- April 28, 2025
- Posted by: feinuojixie
- Category: Injection Molding News
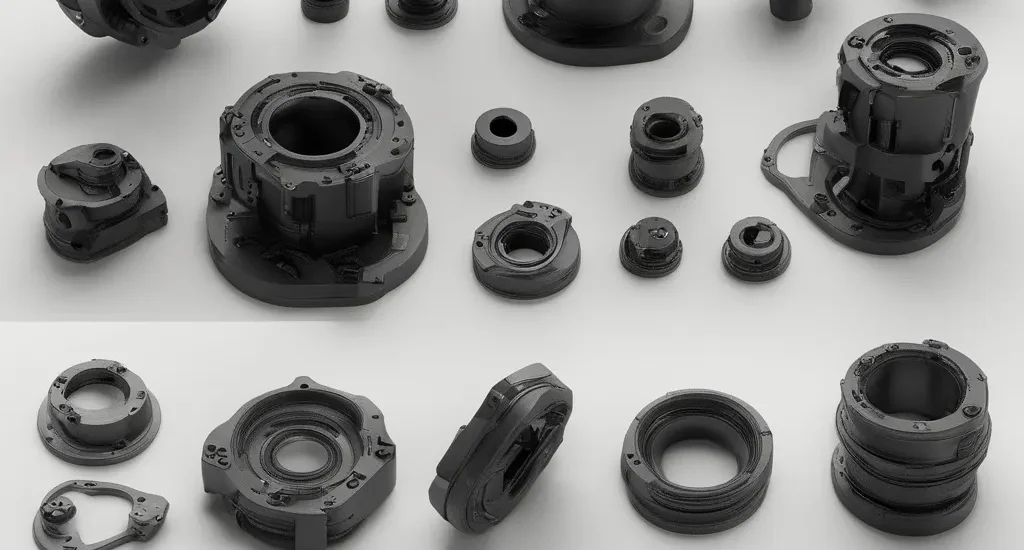
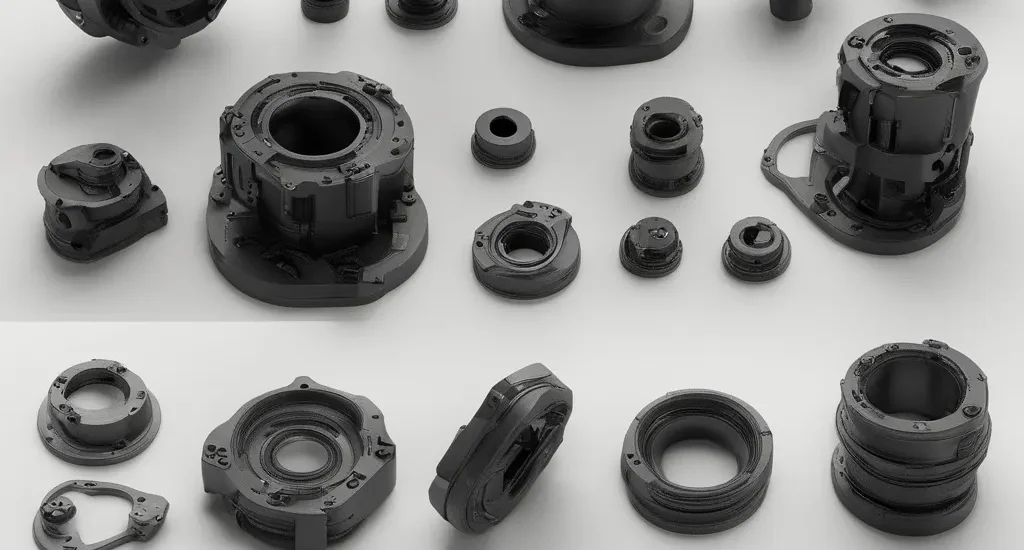
The automotive industry has witnessed dramatic shifts in how vehicle parts are manufactured. From traditional handcrafting and metal forging to modern automated assembly lines, each advancement has pushed the boundaries of what vehicles can achieve. Today, injection molding automotive parts stands at the forefront of this evolution, offering a game-changing approach that combines precision, speed, and cost-effectiveness. As manufacturers seek smarter, lighter, and more sustainable solutions, injection molding is becoming the natural choice.
