- May 2, 2025
- Posted by: feinuojixie
- Category: Injection Molding News
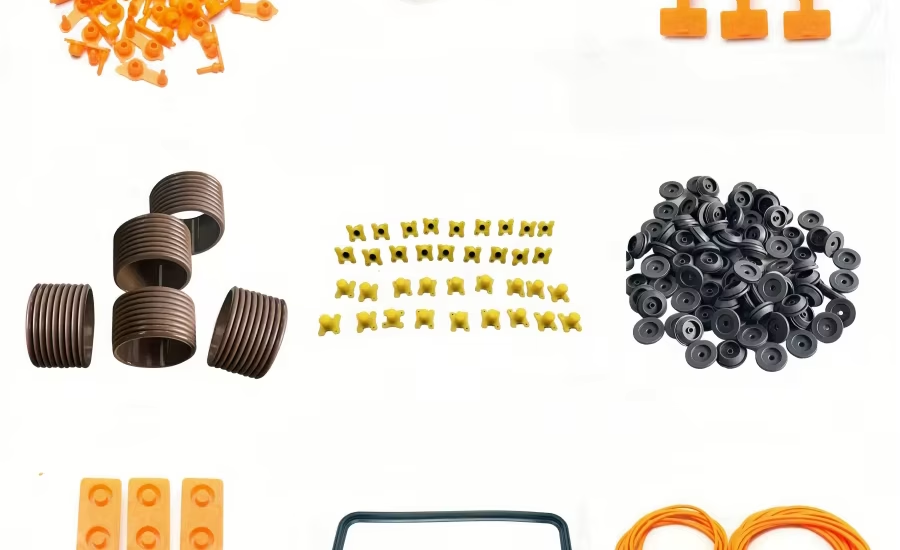
In the fast-paced world of modern manufacturing, countless components operate behind the scenes to power industries, streamline production, and deliver innovative products to consumers. Among these crucial elements, plastic injection molded parts stand out as silent heroes. They are embedded in nearly every sector, from automotive and medical devices to electronics and consumer goods. Despite their omnipresence, the significance of plastic injection molded parts often goes unrecognized. Their precision, versatility, and cost-efficiency make them the preferred choice for manufacturers aiming to achieve high-quality outcomes at scale. As we delve deeper into the journey of plastic injection molded parts, it becomes clear why they form the very backbone of today’s manufacturing success stories.
The Evolution of Plastic Injection Molded Parts in Manufacturing
The story of plastic injection molded parts begins in the early 20th century with the invention of the first injection molding machine. Initially used for simple items like buttons and combs, plastic injection molding has evolved dramatically with advances in materials, design capabilities, and machine technology. Modern manufacturing relies on highly sophisticated injection molding processes that allow for the creation of complex, precise components at remarkable speeds. Over the decades, plastic injection molded parts have transitioned from basic consumer goods to critical components in high-tech industries, reflecting the constant innovation driving manufacturing forward.
Key Advantages of Plastic Injection Molded Parts
One of the primary reasons plastic injection molded parts are so widely adopted is their array of advantages over alternative manufacturing methods. They offer unparalleled design flexibility, allowing engineers to create intricate shapes and detailed features with ease. The process is highly repeatable, ensuring consistent quality across large production runs. Moreover, plastic injection molded parts are cost-effective, especially at high volumes, thanks to minimized material waste and reduced labor costs. Their durability, lightweight nature, and resistance to chemicals and corrosion make them suitable for a wide range of demanding applications. These benefits combine to make plastic injection molded parts indispensable in industries striving for innovation and efficiency.
How Plastic Injection Molded Parts Enable Mass Production
The ability to mass-produce identical parts quickly and reliably is a cornerstone of modern manufacturing, and plastic injection molded parts make this possible. Once a mold is created, production cycles are fast, with minimal human intervention required. This scalability allows companies to meet the demands of global markets without sacrificing quality or increasing costs. Whether producing millions of smartphone housings or thousands of automotive interior components, plastic injection molded parts deliver the consistency and speed that manufacturers need to stay competitive. Their role in mass production is not just supportive but foundational, enabling economies of scale that benefit both producers and consumers.
Plastic Injection Molded Parts in Automotive Innovation
The automotive industry has long been a champion of plastic injection molded parts, using them to replace heavier metal components and improve vehicle performance. From dashboard panels and bumpers to under-the-hood components, plastic injection molded parts contribute to lighter vehicles, leading to better fuel efficiency and lower emissions. In addition to weight savings, these parts offer superior design flexibility, enabling the creation of aerodynamic shapes and integrated features that enhance safety and aesthetics. As the automotive industry moves toward electric vehicles and sustainable mobility, the importance of plastic injection molded parts continues to grow, supporting innovation at every turn.
Medical Advancements Powered by Plastic Injection Molded Parts
In the medical field, precision, sterility, and reliability are non-negotiable, and plastic injection molded parts meet these stringent requirements. They are used to create a wide range of products, from syringes and diagnostic devices to surgical instruments and implantable components. The ability to produce highly detailed, contamination-free parts ensures that medical devices perform as intended, safeguarding patient health. Advances in biocompatible plastics and micro-molding techniques have expanded the applications of plastic injection molded parts in healthcare, making them essential tools in the fight against disease and in improving patient outcomes worldwide.
Consumer Electronics and the Precision of Plastic Injection Molded Parts
The sleek designs and complex functionalities of today’s consumer electronics would not be possible without plastic injection molded parts. Smartphones, laptops, wearable devices, and home appliances all rely on precision-molded components to house sensitive electronic assemblies, provide user interfaces, and ensure durability. Plastic injection molded parts allow manufacturers to achieve the tight tolerances and intricate designs that consumers expect, while also enabling faster product development cycles. As electronics continue to evolve toward greater miniaturization and multifunctionality, the demand for high-quality plastic injection molded parts will only increase.
The Sustainability of Plastic Injection Molded Parts
As industries worldwide shift toward more sustainable practices, plastic injection molded parts are also undergoing a green transformation. Manufacturers are increasingly using recycled and bio-based plastics to reduce the environmental impact of their products. Additionally, the efficiency of the injection molding process itself minimizes material waste, and innovative design strategies allow for lighter components that require less energy to produce and transport. Research into biodegradable plastics and closed-loop recycling systems further enhances the sustainability of plastic injection molded parts, positioning them as key contributors to the circular economy of the future.
Future Trends in Plastic Injection Molded Parts for Manufacturing
The future of plastic injection molded parts in manufacturing looks bright, fueled by technological advancements and evolving market needs. Smart materials that respond to environmental changes, automation that enhances production efficiency, and digital tools like simulation software are transforming the way plastic injection molded parts are designed and produced. Emerging technologies such as metal-to-plastic conversion and additive manufacturing integration promise to push the boundaries of what is possible. As manufacturers embrace Industry 4.0 principles, plastic injection molded parts will continue to adapt and thrive, driving innovation across all sectors.
Why Plastic Injection Molded Parts Will Remain Indispensable
Plastic injection molded parts are far more than just components; they are the building blocks of modern manufacturing. Their unmatched versatility, efficiency, and ability to meet the demands of diverse industries make them an irreplaceable part of the global production landscape. As technology advances and markets evolve, the importance of plastic injection molded parts will only grow stronger. Recognizing their value today ensures that industries can continue to innovate and thrive well into the future.