- April 21, 2025
- Posted by: feinuojixie
- Category: Injection Molding News
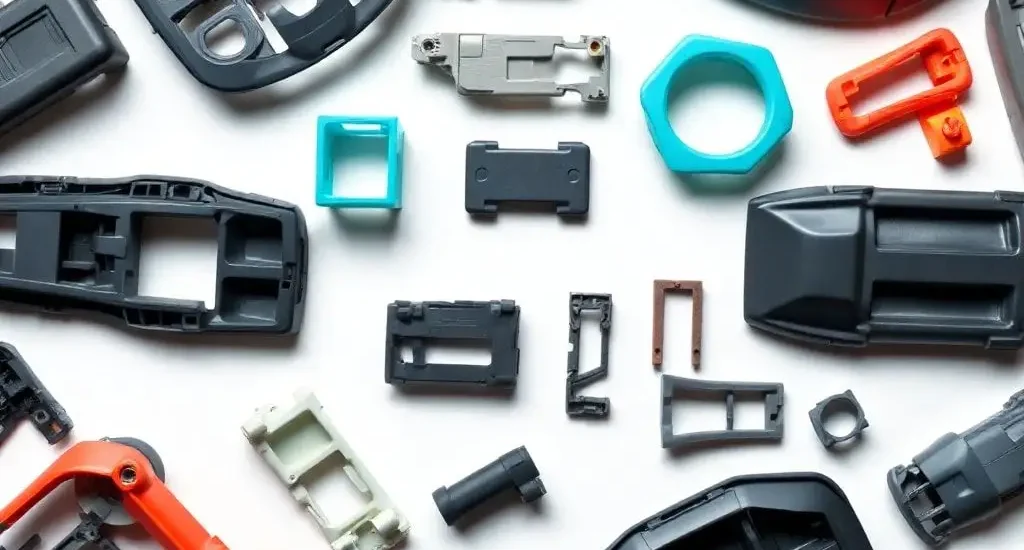
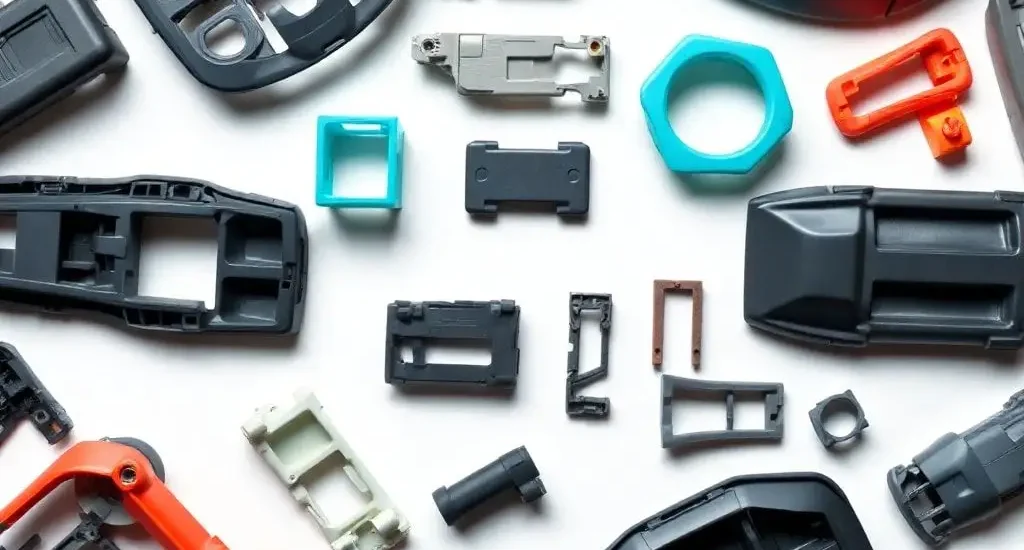
In today’s manufacturing world, injection moulding has become the backbone of plastic part production. From the tiniest medical device component to robust automotive housings, this technique enables the mass production of high-quality plastic part with remarkable precision and consistency. The reason behind its wide adoption is simple—it delivers speed, scalability, and cost-efficiency without sacrificing detail or durability. Whether you are designing a product from scratch or scaling up an existing design, understanding why injection moulding is considered the gold standard is essential. This article explores every angle of this versatile process, helping you understand what makes injection moulding the industry’s preferred solution for plastic part manufacturing.
Understanding Injection Moulding: The Foundation of Plastic Part Manufacturing
At its core, injection moulding is a manufacturing process that involves injecting molten plastic into a precision-machined mould. Once the material cools and hardens, it takes the shape of the mould cavity, forming a solid plastic part. This technique has been a cornerstone of industrial production since the mid-20th century, evolving with advances in materials science and automation. Today, it supports everything from mass-market consumer goods to mission-critical aerospace components. The process is highly repeatable and produces minimal waste, making it an efficient and sustainable option for manufacturers worldwide.