Understanding Injection Molding Automotive Parts Technology
Injection molding is a manufacturing process where molten material, typically thermoplastic, is injected into a mold cavity to form a specific part. When applied to automotive parts, this technology allows for the rapid creation of complex shapes with high precision and consistency. From dashboard components to under-the-hood applications, injection molding automotive parts covers a vast range of needs, supporting everything from aesthetic design to structural performance requirements.
The Key Advantages of Injection Molding Automotive Parts
One of the standout advantages of injection molding automotive parts is the unparalleled efficiency it brings to production. Unlike traditional methods such as metal stamping or machining, injection molding enables the mass production of intricate components with minimal waste. Parts created through injection molding exhibit excellent dimensional accuracy, high repeatability, and a superior surface finish. Additionally, the cycle times are remarkably short, enabling faster time-to-market for new vehicle models.
Material Innovations Driving Injection Molding Automotive Parts
The materials used in injection molding automotive parts have evolved significantly, giving manufacturers greater flexibility and performance. Advanced polymers and composites, such as reinforced polypropylene and high-heat resistant nylon, are commonly utilized. These materials not only meet stringent mechanical and thermal requirements but also offer benefits like corrosion resistance and reduced weight. The continuous development of smart materials further expands the possibilities for what injection molding can achieve in vehicle production.
Injection Molding Automotive Parts and the Push for Lightweight Vehicles
Automakers are under increasing pressure to design vehicles that are lighter without compromising safety or durability. Injection molding automotive parts plays a crucial role in this effort by enabling the use of lightweight plastic and composite materials instead of traditional metals. Components like bumper beams, seat structures, and even engine parts are now commonly produced using injection molding, contributing to significant weight reductions that improve fuel economy and extend electric vehicle range.
Customization and Design Freedom with Injection Molding Automotive Parts
Design flexibility is another major reason injection molding automotive parts are leading the future. Engineers can integrate complex geometries, textures, and functional features directly into the part during the molding process. This capability allows for innovative designs that improve aesthetics, enhance ergonomics, and consolidate multiple parts into a single, more efficient assembly. With injection molding, manufacturers can easily tailor parts to meet specific performance or branding needs without excessive cost increases.
Cost Efficiency and Scalability of Injection Molding Automotive Parts
Cost considerations are paramount in automotive manufacturing, where profit margins can be razor-thin. Injection molding automotive parts offer a distinct advantage by lowering per-unit costs once the initial investment in molds is made. The process is highly scalable, making it ideal for both low-volume specialty vehicles and high-volume mass-market production. Additionally, automation in injection molding reduces labor costs and minimizes the risk of human error, resulting in consistent quality across large production runs.
Sustainability Benefits of Injection Molding Automotive Parts
Sustainability is becoming a non-negotiable priority for the automotive industry. Injection molding automotive parts contribute to greener manufacturing in several ways. Many materials used in the process are recyclable, and manufacturers can reclaim and reuse scrap generated during production. Moreover, the precision of injection molding minimizes excess material usage and energy consumption compared to more traditional fabrication methods, aligning with global efforts to reduce carbon footprints.
Challenges and Innovations in Injection Molding Automotive Parts
Despite its many advantages, injection molding automotive parts does present challenges. High upfront costs for tooling and molds can be a barrier, especially for small manufacturers. Additionally, the complexity of mold design demands specialized expertise. However, ongoing innovations are addressing these issues. New techniques such as rapid tooling, 3D-printed molds, and AI-driven design optimization are making injection molding more accessible and flexible than ever before.
The Future Outlook: How Injection Molding Automotive Parts Will Redefine the Industry
Looking ahead, the role of injection molding automotive parts is set to expand dramatically. With the rise of electric vehicles, autonomous driving technologies, and the demand for smarter, more integrated vehicle systems, injection molding offers the adaptability needed to meet these evolving requirements. Innovations like overmolding electronics directly into components and using bioplastics will further enhance the role of injection molding in future vehicle design and production.
Embracing the Shift Toward Injection Molding Automotive Parts
Injection molding automotive parts is not just a trend; it is a transformative movement shaping the future of vehicle production. With its blend of efficiency, innovation, and sustainability, this manufacturing method provides automotive companies with a powerful tool to stay competitive in a rapidly changing industry. Those who embrace injection molding today will be better positioned to lead tomorrow’s automotive revolution.