- March 25, 2025
- Posted by: feinuojixie
- Category: Injection Molding News
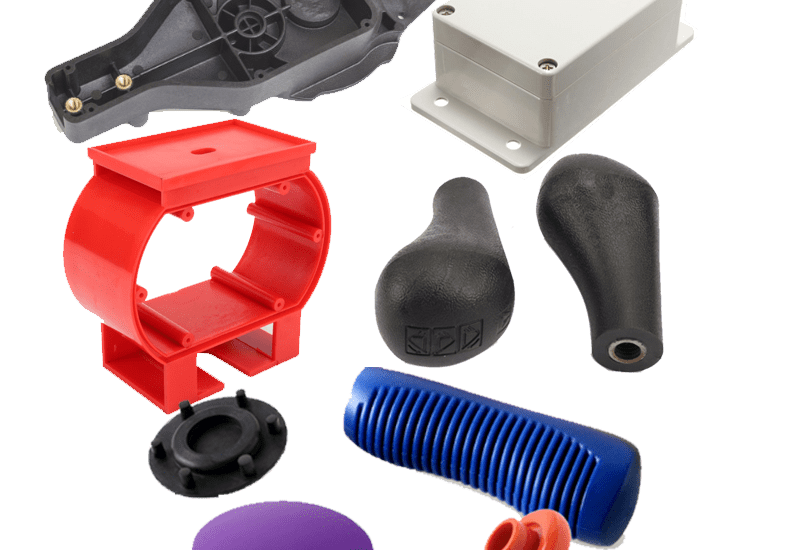
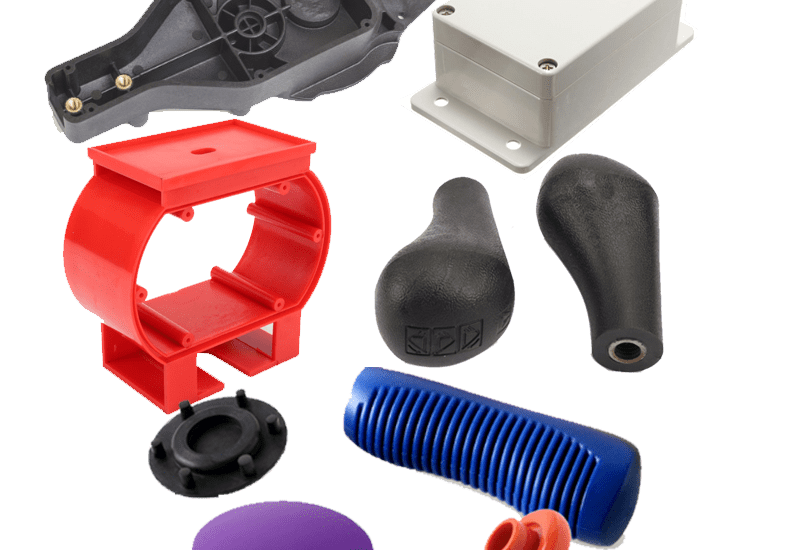
ABS injection moulding has revolutionized modern manufacturing by offering a cost-effective, durable, and versatile solution for producing high-quality plastic components. As a widely used thermoplastic, ABS (Acrylonitrile Butadiene Styrene) combines strength, impact resistance, and flexibility, making it an ideal material for various industries. Whether in automotive, electronics, or consumer goods, ABS injection moulding provides manufacturers with the ability to create complex, precision-engineered parts while maintaining production efficiency. This article explores why ABS injection moulding is a game-changer, highlighting its advantages, applications, and future potential.
Understanding ABS Injection Moulding
ABS injection moulding is a widely used process in plastic manufacturing that involves injecting molten ABS material into a mould cavity. Once cooled and solidified, the final product takes on the desired shape with high precision and durability. ABS, short for Acrylonitrile Butadiene Styrene, is a thermoplastic polymer known for its excellent impact resistance, toughness, and ease of processing. These properties make it a preferred choice for injection moulding across multiple industries.
Compared to other plastics, ABS stands out due to its balanced combination of strength, flexibility, and affordability. It can be easily moulded into intricate designs while maintaining structural integrity, making it ideal for producing components that require both durability and aesthetic appeal.
Superior Material Properties of ABS
One of the key reasons ABS injection moulding is a game-changer is the exceptional material properties of ABS. These include:
-
High Strength and Impact Resistance: ABS is known for its toughness, making it highly resistant to physical impact and mechanical stress. This is particularly beneficial for applications where durability is essential.
-
Lightweight Yet Strong: Despite its robustness, ABS remains lightweight, allowing for easy handling and reducing the overall weight of finished products.
-
Excellent Thermal and Chemical Resistance: ABS can withstand moderate heat and exposure to various chemicals, making it suitable for both indoor and outdoor applications.
-
Dimensional Stability: Once moulded, ABS maintains its shape with minimal warping, ensuring consistent product quality.