Unmatched Precision and Consistency in Plastic Part Quality
One of the most compelling advantages of injection moulding is its ability to produce plastic part with incredible accuracy. Modern moulds are engineered with tight tolerances, and the repeatability of the process ensures that each part is virtually identical to the next. This consistency is vital in sectors like medical and automotive manufacturing, where even slight deviations can result in product failure. The ability to integrate advanced quality control systems, such as in-mould sensors and automated inspection, further reinforces the reliability of injection moulding for delivering high-quality plastic part every time.
Efficiency at Scale: How Injection Moulding Transforms Production Economics
Injection moulding truly shines when it comes to high-volume production. While the initial investment in tooling and mould design can be substantial, the cost per plastic part drops dramatically with scale. Once the mould is ready, thousands—or even millions—of parts can be produced with minimal human intervention. Short cycle times, high throughput, and low scrap rates contribute to its reputation as a cost-effective solution for mass manufacturing. For businesses aiming to scale rapidly or maintain consistent inventory, injection moulding offers a powerful economic advantage.
Material Versatility: Tailoring Plastic Part to Specific Applications
Another reason injection moulding dominates plastic manufacturing is the vast selection of compatible materials. From standard thermoplastics like ABS and polypropylene to high-performance engineering polymers like PEEK and polycarbonate, manufacturers can choose materials that best meet the mechanical, thermal, and chemical requirements of their application. Additives can be introduced to enhance UV resistance, flame retardancy, flexibility, or color. This flexibility in material selection ensures that every plastic part is optimized for its intended use, whether it needs to be soft and pliable or tough and rigid.
Complex Geometries Made Simple with Injection Moulding
Designers and engineers appreciate injection moulding for its ability to create intricate and complex shapes that would be difficult or impossible to achieve through other manufacturing processes. Thanks to advanced mould-making techniques, features such as undercuts, threaded inserts, thin walls, and living hinges can be incorporated directly into the design. With the right tooling, these complex geometries are formed in a single cycle, eliminating the need for secondary operations and reducing lead times. This capability expands the design possibilities for every plastic part, making innovation more accessible.
Speed and Automation: Meeting Market Demands with Agility
In fast-moving industries, the ability to respond to market demands quickly is crucial. Injection moulding supports rapid production through short cycle times—often measured in seconds. When integrated with automated systems such as robotic arms, conveyors, and vision inspection tools, the process becomes highly autonomous. This high level of automation not only accelerates production but also reduces labor costs and human error. As a result, manufacturers can meet tight deadlines while maintaining the quality of each plastic part produced.
Design for Manufacturability: Optimizing Every Plastic Part
Designing a plastic part for injection moulding is both an art and a science. Engineers must consider factors such as wall thickness, draft angles, gate placement, and cooling time to ensure efficient production and optimal performance. By embracing “design for manufacturability” (DFM) principles early in the design phase, companies can reduce defects, shorten development cycles, and lower costs. The DFM approach also facilitates better collaboration between design and manufacturing teams, leading to smarter products and fewer production issues down the line.
Sustainability and Waste Reduction in Injection Moulding
As sustainability becomes a growing concern, injection moulding continues to evolve to meet environmental goals. Many modern systems are equipped with energy-efficient servo motors and closed-loop control systems that minimize energy consumption. Material waste is also significantly reduced through recycling scrap and regrinding defective parts for reuse. Moreover, biodegradable and recycled plastics are increasingly being used, helping companies align with eco-conscious initiatives. These green practices make injection moulding a viable and responsible choice for sustainable plastic part production.
Challenges and Limitations: What to Consider Before Choosing Injection Moulding
Despite its many strengths, injection moulding is not always the right fit for every project. The initial cost of mould fabrication can be high, making it less suitable for low-volume or prototype production. Additionally, design changes after mould creation can be expensive and time-consuming. Alternative methods like 3D printing or CNC machining may be better options for rapid prototyping or custom parts. Still, for most high-volume applications, the benefits of injection moulding far outweigh its limitations.
Why Industries Choose Injection Moulding for Every Plastic Part
From electronics and consumer goods to healthcare and aerospace, industries consistently turn to injection moulding as their preferred method for plastic part production. Its unmatched precision, speed, and cost-efficiency make it ideal for meeting modern manufacturing demands. The process also adapts well to technological advancements, ensuring its relevance in a rapidly evolving market. When businesses need reliability at scale, injection moulding is the logical—and often unbeatable—choice.
The Future of Injection Moulding in Plastic Part Production
As new technologies emerge, injection moulding continues to adapt and thrive. Innovations like micro moulding, real-time AI-driven process monitoring, and the integration of smart manufacturing tools are pushing the boundaries of what’s possible. The increasing availability of eco-friendly materials and closed-loop systems also ensures that sustainability remains a core focus. Looking ahead, injection moulding is not only poised to remain the gold standard for plastic part production—it is set to become even more powerful, intelligent, and sustainable.