- April 27, 2025
- Posted by: feinuojixie
- Category: Injection Molding News
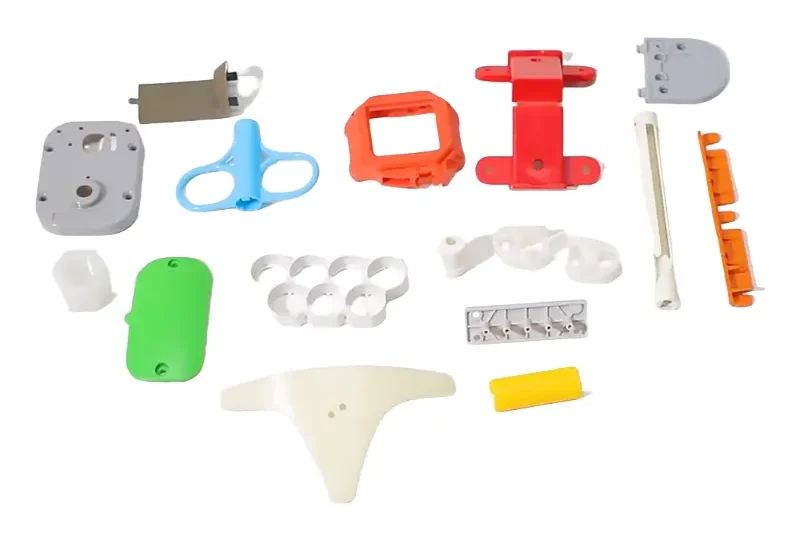
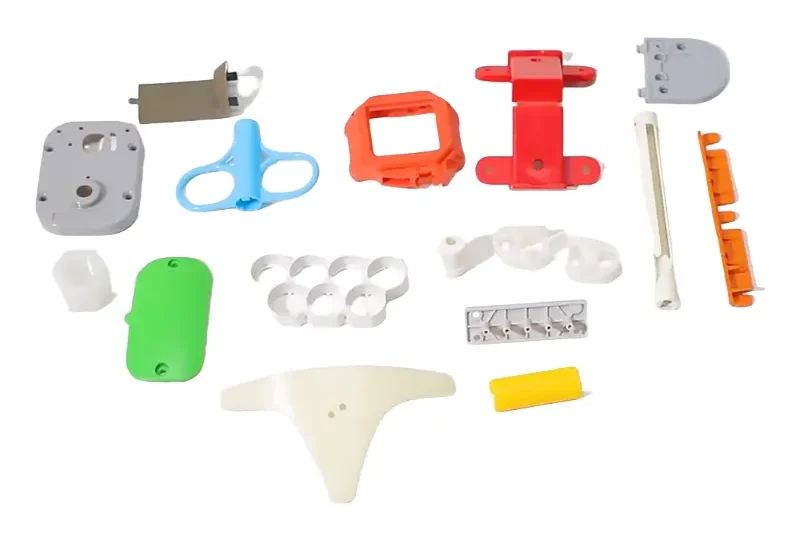
In the fast-paced world of modern manufacturing, achieving greater efficiency is a constant goal. At the heart of this drive for productivity lies a crucial yet often overlooked element: injection parts. These precision-engineered components serve as the foundation of countless products across industries, from automotive to medical devices. Injection parts offer a unique combination of reliability, scalability, and cost-effectiveness that enables manufacturers to streamline their operations while maintaining exceptional quality standards. As technology advances and production demands continue to grow, the role of injection parts in ensuring efficient manufacturing has never been more vital.
Understanding Injection Parts and Their Manufacturing Process
Injection parts are components created by injecting molten material into a mold cavity, allowing it to cool and solidify into a precise shape. This method, commonly known as injection molding, is highly valued for its ability to produce complex geometries with incredible accuracy. The process begins with selecting a suitable material, usually a polymer, heating it until it becomes liquid, and then forcing it under pressure into a custom-designed mold. After cooling, the mold opens to release the finished injection part. Thanks to this streamlined and highly repeatable process, manufacturers can produce large quantities of identical parts with minimal variation, setting the standard for mass production.
