- February 28, 2025
- Posted by: feinuojixie
- Category: Injection Molding News
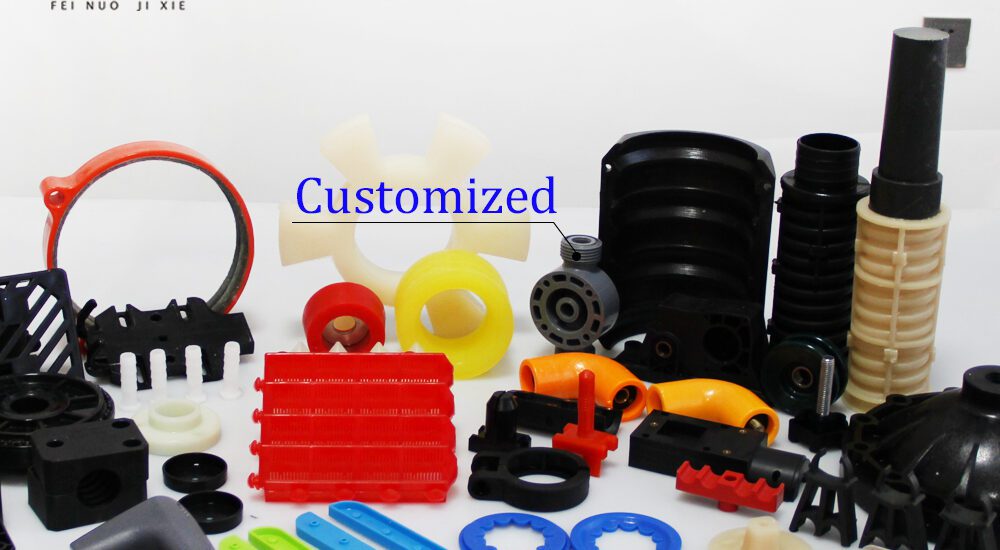
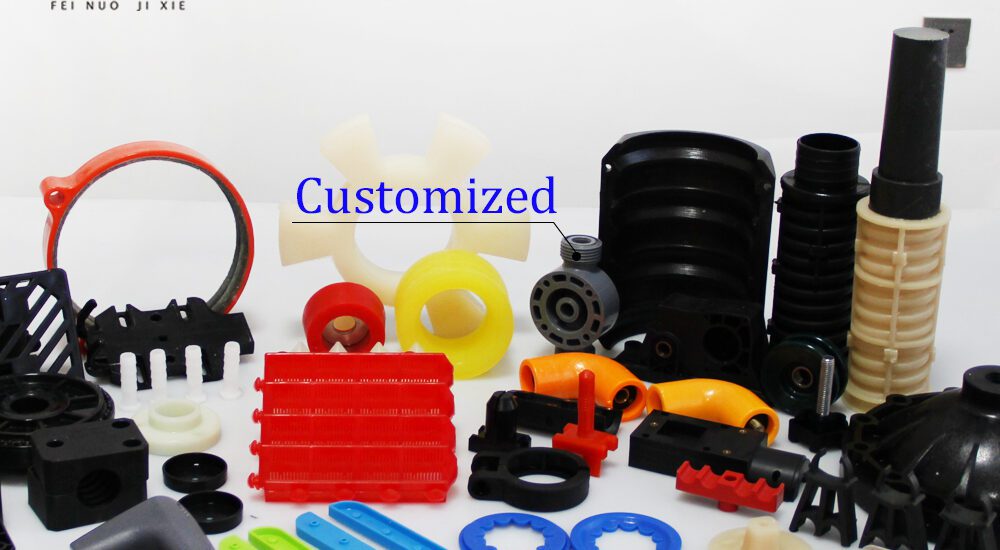
In the world of manufacturing, few processes have had as transformative an impact as injection molding. While it may not always be in the spotlight, the use of injection molded part is revolutionizing industries by providing unmatched precision, speed, and cost-efficiency. From automotive parts to consumer electronics, injection molded part has become a cornerstone of modern manufacturing. But what exactly makes this process so essential? And why is it shaping the future of production on a global scale? In this article, we’ll explore how injection molded part is not only changing how products are made but also enhancing the way industries operate across the globe.
