- April 16, 2025
- Posted by: feinuojixie
- Category: Injection Molding News
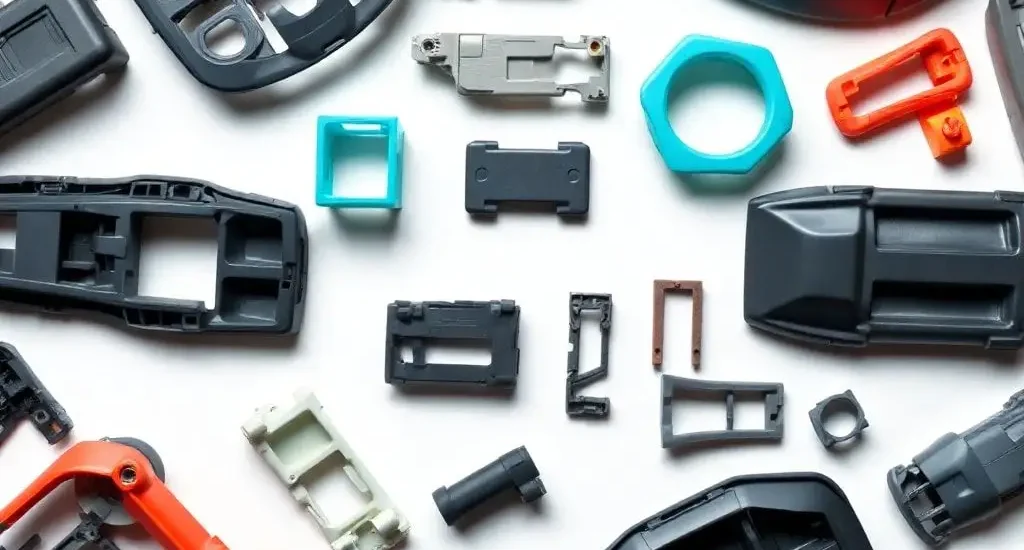
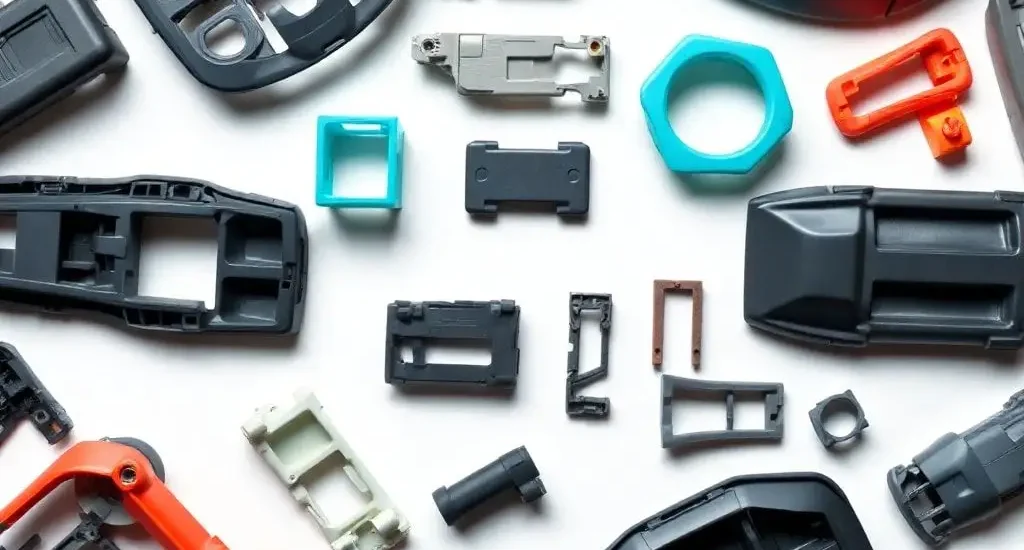
Look around you—your phone case, the dashboard of your car, the packaging of your last online order. Chances are, each of these contains at least one injection molding part. Despite being largely invisible to everyday consumers, this method of production has become the backbone of modern manufacturing. Its ability to deliver precise, reliable, and scalable components has transformed how companies across countless industries build their products. From medical devices to electronics, injection molding part is a quiet hero driving innovation, cost-efficiency, and industrial evolution forward. In this article, we explore why injection molding part holds such an indispensable position in today’s production landscape.