The Critical Role of Injection Parts in Modern Production Lines
Injection parts play a pivotal role in the efficiency of today’s production lines. Their consistency ensures that every assembled product meets the same rigorous standards, reducing the risk of defects and recalls. Because injection parts are manufactured with exacting precision, they fit together seamlessly during assembly, which minimizes delays and quality issues. In high-volume industries like automotive and electronics, where every second counts, the ability of injection parts to speed up production cycles is a significant competitive advantage. Their reliability not only boosts operational efficiency but also enhances brand reputation through consistent product quality.
Material Advantages in Injection Parts
The success of injection parts in manufacturing also stems from the wide range of materials available for their production. Thermoplastics, known for their flexibility and recyclability, are ideal for parts requiring durability and lightweight properties. Thermosetting plastics offer greater heat and chemical resistance, making them suitable for high-performance applications. Advanced composites and specialized polymers further expand the possibilities, allowing manufacturers to tailor injection parts to specific functional requirements. By carefully selecting materials, companies can ensure that their injection parts withstand demanding operating conditions, extend product lifespans, and meet industry-specific standards.
Injection Parts Driving Cost Efficiency
One of the most compelling reasons for the widespread adoption of injection parts is their contribution to cost efficiency. Once a mold is created, the per-unit production cost of injection parts drops significantly, making it ideal for large-scale manufacturing. The process generates minimal waste because excess material can often be recycled or reused. Additionally, the speed of production means that more parts can be made in less time, further driving down operational costs. Through the use of injection parts, manufacturers can optimize their resource usage, reduce overhead, and maintain competitive pricing without compromising on quality.
Customization and Design Flexibility of Injection Parts
Injection parts offer unmatched design flexibility, enabling manufacturers to create customized solutions for a wide range of applications. The molding process supports intricate designs, tight tolerances, and complex shapes that would be difficult or impossible to achieve with other manufacturing methods. Custom features such as textured surfaces, embedded components, or multi-material designs can be seamlessly integrated into the production of injection parts. This flexibility allows companies to innovate quickly, adapt products to changing market needs, and differentiate themselves through unique product offerings without sacrificing the benefits of mass production.
Applications Across Key Industries
The versatility of injection parts is evident across numerous industries. In the automotive sector, injection parts are used for everything from dashboard components to intricate fuel system parts, offering strength and weight savings critical for vehicle efficiency. In healthcare, precision injection parts are essential for devices like syringes, diagnostic equipment, and surgical instruments, where accuracy and reliability are non-negotiable. Consumer electronics rely on injection parts for casings, connectors, and internal structures that require fine detail and durability. Even in everyday consumer goods, from kitchen appliances to sporting equipment, injection parts ensure affordability, functionality, and aesthetic appeal.
Future Trends in Injection Parts and Manufacturing Efficiency
The future of injection parts is intertwined with emerging manufacturing technologies and materials. Micro-molding, a process for creating extremely small and precise injection parts, is opening new possibilities in electronics and medical devices. Sustainable innovations, such as bio-based and biodegradable polymers, are addressing environmental concerns while maintaining performance standards. Meanwhile, the integration of smart manufacturing techniques like automation, AI-driven quality control, and real-time monitoring is enhancing the efficiency of injection part production. As these trends evolve, injection parts will continue to be at the forefront of efficient, high-quality, and sustainable manufacturing practices.
Injection Parts as the Foundation of Tomorrow’s Manufacturing
Injection parts have firmly established themselves as the backbone of efficient manufacturing. Their precision, cost-effectiveness, and versatility make them indispensable across industries. As technology advances and market demands grow, the importance of injection parts will only increase, driving innovation and setting new benchmarks for quality and efficiency. Manufacturers who leverage the full potential of injection parts will not only meet today’s challenges but also lead the way into a smarter, more sustainable industrial future.