These properties make ABS an excellent choice for products that require longevity and reliability.
Cost-Effective and Scalable Production
One of the biggest advantages of ABS injection moulding is its cost-effectiveness. The process allows manufacturers to produce high volumes of components at a relatively low cost due to several factors:
-
Efficient Mass Production: Injection moulding is highly scalable, making it ideal for large production runs without compromising quality.
-
Minimal Material Waste: Excess ABS from the moulding process can be recycled and reused, reducing waste and cutting costs.
-
Faster Production Cycles: The automated nature of injection moulding ensures rapid production speeds, meeting high demand efficiently.
Because of these factors, ABS injection moulding is a preferred choice for businesses looking to optimize their manufacturing costs while maintaining superior product quality.
Versatility in Industry Applications
ABS injection moulding is used across various industries due to its adaptability and reliability. Some of the most notable applications include:
-
Automotive Industry: ABS is extensively used in manufacturing car interiors, dashboards, trim panels, and other components that require both durability and aesthetic appeal.
-
Electronics Industry: Many consumer electronics, such as laptop casings, remote controls, and keyboard frames, rely on ABS injection moulding for its insulating properties and mechanical strength.
-
Consumer Goods: Everyday products like plastic housings for appliances, luggage, and toys are made using ABS due to its balance of strength and cost-efficiency.
-
Medical and Industrial Equipment: ABS is also found in medical devices, protective gear, and industrial equipment where durability and hygiene are essential.
The ability of ABS injection moulding to cater to such a wide range of applications underscores its importance in modern manufacturing.
Customization and Aesthetic Benefits
Another reason ABS injection moulding is a game-changer is its flexibility in customization. ABS can be easily modified to achieve different colors, textures, and surface finishes, making it ideal for products that require an appealing visual appearance. Some notable advantages include:
-
Wide Range of Colors: ABS can be pre-colored or painted after moulding to match specific design requirements.
-
Surface Finishing Options: From glossy to matte finishes, ABS injection moulding allows for various surface textures to enhance product aesthetics.
-
Easy Printing and Coating: Logos, labels, and protective coatings can be applied to ABS surfaces without difficulty, improving branding and durability.
These features make ABS injection moulding a preferred choice for designers and manufacturers looking to create visually appealing and functional products.
Sustainability and Recycling Advantages
As sustainability becomes a growing concern, ABS injection moulding offers environmental benefits that contribute to reducing plastic waste.
-
Recyclability: ABS is a thermoplastic, meaning it can be melted and reshaped multiple times without significant degradation. This allows manufacturers to recycle unused ABS material efficiently.
-
Energy-Efficient Processing: The injection moulding process is designed to minimize energy consumption while maximizing output.
-
Eco-Friendly Alternatives: Some manufacturers are now incorporating bio-based or recycled ABS into their moulding processes to further reduce their environmental footprint.
With these sustainable practices, ABS injection moulding continues to evolve as an environmentally responsible manufacturing solution.
Challenges and Considerations
Despite its many advantages, ABS injection moulding also has some limitations that manufacturers need to consider:
-
Heat Sensitivity: While ABS has good thermal resistance, excessive heat exposure can cause deformation, limiting its use in high-temperature applications.
-
Environmental Impact: Although recyclable, ABS is still a petroleum-based plastic, meaning its production contributes to carbon emissions. However, advances in recycling technologies are addressing this issue.
-
Potential Chemical Sensitivity: Certain chemicals, such as strong acids and solvents, can degrade ABS over time, making material selection crucial for specific applications.
By optimizing processing conditions and selecting the right formulations, manufacturers can mitigate these challenges and maximize the benefits of ABS injection moulding.
Future Trends in ABS Injection Moulding
The future of ABS injection moulding is promising, with continuous advancements aimed at enhancing its performance and sustainability. Some key trends include:
-
Improved ABS Formulations: Ongoing research is developing ABS variants with enhanced heat resistance, UV stability, and eco-friendly properties.
-
Smart Injection Moulding: Automation and AI-driven quality control are making the process more efficient and precise, reducing defects and production costs.
-
Sustainable Manufacturing Practices: Increased use of recycled ABS and bio-based plastics is helping to make injection moulding more environmentally friendly.
-
3D Printing Integration: Combining ABS injection moulding with additive manufacturing techniques is allowing for rapid prototyping and mass customization.
These innovations will further solidify ABS injection moulding as a leading technology in the manufacturing industry.
Conclusion
ABS injection moulding has revolutionized modern manufacturing by offering a powerful combination of strength, versatility, and cost-efficiency. Its widespread use across industries—from automotive and electronics to consumer goods and medical equipment—demonstrates its unmatched reliability. Additionally, advancements in sustainable practices and material formulations are making ABS injection moulding an even more attractive option for future production needs.
For businesses looking to enhance product quality while optimizing costs, ABS injection moulding remains an indispensable technology that continues to shape the future of plastic manufacturing.