The Basics: What Are Injection Molding Parts?
At its core, an injection molding part is a component created by injecting molten material—typically a type of plastic—into a pre-designed mold. Once cooled, the material hardens into the desired shape with exceptional precision. This method has become a staple of modern manufacturing thanks to its speed, accuracy, and ability to replicate intricate designs consistently. Whether it’s a simple cap or a highly technical medical device housing, injection molding part is the reliable foundation behind many modern products. Understanding this basic process sheds light on why it’s so dominant across industrial sectors.
Versatility Across Industries: Where Injection Molding Parts Dominate
Injection molding part has found its place in nearly every major industry. In automotive manufacturing, it’s used for dashboards, bumpers, and under-the-hood components. In the medical field, it forms sterile housings for devices and single-use components. Consumer electronics rely on it for cases, connectors, and internal structures. Even the packaging industry depends on injection molding part to produce containers, caps, and closures with speed and uniformity. Its adaptability to various applications and requirements makes it the go-to choice for both high-tech and everyday products.
Cost-Effective Mass Production: Efficiency Meets Affordability
One of the most compelling reasons manufacturers opt for injection molding part is its unparalleled efficiency in mass production. After the initial mold is created—a cost that can be significant—the per-unit cost of each part drops dramatically, especially in large volumes. This makes it ideal for businesses aiming to produce high quantities of consistent, high-quality components. The speed of the injection molding cycle also means manufacturers can meet tight deadlines without sacrificing quality, making it a vital process in fast-paced industries.
Precision and Consistency: The Gold Standard of Quality
In production, consistency isn’t just a goal—it’s a requirement. Injection molding part excels at delivering exact duplicates of a design, maintaining tight tolerances and clean finishes with every cycle. This level of precision is especially important in industries like aerospace and healthcare, where even a slight variation can lead to performance failure or safety issues. Through automation and precise mold engineering, manufacturers achieve repeatable accuracy that rivals any other method of production.
Material Flexibility: The Power of Choice
Injection molding part offers extraordinary flexibility in terms of materials. Manufacturers can choose from a wide range of thermoplastics, including ABS, polycarbonate, nylon, and more. Each material brings unique properties to the table, such as impact resistance, chemical durability, or heat tolerance. This selection allows engineers to match the material properties precisely to the function of the part. Furthermore, additives and colorants can be introduced during the process, enabling enhanced performance and custom aesthetics.
Sustainability Benefits: A Greener Path to Production
As environmental concerns grow, injection molding part is gaining recognition for its sustainability potential. The process generates minimal waste, as excess material can often be recycled and reused. Many modern facilities also incorporate energy-efficient equipment and eco-friendly practices. Additionally, the durability of injection molded components means they often have longer lifespans, reducing the need for frequent replacements. When paired with recyclable materials, injection molding part supports a circular economy approach in industrial production.
Advancements in Injection Molding: Smart and Future-Ready
Technology never stands still, and neither does injection molding. Recent innovations such as micro molding enable the production of ultra-small parts with high detail—perfect for medical and electronic devices. Automation has streamlined the process even further, increasing output while reducing labor costs. Smart molds with sensors now provide real-time data during production, allowing for immediate quality control adjustments. These advancements ensure that injection molding part remains at the cutting edge of modern manufacturing.
Design Freedom: Unlocking Creative Engineering Possibilities
Unlike many traditional manufacturing techniques, injection molding part supports complex geometries and intricate designs without a significant increase in production cost. Engineers can incorporate features like undercuts, threads, and snap-fits directly into the mold, allowing for parts that are both functional and aesthetically refined. This freedom encourages innovation, enabling designers to push the boundaries of what’s possible while still maintaining cost and quality control.
The Silent Pillar of Industrial Evolution
Behind every sleek gadget, sturdy vehicle, and reliable medical device, there’s often an injection molding part doing the heavy lifting—quietly, precisely, and efficiently. Its unmatched combination of scalability, precision, material flexibility, and cost-effectiveness has solidified its place as the backbone of modern production. As technology advances and industries evolve, injection molding part continues to adapt and lead, proving that sometimes the most vital forces in progress are the ones we don’t always see.