- March 5, 2025
- Posted by: feinuojixie
- Category: Injection Molding News
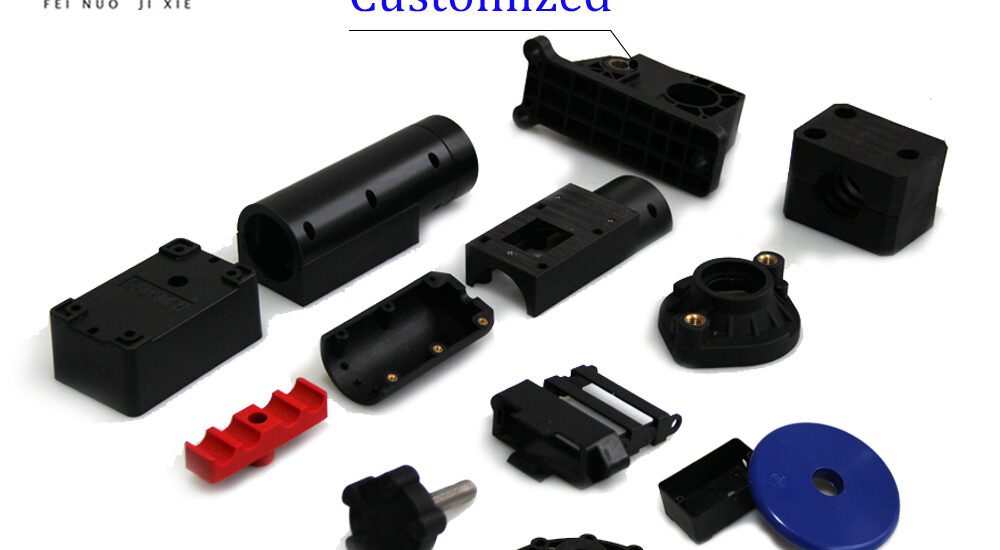
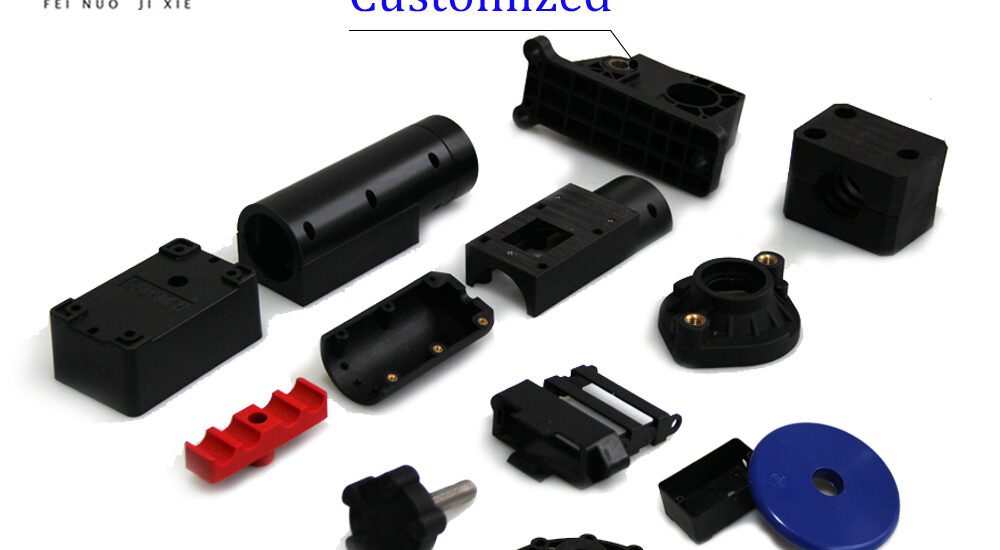
Injection moulding plastic part has rapidly become one of the most critical technologies in precision engineering. As industries move towards greater precision in manufacturing, injection moulding is playing a central role in meeting these high standards. Precision engineering demands accurate, repeatable, and reliable parts, and injection moulding plastic part delivers these qualities at scale. The process enables manufacturers to create complex shapes and parts with remarkable accuracy, making it indispensable for a wide range of applications, from automotive to medical fields.
In this article, we will explore the significance of injection moulding plastic part in precision engineering, why it has become the go-to method for producing high-quality components, and what its future holds as technology continues to advance.
The Mechanics Behind Injection Moulding Plastic Part: A Game-Changer in Manufacturing
Injection moulding plastic part is a highly sophisticated process that involves injecting molten plastic material into a precisely shaped mould. Once the material cools and solidifies, the mould opens to reveal the finished part. This process is incredibly efficient, allowing manufacturers to produce thousands of identical plastic parts with high precision.