What Is an Injection Molded Part? Defining the Basics
Injection molding is a manufacturing process used to produce parts by injecting molten material into a mold. The material is then cooled and solidified to form the final product. This process is widely used because of its ability to create complex shapes with high precision at a fast rate, making it ideal for large-scale production runs.
An injection molded part can be made from a variety of materials, including plastics, metals, and even certain rubber types. These materials are selected based on the desired properties of the finished product, such as strength, flexibility, and durability.
The injection molding process begins by melting the raw material, which is then injected into a carefully designed mold under high pressure. Once the material fills the mold, it is allowed to cool and harden, after which the part is ejected. The precision involved in this process ensures that every injection molded part is consistent, reducing waste and rework.
Advantages of Injection Molded Part in Industrial Production
One of the primary reasons why injection molded part is so widely used in manufacturing is its numerous advantages:
High Precision and Quality Control
Injection molded parts are known for their high level of accuracy. The process allows manufacturers to create parts with intricate details and consistent dimensions, ensuring high-quality standards are met. This is particularly crucial in industries like electronics, automotive, and medical devices, where even the smallest flaw can have significant consequences.
Enhanced Production Speed and Efficiency
Injection molding is incredibly fast. Once the mold is created, parts can be produced in seconds, significantly reducing production times. This speed enables manufacturers to produce large quantities of parts in a short period, meeting the high demand of industries worldwide.
Cost-Effectiveness and Scalability
Because injection molding is a high-efficiency process, it allows for mass production of parts at a relatively low cost. The ability to produce large quantities of identical parts makes it an ideal solution for industries that require scale, such as automotive and consumer goods. The cost per part decreases as production volumes increase, making it a highly scalable manufacturing option.
How Injection Molded Part Is Transforming Automotive Manufacturing
The automotive industry has seen a dramatic shift in manufacturing techniques in recent years, and injection molded parts are a key contributor to this transformation. From reducing vehicle weight to improving fuel efficiency, the automotive sector is benefiting immensely from this technology.
Injection molded parts are commonly used in a variety of automotive applications, from dashboards and door panels to engine components. The ability to create lightweight yet durable parts helps manufacturers meet regulatory requirements for fuel efficiency while maintaining safety and performance standards. Injection molded parts also allow for more complex designs, enabling car manufacturers to produce parts that are both functional and aesthetically pleasing.
The Influence of Injection Molded Part on Consumer Electronics
In the realm of consumer electronics, injection molded part plays an essential role in the design and production of durable, sleek, and reliable products. Whether it’s a smartphone, tablet, or television, manufacturers rely on injection molded parts to create the intricate, high-quality housings and components that make these devices so appealing to consumers.
One of the biggest advantages of using injection molded parts in electronics is the flexibility it provides in terms of design. Manufacturers can produce complex shapes that are both lightweight and durable, helping to reduce the overall weight of devices while enhancing their aesthetic appeal. Additionally, the high precision of injection molding ensures that parts fit together seamlessly, improving the overall functionality and longevity of the product.
Injection Molded Part in Medical Device Manufacturing: Improving Safety and Efficiency
The medical industry is another sector where the use of injection molded parts is having a profound impact. Medical devices require a high level of precision and reliability, and injection molding meets these requirements with ease.
Injection molded parts are used in a variety of medical devices, from surgical instruments to drug delivery systems. These parts are often required to be sterilized, and injection molding allows for the creation of parts that are both easy to sterilize and durable enough to withstand repeated use. Furthermore, the high precision of injection molding ensures that medical devices perform consistently, which is critical in ensuring patient safety.
