- May 5, 2025
- Posted by: feinuojixie
- Category: Injection Molding News
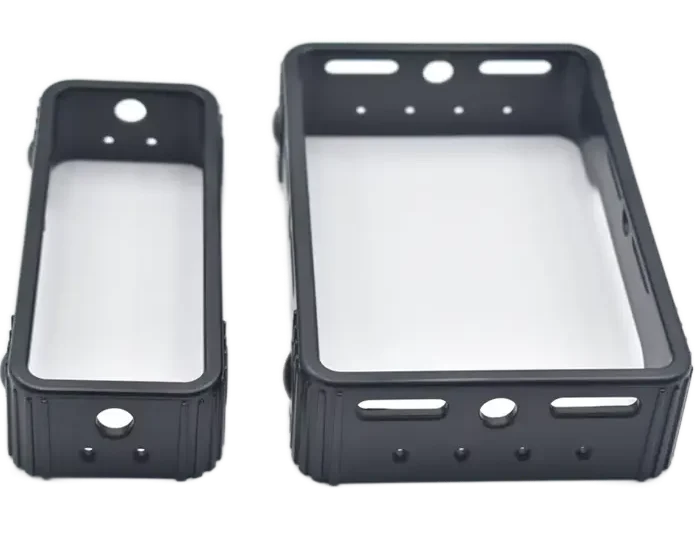
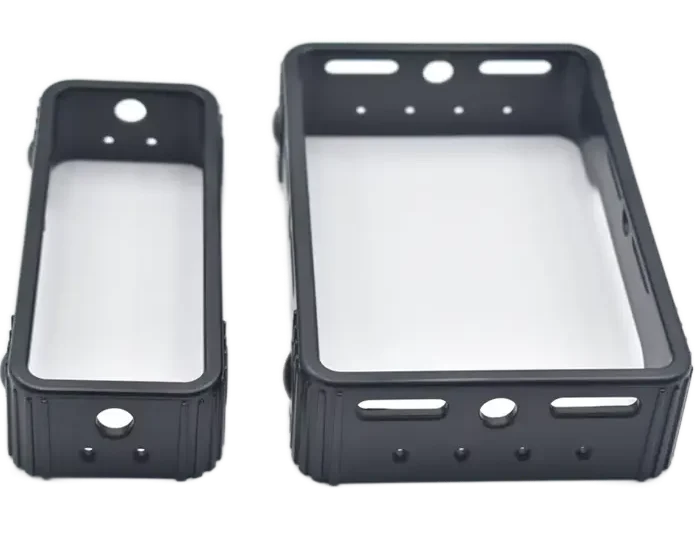
The manufacturing industry has always relied on innovative techniques to create high-quality, durable products. Among these techniques, injection molding has long been a cornerstone of efficiency and precision. However, with the rise of large part injection molding, the landscape is experiencing a profound transformation. Large part injection molding involves producing bigger, more complex parts with the same speed and cost-effectiveness that traditionally smaller parts could be made. This evolution is revolutionizing industries from automotive to aerospace, where manufacturers are increasingly turning to this method to meet modern demands for larger, more intricate components. In this article, we will explore how large part injection molding is shaping the future of manufacturing and why it’s becoming a go-to solution for many industries.
Understanding Large Part Injection Molding
Large part injection molding refers to the process of molding larger-than-usual plastic components by injecting molten material into custom-designed molds under high pressure. Unlike traditional molding, which is typically used for smaller parts, large part molding requires specialized equipment capable of handling the size and complexity of the molds. This advanced technique can produce parts ranging from automotive panels to industrial machinery components, with intricate designs and precise detailing.
The key to its success lies in technological advancements, particularly in mold design, material selection, and machine capabilities. Innovations such as multi-cavity molds, high-tonnage presses, and the ability to use a wider variety of materials have made it possible to scale the molding process for much larger parts without sacrificing quality. In addition, modern techniques allow for the molding of parts with complex geometries, which was once considered impossible using traditional molding methods.