The primary materials used in injection moulding plastic part include thermoplastics such as ABS, polycarbonate, and polyethylene, each offering different properties suitable for specific applications. These materials provide the flexibility to create parts that are durable, lightweight, and capable of withstanding varying environmental conditions. The advanced machinery and techniques used in injection moulding ensure that the final products meet exact specifications, making it the ideal method for precision engineering.
Why Injection Moulding Plastic Part Is Ideal for Precision Engineering Applications
Injection moulding plastic part excels in applications where precision is paramount. One of the key benefits of this process is its ability to produce parts with tight tolerances, which is essential for industries that require high-quality, accurate components. This level of precision is achieved through advanced mould design, tight control over injection speeds, and precise temperature management during the cooling phase.
Additionally, the ability to create complex shapes and intricate designs with ease sets injection moulding apart from other manufacturing methods. Whether it’s for micro-components or larger, more intricate parts, injection moulding offers unmatched versatility, making it ideal for industries like automotive, electronics, and medical devices where precision is critical.
Advantages of Using Injection Moulding Plastic Part in Modern Manufacturing
Injection moulding plastic part offers a host of advantages that make it an attractive choice for precision engineering. One of the most significant benefits is cost-efficiency. While the initial tooling costs can be high, the per-unit cost decreases significantly as production volume increases. This makes injection moulding a cost-effective solution for both small and large production runs.
Another key advantage is speed. The injection moulding process is incredibly fast, allowing manufacturers to produce large quantities of parts in a short amount of time. This rapid production capability is crucial for industries that require quick turnaround times and large volumes of parts.
Furthermore, injection moulding ensures consistency and scalability. Once the mould is designed, the process can be repeated thousands of times, producing identical parts with consistent quality. This scalability is essential for businesses looking to expand their production without sacrificing quality or precision.
The Role of Advanced Technology in Enhancing Injection Moulding Plastic Part Precision
As technology continues to evolve, injection moulding plastic part has also benefited from cutting-edge innovations. Advanced technologies such as 3D printing, computer-aided design (CAD), and simulation software have revolutionized the way injection moulding parts are designed and produced.
3D printing enables rapid prototyping, allowing manufacturers to test and refine their designs before committing to large-scale production. This reduces the likelihood of costly errors and ensures that the final product meets the required specifications. Additionally, CAD software allows for precise design of the moulds, ensuring that every detail is accounted for in the production process.
Simulation software has also improved precision by allowing engineers to predict how the plastic material will behave during the injection process. This helps optimize the design and production parameters, reducing defects and ensuring the final product meets the desired quality standards.
Real-World Applications: Industries Benefiting from Injection Moulding Plastic Part
Injection moulding plastic part has found applications in numerous industries where precision is essential. In the automotive sector, injection moulding is used to produce lightweight, durable components such as dashboard parts, interior trims, and engine components. The ability to create complex shapes and parts with tight tolerances makes it ideal for these applications.
In the medical industry, injection moulding plastic part is used to produce a variety of components for medical devices, including syringe parts, respiratory devices, and diagnostic equipment. These parts must meet stringent quality standards and be produced with high precision to ensure safety and functionality.
The electronics industry also relies heavily on injection moulding plastic part for producing intricate electrical components, such as connectors, housings, and protective covers. The ability to create parts with fine details and tight tolerances ensures that these components function correctly and efficiently.
Challenges and Solutions in Injection Moulding Plastic Part for Precision Engineering
While injection moulding plastic part offers numerous advantages, there are challenges that manufacturers must address. One of the main challenges is the high upfront cost of tooling and mould design. However, this cost is often offset by the efficiency and cost-effectiveness of large-scale production runs.
Another challenge is material limitations. Not all plastics are suitable for injection moulding, and some materials may require additional processing or specific mould designs. However, ongoing advancements in material science are expanding the range of plastics that can be used in injection moulding, making it even more versatile.
Tooling wear and the need for precision maintenance are also factors to consider. Ensuring that the moulds are well-maintained and regularly inspected helps mitigate these issues, ensuring high-quality results and reducing the risk of defects.
Future Outlook: The Growing Potential of Injection Moulding Plastic Part in Precision Engineering
Looking ahead, injection moulding plastic part is poised to continue its growth in precision engineering. As industries demand more complex designs and tighter tolerances, the need for advanced injection moulding technologies will only increase. Innovations in material science, automation, and digital technologies will continue to drive improvements in precision, cost-efficiency, and production speed.
The future of injection moulding in precision engineering is bright, with applications expanding in fields such as aerospace, robotics, and even consumer electronics. Manufacturers that embrace these technological advancements will be well-positioned to lead the way in precision manufacturing.
Conclusion: Injection Moulding Plastic Part – A Key to the Future of Precision Engineering
Injection moulding plastic part is a critical technology that will continue to shape the future of precision engineering. Its ability to produce high-quality, precise, and complex parts at scale makes it indispensable across industries. With ongoing technological advancements, injection moulding will only become more efficient and versatile, enabling even greater innovation and growth in precision engineering.