve, these parts are no longer just a supporting player—they’re at the center of innovation. For automakers aiming to stay ahead in performance, safety, and sustainability, embracing plastic injection molding parts isn’t just smart—it’s essential.