Benefits of Large Part Injection Molding in Modern Manufacturing
One of the most significant advantages of large part injection molding is its ability to drive cost-efficiency. Because the process minimizes waste and optimizes material usage, it is far more cost-effective than alternative manufacturing methods like machining or casting. In large part molding, the material is injected into the mold with precision, ensuring that only the necessary amount of material is used and reducing waste.
In addition to cost savings, large part injection molding greatly speeds up production cycles. In today’s fast-paced manufacturing environment, time is of the essence, and the ability to produce large parts quickly is a game-changer. The process can handle large volumes of parts in shorter timeframes, which means that manufacturers can meet increasing demands without delays. This efficiency also helps reduce overhead costs and improve overall profitability.
Precision is another standout benefit of large part injection molding. Despite the larger size of the components being produced, the technology allows for high levels of accuracy and consistency. Whether it’s an intricate automotive dashboard or a complex aerospace part, large part molding can deliver uniform quality across thousands of units, ensuring that each product meets the same exacting standards.
The Industries Benefiting from Large Part Injection Molding
Several industries have been quick to adopt large part injection molding due to the significant advantages it offers in production speed, cost savings, and product quality.
Automotive Industry: Large part injection molding has transformed the production of various automotive components, from bumpers and dashboards to door panels and trim parts. Manufacturers in the automotive industry are able to produce lightweight, durable, and precisely molded parts that meet the highest safety standards. This technology also supports the ongoing trend toward electric vehicles, which require large, high-performance plastic components.
Aerospace Industry: The aerospace sector is another area where large part injection molding is making waves. Complex and high-strength parts used in aircraft, such as engine components, interior panels, and structural elements, are often produced through this method. Large part injection molding allows for the creation of intricate designs that cannot be achieved with traditional manufacturing techniques, all while maintaining the durability and lightweight properties necessary for aerospace applications.
Consumer Goods: In the consumer goods sector, manufacturers are using large part injection molding to produce everything from large plastic containers and furniture to complex appliances. The ability to quickly produce large quantities of uniform, durable products has made large part molding essential for meeting consumer demand in a competitive market.
Overcoming Challenges in Large Part Injection Molding
Despite its many advantages, large part injection molding does present a few challenges. One of the main concerns is the technical limitations related to mold size and material. Creating molds that can accommodate large parts requires advanced engineering and specialized equipment, which can increase the initial setup costs. Additionally, ensuring that the molding process remains stable and efficient when dealing with large parts can be more challenging than with smaller components.
However, the industry has responded to these challenges with innovations that have improved the process. For example, new materials with enhanced strength-to-weight ratios are being developed, enabling manufacturers to create large parts that are both strong and lightweight. Moreover, improvements in mold design, such as modular molds and multi-cavity systems, have made it easier to produce large parts with complex geometries.
Automation is another key area of innovation, with robotic arms and automated systems taking over tasks such as loading, unloading, and finishing parts. This reduces human error and increases production efficiency, making large part injection molding even more reliable and cost-effective.
Future Trends in Large Part Injection Molding
Looking ahead, the future of large part injection molding is filled with exciting possibilities. Automation and artificial intelligence are playing an increasingly important role in the molding process. AI-powered systems can now monitor every step of the molding cycle, adjusting parameters in real-time to ensure optimal results. This level of precision and adaptability will lead to even greater efficiency and consistency in large part production.
Another exciting development is the potential integration of 3D printing and additive manufacturing technologies with traditional injection molding. 3D printing could be used to create highly detailed and customized molds for large parts, reducing lead times and offering more design flexibility. Additionally, the ability to use additive manufacturing for prototyping can speed up the product development cycle, helping manufacturers bring new designs to market faster.
The Future of Large Part Injection Molding
In conclusion, large part injection molding is undoubtedly revolutionizing the manufacturing industry. Its ability to produce large, complex parts with speed, precision, and cost-efficiency makes it a game-changing technology for many sectors. While challenges remain, ongoing innovations in materials, mold design, and automation continue to push the boundaries of what is possible. As industries continue to demand larger, more intricate components, large part injection molding will undoubtedly play an even greater role in shaping the future of manufacturing.