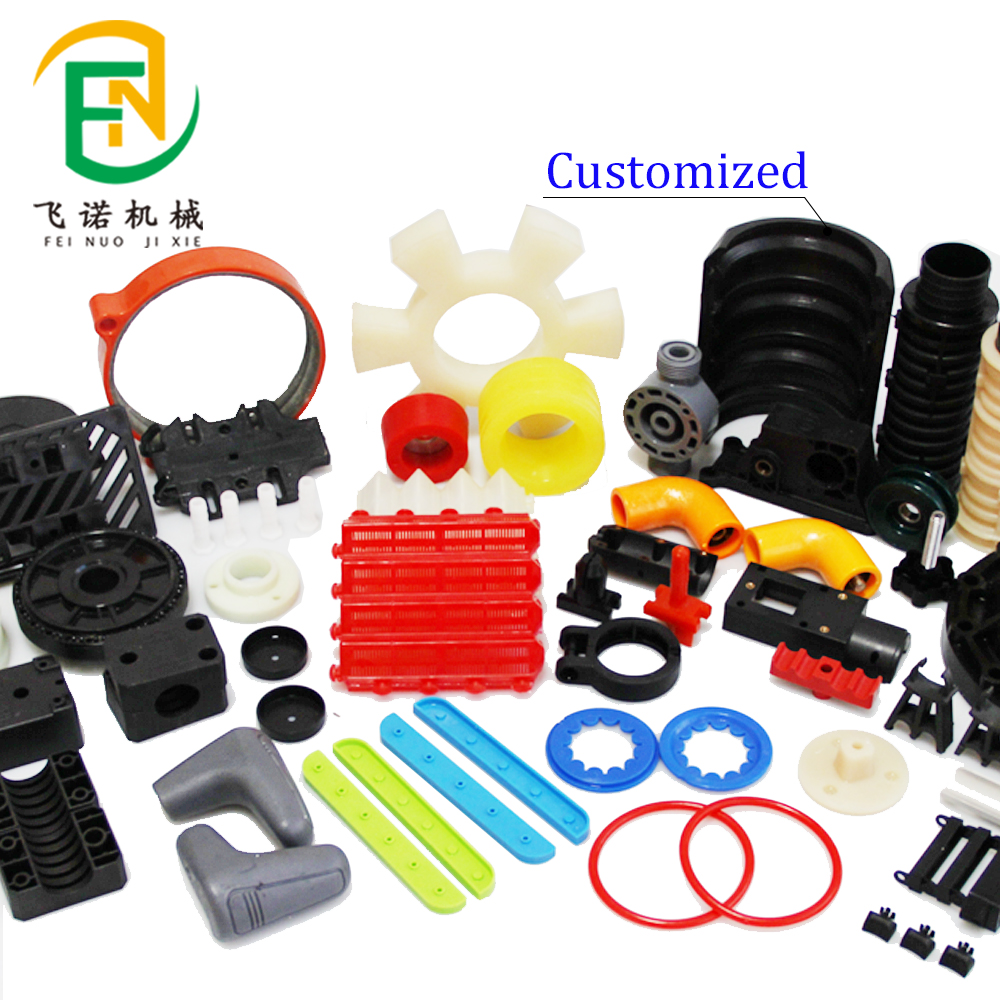
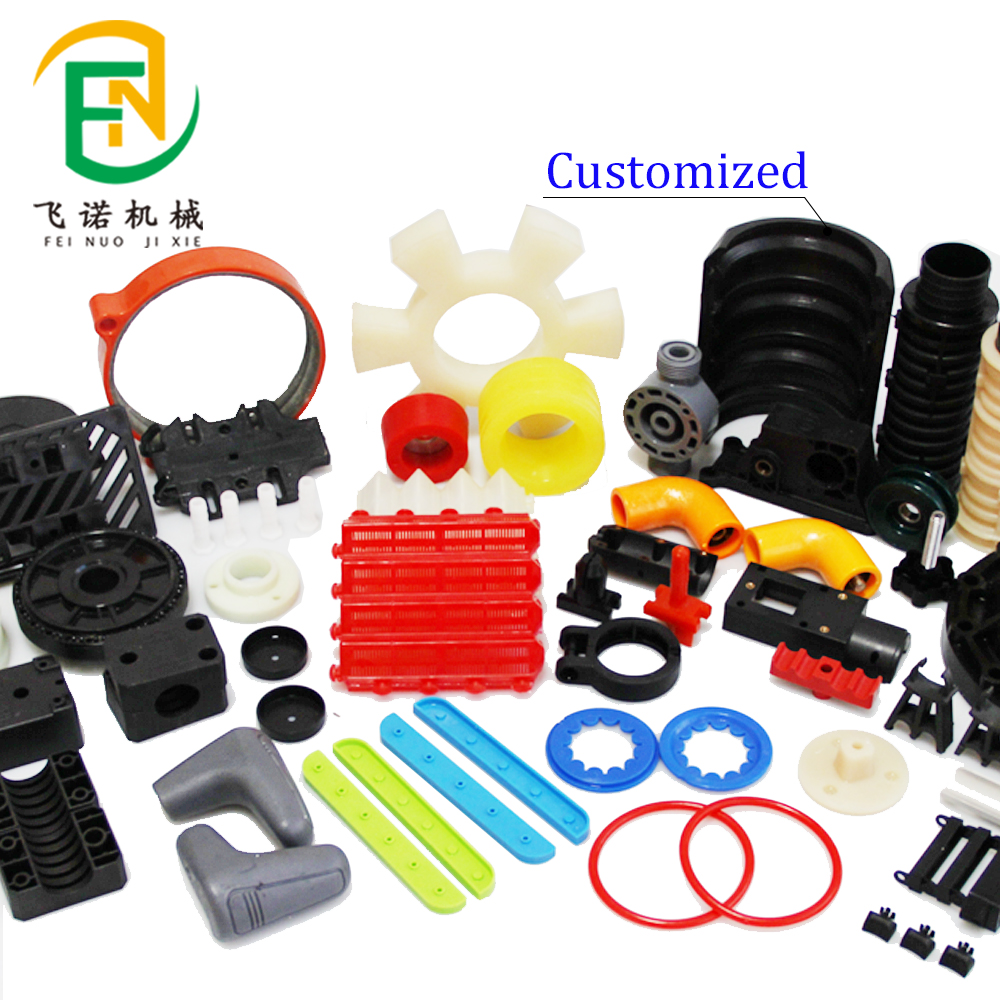
Sustainability and Injection Molded Part: A Greener Future for Manufacturing
As the world becomes increasingly focused on sustainability, industries are looking for ways to reduce their environmental impact. Injection molded part is no exception, with manufacturers working to make the process more eco-friendly.
One of the key benefits of injection molding is the ability to use recycled materials in production. This reduces waste and helps conserve natural resources. Additionally, ongoing innovations in materials are making injection molded parts even more sustainable, with new materials that are biodegradable or made from renewable resources.
The Future of Injection Molded Part: Trends and Innovations to Watch
As technology continues to advance, so too does the injection molding process. In the coming years, we can expect to see further innovations in both materials and manufacturing techniques. One of the most exciting developments is the integration of 3D printing technologies with injection molding, allowing for even more complex designs and reduced production times.
In addition, the development of new, more sustainable materials will likely play a significant role in the future of injection molded parts. Manufacturers are exploring new ways to reduce the environmental impact of their products, making the injection molding process more eco-friendly than ever before.
Conclusion: Why Injection Molded Part Is Here to Stay
Injection molded part has revolutionized manufacturing across a wide range of industries, providing unparalleled precision, speed, and cost-efficiency. From automotive to electronics to medical devices, injection molding has become a crucial part of modern production processes. As technology continues to evolve, we can expect to see even more innovations that will further cement injection molded part’s place in the manufacturing world. With its versatility, scalability, and sustainability, injection molded part is truly here to stay.